PVD (Physical Vapor Deposition) coating is a versatile and widely used process that involves depositing thin layers of materials onto substrates to enhance their properties. The materials used for PVD coating vary depending on the application, but they generally include metals, alloys, ceramics, and specialized compounds. Common metals used in PVD coating include titanium, chromium, zirconium, and aluminum, often in the form of nitrides, carbides, or oxides. These materials are chosen for their ability to improve hardness, wear resistance, corrosion resistance, and aesthetic appeal. PVD coatings are applied to a variety of substrates, including steels, non-ferrous metals, glass, and plastics, making them suitable for industries ranging from automotive and aerospace to medical and consumer goods.
Key Points Explained:
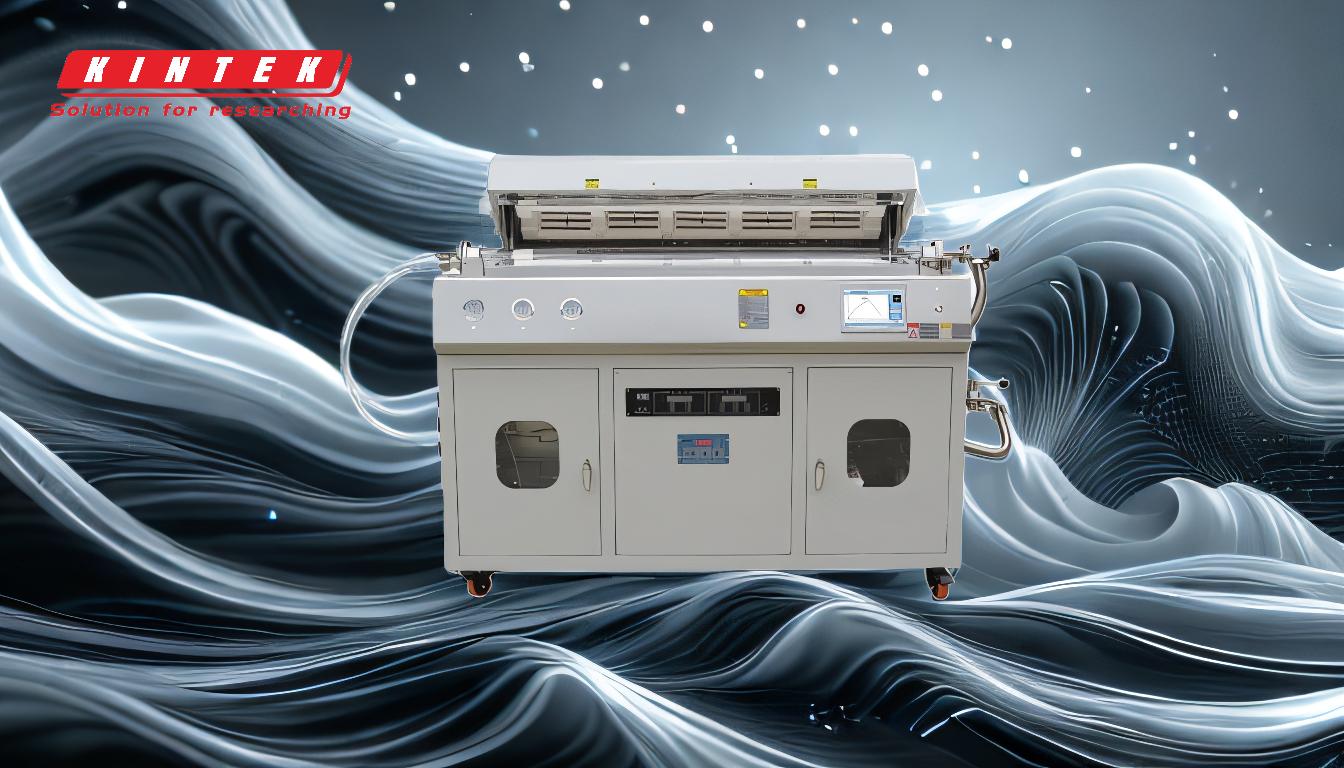
-
Common Metals Used in PVD Coating:
- Titanium (Ti): Often used in the form of titanium nitride (TiN) or titanium aluminum nitride (TiAlN), titanium-based coatings are popular for their hardness and wear resistance. They are commonly applied to cutting tools, automotive components, and medical instruments.
