A two-plate mold is the most widely used type of injection mold in plastic manufacturing. It consists of a single parting plane that splits the mold into two halves, typically referred to as the cavity side and the core side. This design allows for the efficient ejection of the molded part along with the runner and gate system, which are located in the parting plane. Two-plate molds are versatile, cost-effective, and suitable for producing a wide range of plastic parts, making them a standard choice in the industry.
Key Points Explained:
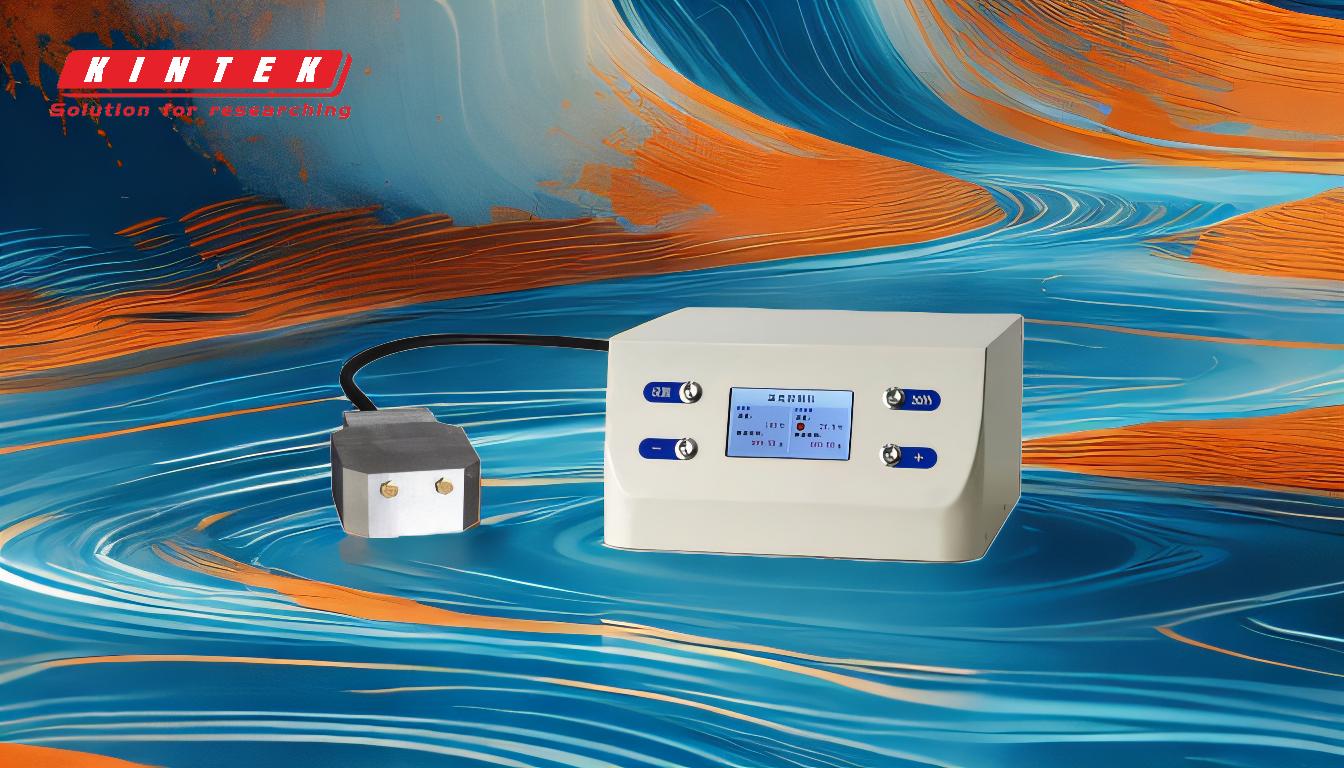
-
Basic Structure of a Two-Plate Mold:
- A two-plate mold consists of two main halves: the cavity side (stationary) and the core side (movable).
- The parting plane is the interface where these two halves meet and separate during the molding process.
- This simple structure makes it easy to manufacture, maintain, and operate.
-
Parting Plane and Its Role:
- The parting plane is the critical feature of a two-plate mold. It is the surface where the mold splits to eject the finished part.
- All features of the part, including the runner and gate system, must be designed to lie within this plane to ensure proper ejection.
- The parting plane also determines the mold's alignment and ensures the accuracy of the final product.
-
Runner and Gate System:
- In a two-plate mold, the runner (the channel that delivers molten plastic to the cavity) and the gate (the entry point into the cavity) are located in the parting plane.
- This design ensures that the runner and gate are ejected along with the part when the mold opens, simplifying the ejection process.
- The runner and gate system must be carefully designed to balance flow, minimize waste, and ensure consistent part quality.
-
Advantages of Two-Plate Molds:
- Simplicity: The straightforward design makes two-plate molds easier and cheaper to manufacture compared to more complex molds like three-plate molds.
- Versatility: They can be used for a wide range of part geometries and materials.
- Ease of Maintenance: With fewer moving parts, two-plate molds are easier to maintain and repair.
- Cost-Effectiveness: Lower manufacturing and operational costs make them ideal for high-volume production.
-
Applications of Two-Plate Molds:
- Two-plate molds are commonly used in industries such as automotive, consumer goods, electronics, and packaging.
- They are suitable for producing parts with simple to moderately complex geometries.
- Multi-cavity two-plate molds are often used for high-volume production of small parts, such as bottle caps or connectors.
-
Limitations of Two-Plate Molds:
- Limited flexibility for complex part designs that require undercuts or side actions.
- The runner and gate system must be manually or automatically trimmed after ejection, which can add to post-processing time and cost.
- Not ideal for parts that require a gate location away from the parting plane.
-
Comparison with Other Mold Types:
- Three-Plate Molds: Unlike two-plate molds, three-plate molds have an additional plate that allows for more complex gating options, such as center gating. However, they are more expensive and complex to operate.
- Hot Runner Molds: These molds eliminate the need for a runner system, reducing material waste. However, they are significantly more expensive and require precise temperature control.
In summary, a two-plate mold is a fundamental and widely used tool in plastic injection molding due to its simplicity, cost-effectiveness, and versatility. Its design, centered around a single parting plane, ensures efficient ejection of parts and runner systems, making it a reliable choice for many manufacturing applications. However, its limitations in handling complex part designs and the need for post-processing of runners and gates should be considered when selecting the appropriate mold type for a specific project.
Summary Table:
Aspect | Details |
---|---|
Structure | Two halves: cavity side (stationary) and core side (movable). |
Parting Plane | Interface for mold splitting and part ejection. |
Runner & Gate System | Located in the parting plane for easy ejection. |
Advantages | Simple, versatile, cost-effective, and easy to maintain. |
Applications | Automotive, consumer goods, electronics, and packaging industries. |
Limitations | Limited for complex designs; requires post-processing of runners and gates. |
Ready to optimize your plastic manufacturing process? Contact us today to learn more about two-plate molds!