Physical Vapor Deposition (PVD) is a widely used technique for depositing thin films, with thicknesses typically ranging from atomic layers (less than 10 Å) to several microns (µm). The specific thickness achieved depends on the application, whether it is for decorative purposes, functional coatings, or advanced technological uses. For decorative coatings, thinner films (around 0.2 µm) are common, while functional coatings, such as those used in electronics or wear-resistant applications, may require thicker films (up to 5 µm or more). The versatility of PVD allows for precise control over film thickness, making it suitable for a wide range of industries and applications.
Key Points Explained:
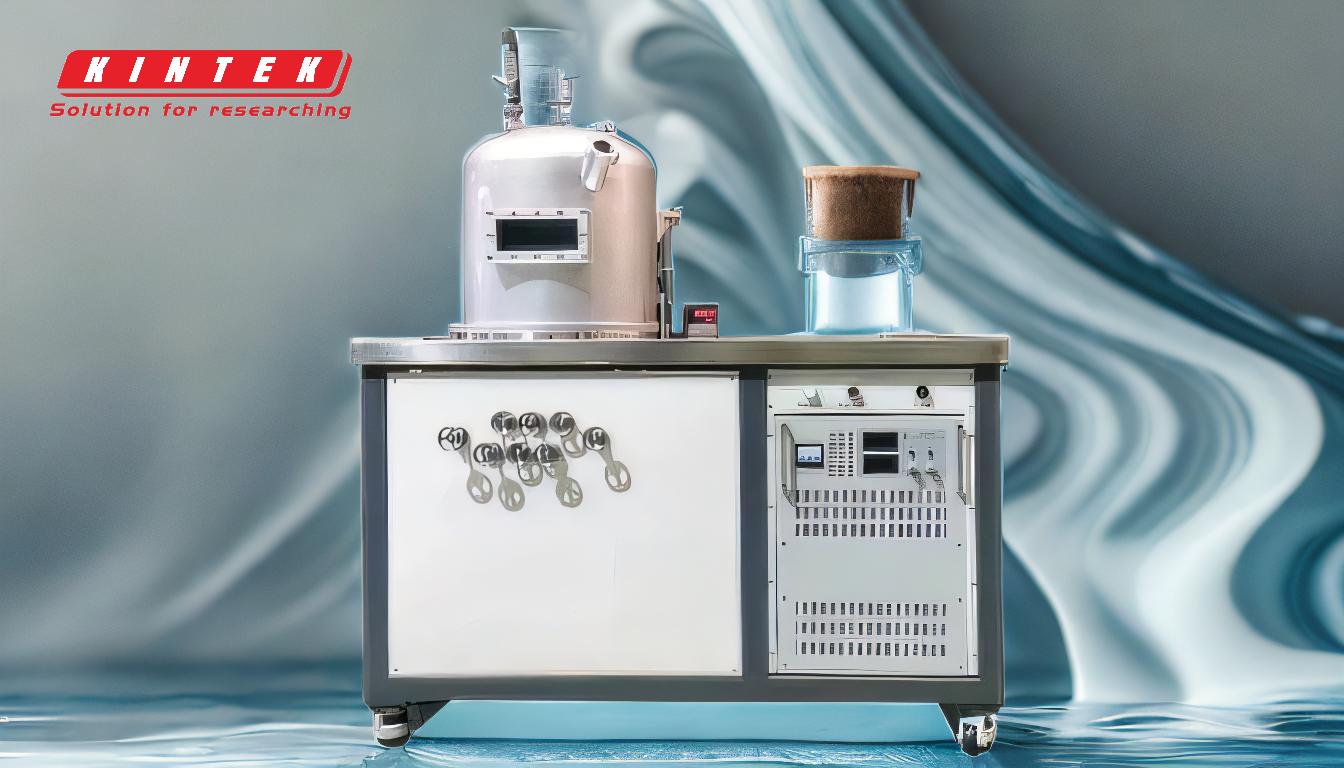
-
Range of Thin Film Thicknesses in PVD:
- Atomic Layers to Microns: PVD can deposit films ranging from atomic layers (less than 10 Å or 0.1 nm) to several microns (µm). This wide range allows PVD to be used in applications requiring ultra-thin films (e.g., semiconductors) as well as thicker coatings (e.g., wear-resistant layers).
