A good crucible is defined by its ability to withstand extreme temperatures, maintain chemical and physical stability, and resist reactions with the materials it contains. It must have a higher melting point than the substances it holds and be chemically compatible with them to avoid contamination. For applications like refining and melting precious metals, non-wetting properties are crucial to prevent metal penetration, achieved through dense material structures and durable protective glazes. Additionally, the crucible's design must align with operational requirements, such as furnace type, melting temperatures, and specific processes like degassing or slag removal. Modern crucibles are often graphite-based composites, tailored to meet the demands of various furnace types and melting applications.
Key Points Explained:
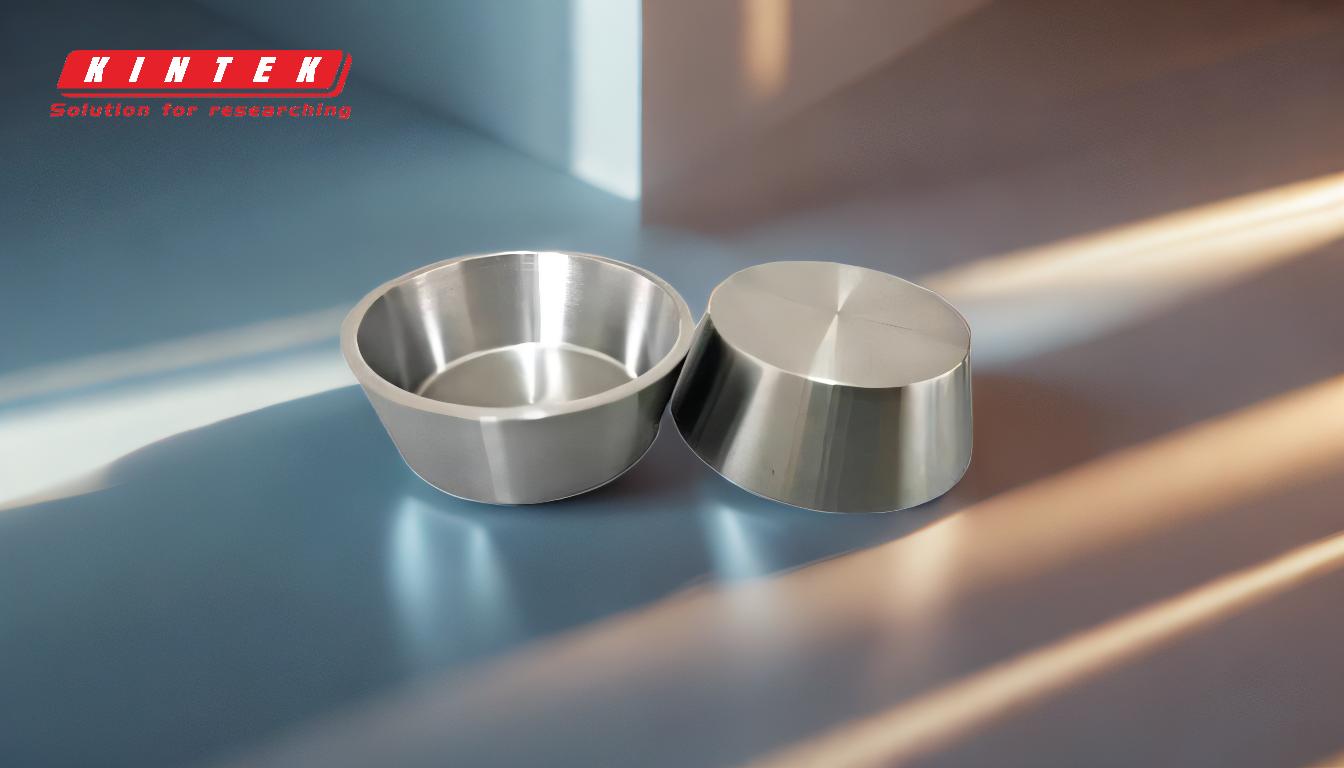
-
High-Temperature Resistance:
- A crucible must withstand extreme temperatures without degrading. This ensures it can handle the melting or refining processes without breaking down.
- The melting point of the crucible must be higher than the materials it contains to prevent structural failure during operation.
-
Chemical and Physical Stability:
- The crucible must remain chemically inert to the materials it holds to avoid contamination. This is particularly important in applications involving precious metals or reactive alloys.
- Physical stability ensures the crucible maintains its shape and integrity under thermal stress, preventing cracks or deformations.
-
Non-Wetting Properties (for Precious Metals):
- Non-wetting properties prevent molten metals from penetrating the crucible's surface, ensuring clean metal output.
- This is achieved through dense material structures and durable protective glazes, which create a barrier against metal penetration.
-
Material Composition and Design:
- Modern crucibles are often graphite-based composites, with performance depending on the control of graphite’s structural alignment.
- The crucible's size, shape, and design (e.g., with or without pouring spouts) must align with the furnace type and operational requirements.
-
Operational Compatibility:
- Crucibles must match the specific furnace type (e.g., fuel-fired, electric resistance, induction) and melting application.
- For induction furnaces, the crucible's electrical resistivity must align with the furnace's operating frequency to prevent overheating.
-
Consideration of Melting Processes:
- Factors like melting and holding temperatures, temperature change rates, charging methods, and processes (e.g., degassing, slag removal) must be considered.
- The crucible should also accommodate specific operational needs, such as avoiding alloy cross-contamination.
-
Versatility and Adaptability:
- Crucibles vary in size, from small teacup-sized containers to large ones capable of holding several tons of metal.
- They can be fixed in place or designed for removal, depending on the application and furnace setup.
By addressing these key points, a crucible can effectively meet the demands of various industrial and laboratory applications, ensuring efficiency, durability, and high-quality results.
Summary Table:
Feature | Description |
---|---|
High-Temperature Resistance | Withstands extreme temperatures without degrading; melting point higher than contents. |
Chemical Stability | Remains chemically inert to prevent contamination, especially with precious metals. |
Physical Stability | Maintains shape and integrity under thermal stress, preventing cracks or deformations. |
Non-Wetting Properties | Prevents metal penetration through dense structures and protective glazes. |
Material Composition | Often graphite-based composites, optimized for performance and durability. |
Operational Compatibility | Matches furnace type (e.g., induction, fuel-fired) and specific melting processes. |
Versatility | Available in various sizes and designs to suit different applications. |
Need a crucible tailored to your specific needs? Contact our experts today for personalized solutions!