Thermal evaporation is a versatile deposition technique used to create thin films of various materials. It is widely employed in industries such as electronics, optics, and solar energy. The process involves heating a material in a vacuum until it evaporates, allowing it to condense on a substrate to form a thin film. Materials suitable for thermal evaporation include metals, alloys, semiconductors, oxides, nitrides, and organic compounds. Commonly used materials include aluminum, silver, gold, titanium, chromium, nickel, magnesium, silicon dioxide, tungsten, and copper. These materials are chosen based on their properties and the specific application requirements, such as conductivity, reflectivity, or durability.
Key Points Explained:
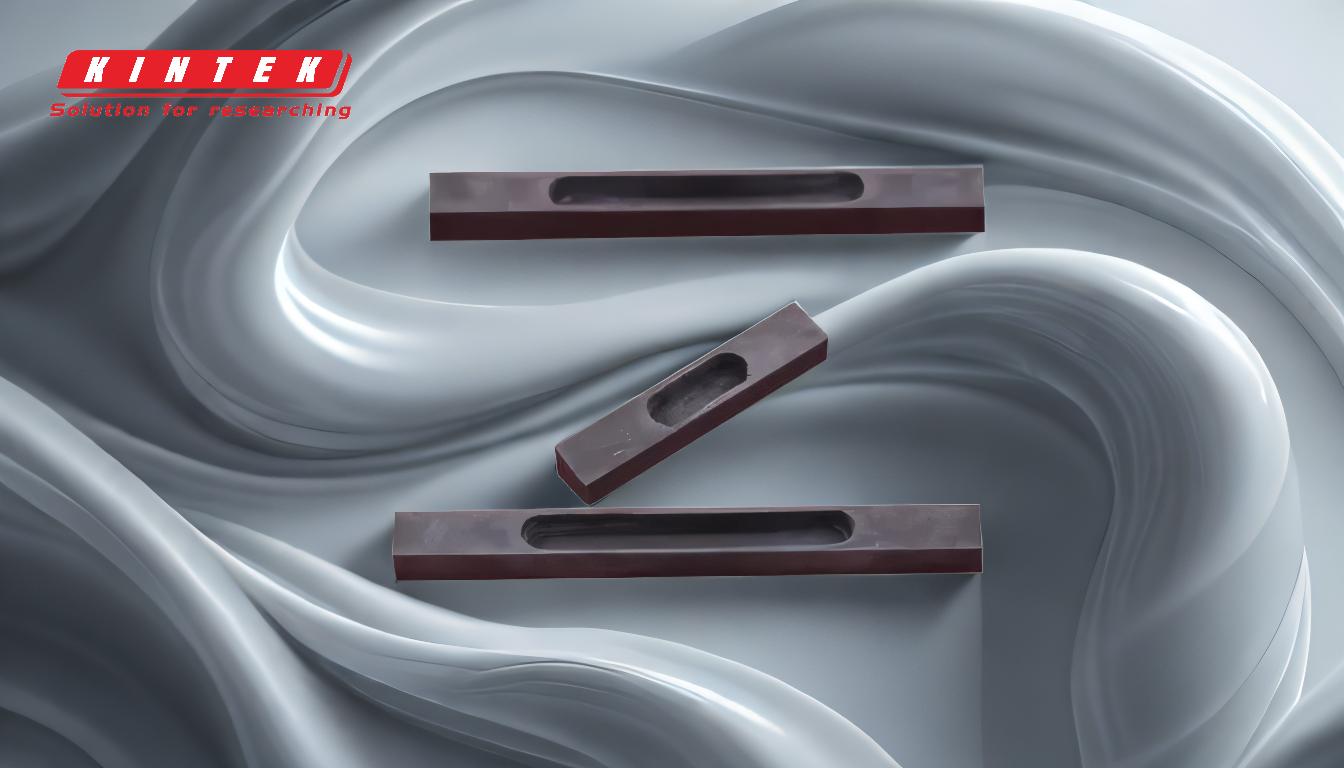
-
Types of Materials Used in Thermal Evaporation:
-
Metals:
- Commonly used metals include aluminum, silver, gold, titanium, chromium, nickel, magnesium, tungsten, and copper.
- These metals are often chosen for their electrical conductivity, reflectivity, and durability. For example, aluminum and silver are frequently used in solar cells and OLED displays due to their excellent conductivity and reflectivity.