- Typical Range: The most common thickness range for PVD coatings is between 0.2 µm and 5 µm. This range is suitable for both decorative and functional applications.
-
Decorative vs. Functional Coatings:
- Decorative Coatings: These are typically thinner, around 0.2 µm. Decorative coatings are often used in industries like jewelry, watches, and consumer electronics, where aesthetics are important. The thinness ensures a high-quality finish without adding significant bulk.
- Functional Coatings: These coatings are generally thicker, ranging from 1 µm to 5 µm or more. Functional coatings are used in applications where durability, wear resistance, or specific electrical properties are required. Examples include protective coatings on tools, medical devices, and electronic components.
-
Applications Influencing Thickness:
- Semiconductors and Electronics: In these fields, ultra-thin films (a few nanometers) are often required. PVD is capable of depositing films at this scale, making it ideal for creating thin layers in transistors, sensors, and other microelectronic devices.
- Wear-Resistant Coatings: For applications like cutting tools or engine components, thicker films (several microns) are necessary to provide adequate protection against wear and corrosion. PVD can achieve these thicknesses while maintaining high adhesion and uniformity.
-
Factors Affecting Thickness in PVD:
- Deposition Time: The longer the deposition process, the thicker the film. PVD allows for precise control over deposition time, enabling the creation of films with specific thicknesses.
- Material Properties: Different materials have different deposition rates. For example, metals may deposit faster than ceramics, affecting the final thickness.
- Substrate and Process Parameters: The type of substrate, temperature, pressure, and other process parameters can influence the thickness and quality of the deposited film.
-
Comparison with Other Deposition Methods:
- Chemical Vapor Deposition (CVD): Like PVD, CVD can deposit films ranging from a few nanometers to several microns. However, CVD often requires higher temperatures and may not be suitable for all substrates.
- Other Thin Film Techniques: Techniques like sputtering or evaporation (both PVD methods) can achieve similar thickness ranges, but PVD is often preferred for its ability to deposit high-quality films at lower temperatures.
-
Practical Considerations for Equipment and Consumable Purchasers:
- Application-Specific Requirements: When selecting PVD equipment or consumables, it is crucial to consider the desired film thickness and application. For example, if the goal is to create ultra-thin films for electronics, equipment with precise control over deposition rates and thickness is essential.
- Material Compatibility: Ensure that the PVD system is compatible with the materials you intend to deposit. Some materials may require specific process conditions to achieve the desired thickness and quality.
- Cost and Efficiency: Thicker films may require longer deposition times and more material, increasing costs. Balancing thickness requirements with cost-efficiency is important for both small-scale and large-scale production.
In summary, PVD offers a versatile range of thin film thicknesses, from atomic layers to several microns, making it suitable for a wide array of applications. Understanding the specific requirements of your application—whether decorative or functional—will help in selecting the right PVD equipment and achieving the desired film thickness.
Summary Table:
Aspect | Details |
---|---|
Thickness Range | Atomic layers (<10 Å) to several microns (µm) |
Decorative Coatings | ~0.2 µm, used in jewelry, watches, and consumer electronics |
Functional Coatings | 1 µm to 5 µm+, for wear resistance, electronics, and medical devices |
Key Applications | Semiconductors (ultra-thin), wear-resistant coatings (thicker) |
Factors Affecting Thickness | Deposition time, material properties, substrate, and process parameters |
Comparison with CVD | PVD offers lower temperatures and better substrate compatibility |
Ready to optimize your thin film applications? Contact us today to find the perfect PVD solution!