Thin films are layers of material ranging from fractions of a nanometer to several micrometers in thickness, deposited onto a substrate to enhance its properties or functionality. Sputtering is a widely used thin-film deposition technique where atoms from a solid target material are ejected into a gas phase due to bombardment by high-energy ions, typically from a noble gas like argon. These ejected atoms then deposit onto a substrate, forming a thin film. This process occurs in a vacuum chamber, ensuring controlled conditions for uniform and precise deposition. Sputtering is favored for its ability to produce high-quality, dense films with excellent adhesion and low residual stress, making it suitable for applications in electronics, optics, and coatings.
Key Points Explained:
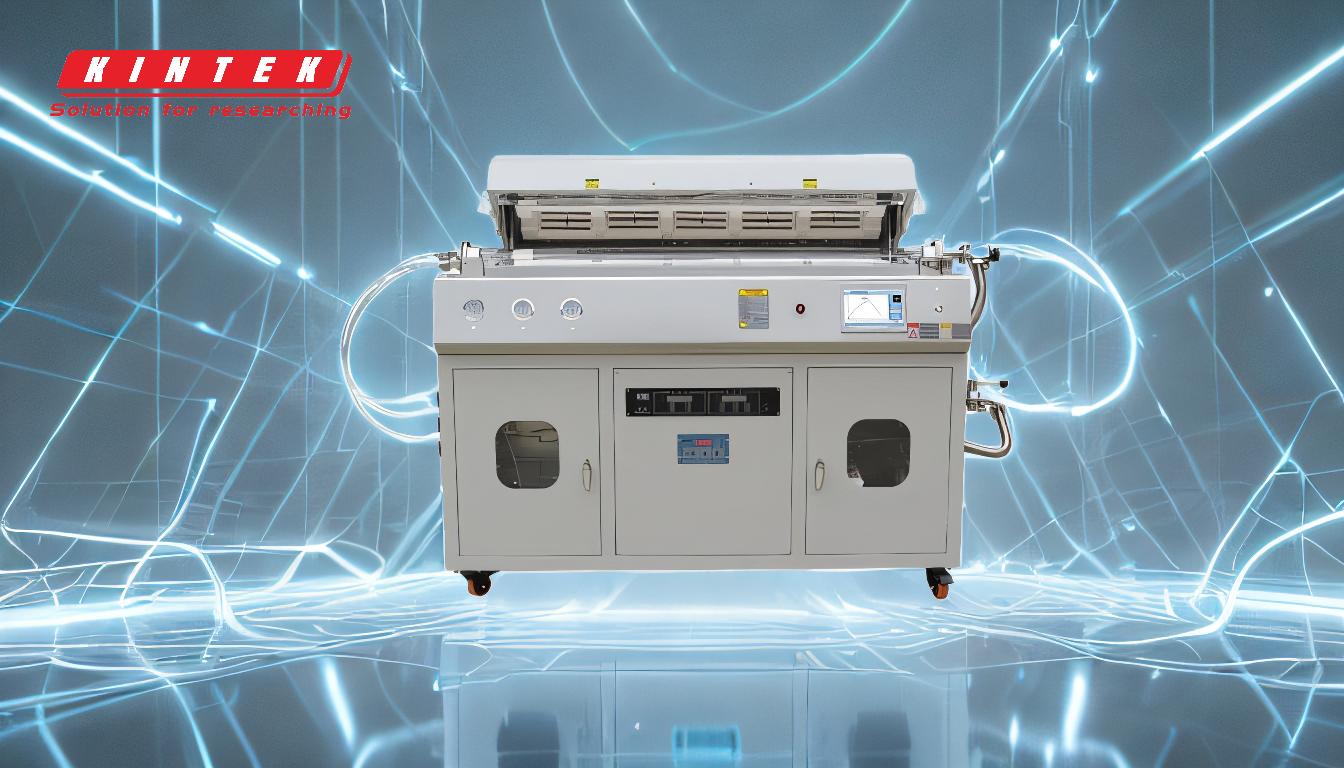
-
What is Thin Film Deposition?
- Thin film deposition involves creating a thin layer of material on a substrate to modify its surface properties.