-
Alloys:
- Alloys can also be deposited using thermal evaporation. These materials are often used to achieve specific mechanical, electrical, or optical properties that pure metals cannot provide.
-
Semiconductors:
- Semiconductors like silicon can be deposited using thermal evaporation, although this is less common compared to other deposition methods like chemical vapor deposition (CVD).
-
Oxides and Nitrides:
- Materials such as silicon dioxide (SiO₂) and various nitrides can be deposited using thermal evaporation. These materials are often used for their insulating or protective properties.
-
Organic Compounds:
- Some organic materials can also be deposited using thermal evaporation, particularly in the fabrication of organic light-emitting diodes (OLEDs) and other organic electronic devices.
-
Metals:
-
Common Applications of Materials in Thermal Evaporation:
-
Solar Cells:
- Metals like aluminum and silver are commonly used to create conductive layers in solar cells. These materials help in efficient electron transport and light reflection.
-
OLED Displays:
- Silver and aluminum are often used in OLED displays for their high reflectivity and conductivity, which are crucial for the performance of the display.
-
Thin-Film Transistors:
- Materials like chromium and gold are used in the fabrication of thin-film transistors due to their excellent electrical properties and stability.
-
Optical Coatings:
- Metals such as gold and silver, as well as oxides like silicon dioxide, are used in optical coatings to enhance reflectivity, reduce glare, or provide protective layers.
-
Solar Cells:
-
Selection Criteria for Materials:
-
Evaporation Temperature:
- The material must have a suitable evaporation temperature that can be achieved in a vacuum environment. Materials with very high melting points may require specialized equipment.
-
Purity:
- High-purity materials are often required to ensure the quality and performance of the deposited film. Impurities can affect the electrical, optical, and mechanical properties of the film.
-
Compatibility with Substrate:
- The material must be compatible with the substrate to ensure good adhesion and film quality. For example, some materials may react with the substrate or cause delamination.
-
Desired Film Properties:
- The choice of material is often dictated by the desired properties of the film, such as conductivity, reflectivity, transparency, or mechanical strength.
-
Evaporation Temperature:
-
Advantages of Thermal Evaporation:
-
Versatility:
- Thermal evaporation can deposit a wide range of materials, making it suitable for various applications.
-
High Purity:
- The process can produce high-purity films, which is essential for many electronic and optical applications.
-
Controlled Deposition:
- The deposition rate and film thickness can be precisely controlled, allowing for the creation of very thin and uniform films.
-
Versatility:
-
Limitations of Thermal Evaporation:
-
Material Limitations:
- Not all materials are suitable for thermal evaporation, particularly those with very high melting points or those that decompose before evaporating.
-
Uniformity:
- Achieving uniform film thickness over large areas can be challenging, especially for complex geometries.
-
Cost:
- The process can be expensive due to the need for high vacuum conditions and specialized equipment.
-
Material Limitations:
In summary, thermal evaporation is a highly versatile and widely used technique for depositing thin films of various materials, including metals, alloys, semiconductors, oxides, nitrides, and organic compounds. The choice of material depends on the specific application requirements, such as conductivity, reflectivity, or durability. While the process offers many advantages, including high purity and controlled deposition, it also has some limitations, such as material suitability and cost. Understanding these factors is crucial for selecting the appropriate materials and optimizing the deposition process for specific applications.
Summary Table:
Category | Examples | Key Properties | Applications |
---|---|---|---|
Metals | Aluminum, Silver, Gold, Titanium, Chromium, Nickel, Magnesium, Tungsten, Copper | Conductivity, Reflectivity, Durability | Solar Cells, OLED Displays, Thin-Film Transistors, Optical Coatings |
Alloys | Custom alloys for specific mechanical, electrical, or optical properties | Tailored properties for specific applications | Specialized coatings, electronic devices |
Semiconductors | Silicon | Electrical properties, compatibility with electronic applications | Thin-film transistors, electronic components |
Oxides & Nitrides | Silicon Dioxide (SiO₂), Nitrides | Insulating or protective properties | Optical coatings, protective layers |
Organic Compounds | Organic materials for OLEDs | Light-emitting properties, flexibility | Organic light-emitting diodes (OLEDs), organic electronic devices |
Need help selecting the right materials for thermal evaporation? Contact our experts today to optimize your thin-film deposition process!