- Chromium (Cr): Chromium-based coatings, such as chromium nitride (CrN), are known for their corrosion resistance and are used in applications like marine hardware and surgical tools.
- Zirconium (Zr): Zirconium nitride (ZrN) is used for its gold-like appearance and durability, making it suitable for decorative applications and high-performance components.
- Aluminum (Al): Aluminum-based coatings, such as aluminum oxide (Al2O3), are used for their thermal and electrical insulation properties, often in aerospace and automotive applications.
-
Specialized Compounds and Alloys:
- Carbides and Nitrides: Materials like titanium carbide (TiC) and titanium nitride (TiN) are used for their extreme hardness and wear resistance, making them ideal for cutting tools and industrial machinery.
- Diamond-Like Coatings (DLCs): These coatings provide a combination of hardness, low friction, and chemical inertness, making them suitable for high-performance applications in the automotive and aerospace industries.
- MCrAlYs: These are alloys of nickel, cobalt, or iron with chromium, aluminum, and yttrium, used for their high-temperature oxidation resistance in turbine blades and other high-stress components.
-
Substrates Suitable for PVD Coating:
- Steels: High-alloy steels, such as high-speed steels and stainless steels, are commonly coated to enhance their durability and performance.
- Non-Ferrous Metals: Copper, aluminum, and their alloys are also suitable for PVD coating, often used in electrical and thermal applications.
- Plastics and Glass: ABS plastics and glass can be coated for decorative or functional purposes, such as in consumer electronics or automotive interiors.
-
Applications of PVD Coating:
- Automotive: PVD coatings are used on car parts like wheels, pistons, and engine components to improve wear resistance and reduce friction.
- Medical: Surgical tools and medical equipment benefit from PVD coatings due to their biocompatibility and resistance to sterilization processes.
- Consumer Goods: Kitchen and bath fixtures, jewelry, and eyeglass frames are often coated for both aesthetic appeal and durability.
- Aerospace: High-performance components in aircraft and spacecraft are coated with materials like titanium and zirconium to withstand extreme conditions.
-
Advantages of PVD Coating:
- Durability: PVD coatings can significantly extend the lifespan of products, sometimes by up to ten times, making them last more than 25 years in some cases.
- Environmental Benefits: Unlike traditional chrome plating, PVD coating does not produce toxic substances, making it a greener alternative.
- Versatility: The wide range of materials and substrates that can be coated makes PVD suitable for a variety of industries and applications.
-
Future Trends in PVD Coating:
- Antimicrobial Applications: Research is being conducted on in-chamber antimicrobial PVD coatings, which could be used in the food industry and healthcare to improve sanitation and reduce the spread of germs.
- Advanced Materials: The development of new materials and compounds for PVD coating is ongoing, with a focus on enhancing performance in extreme environments and specialized applications.
In summary, PVD coating is a highly adaptable and effective process that uses a variety of metals, alloys, and compounds to enhance the properties of substrates across numerous industries. Its ability to improve durability, provide environmental benefits, and offer versatile applications makes it a valuable technology for both current and future innovations.
Summary Table:
Metal | Common Forms | Key Properties | Applications |
---|---|---|---|
Titanium (Ti) | TiN, TiAlN | Hardness, Wear Resistance | Cutting Tools, Automotive, Medical |
Chromium (Cr) | CrN | Corrosion Resistance | Marine Hardware, Surgical Tools |
Zirconium (Zr) | ZrN | Durability, Aesthetic Appeal | Decorative, High-Performance Components |
Aluminum (Al) | Al2O3 | Thermal & Electrical Insulation | Aerospace, Automotive |
Want to enhance your products with PVD coatings? Contact us today to learn more!