- Applications include semiconductor devices, optical coatings, and protective layers.
- The thickness of the film can range from nanometers to micrometers, depending on the application.
-
Overview of Sputtering Technique:
- Sputtering is a physical vapor deposition (PVD) technique.
- It involves bombarding a target material with high-energy ions, typically from a noble gas like argon, to eject atoms from the target.
- The ejected atoms travel through a vacuum chamber and deposit onto a substrate, forming a thin film.
-
Components of Sputtering System:
- Vacuum Chamber: Provides a controlled environment to minimize contamination and ensure uniform deposition.
- Target Material: The source material from which atoms are ejected.
- Substrate: The surface onto which the thin film is deposited.
- Noble Gas (e.g., Argon): Ionized to form plasma, which bombards the target material.
- Electrodes: Generate the electric field necessary to ionize the gas and accelerate ions toward the target.
-
Process Steps in Sputtering:
- Step 1: Introduce a controlled amount of inert gas (e.g., argon) into the vacuum chamber.
- Step 2: Apply a high voltage between the target (cathode) and the substrate (anode) to generate a plasma.
- Step 3: Ionize the gas atoms, creating positively charged ions.
- Step 4: Accelerate the ions toward the target material, causing collisions that eject target atoms.
- Step 5: The ejected atoms travel through the chamber and deposit onto the substrate, forming a thin film.
-
Advantages of Sputtering:
- Uniform Deposition: Sputtering produces highly uniform films, even on complex geometries.
- Precise Control: Film thickness can be precisely controlled by adjusting deposition time.
- Low Residual Stress: Films deposited via sputtering exhibit low residual stress, enhancing durability.
- Versatility: Suitable for a wide range of materials, including metals, alloys, and ceramics.
-
Types of Sputtering:
- DC Sputtering: Uses direct current to generate plasma, ideal for conductive materials.
- RF Sputtering: Uses radio frequency for non-conductive materials.
- Magnetron Sputtering: Incorporates magnetic fields to enhance ionization efficiency, improving deposition rates and film quality.
-
Applications of Sputtering:
- Electronics: Used in the fabrication of semiconductors, integrated circuits, and thin-film transistors.
- Optics: Produces anti-reflective coatings, mirrors, and optical filters.
- Coatings: Provides wear-resistant and corrosion-resistant layers for tools and components.
- Energy: Used in solar cells and battery technologies.
-
Historical Context:
- Sputtering was first commercialized by Thomas Edison in 1904 for applying thin metal layers to wax phonograph recordings.
- The technique has since evolved, with advancements like magnetron sputtering improving efficiency and versatility.
-
Challenges and Considerations:
- Energy Efficiency: Sputtering can be energy-intensive due to the need for high vacuum and plasma generation.
- Material Compatibility: Not all materials are suitable for sputtering, particularly those with low melting points.
- Cost: The equipment and operational costs can be high, especially for large-scale production.
-
Future Trends in Sputtering:
- Development of hybrid techniques combining sputtering with other deposition methods.
- Advances in plasma technology to improve deposition rates and reduce energy consumption.
- Increased use of sputtering in emerging fields like flexible electronics and nanotechnology.
In summary, sputtering is a versatile and precise thin-film deposition technique that plays a critical role in modern technology. Its ability to produce high-quality, uniform films makes it indispensable in industries ranging from electronics to optics. Understanding the principles, components, and applications of sputtering is essential for anyone involved in thin-film technology or equipment procurement.
Summary Table:
Aspect | Details |
---|---|
Definition | Sputtering is a physical vapor deposition (PVD) technique for thin films. |
Process | Ejects atoms from a target material using high-energy ions in a vacuum. |
Key Components | Vacuum chamber, target material, substrate, noble gas, electrodes. |
Advantages | Uniform deposition, precise control, low residual stress, versatility. |
Types | DC, RF, and magnetron sputtering. |
Applications | Electronics, optics, coatings, energy (solar cells, batteries). |
Challenges | Energy-intensive, material compatibility, high costs. |
Future Trends | Hybrid techniques, improved plasma tech, flexible electronics. |
Discover how sputtering can enhance your projects—contact our experts today!