Sintering is a versatile manufacturing process that allows for the creation of high-quality, durable products from a wide range of metals. This process involves compacting metal powders and heating them to a temperature below their melting point, which causes the particles to bond together. The metals that can be sintered include iron, iron-copper, copper steels, nickel steels, stainless steels (300 and 400 series), high-strength low-alloy steels (HSLA), medium- and high-carbon steels, diffusion hardenable steels, brass, bronze, soft iron magnetic alloys, and aluminum. These metals are chosen based on the desired properties of the final product, such as strength, durability, and corrosion resistance. Additionally, powders can be mixed to create unique and reliable alloys, allowing for customization to meet specific client needs.
Key Points Explained:
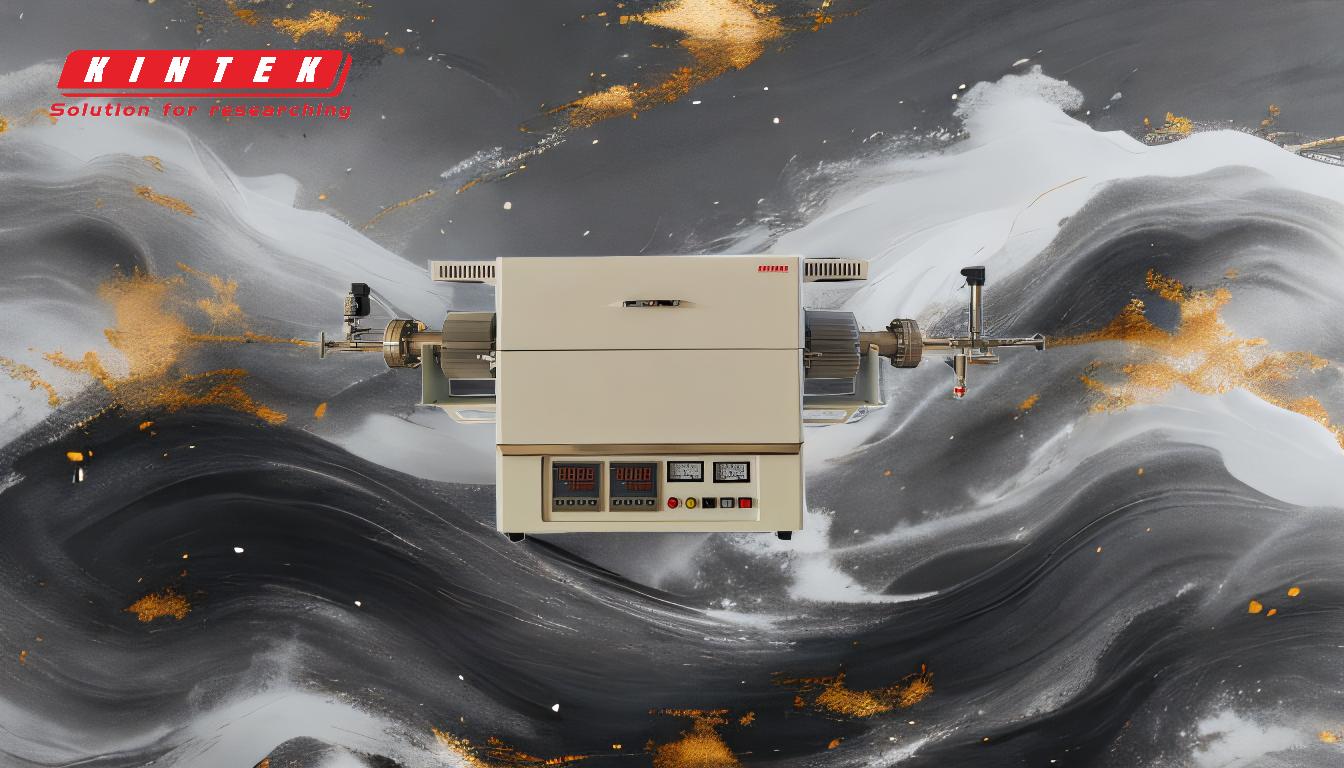
-
Sintering Process Overview:
- Sintering involves compacting metal powders and heating them to a temperature below their melting point.
- This process causes the particles to bond together, creating a solid, durable product.
- Sintering allows for greater control over the manufacturing process, resulting in more consistent products.
-
Common Metals Used in Sintering:
- Iron and Iron Alloys: Iron is one of the most commonly sintered metals due to its availability and versatility. Iron-copper alloys are also widely used.
- Copper Steels and Nickel Steels: These alloys are used for their strength and durability.
- Stainless Steels (300 and 400 series): Known for their corrosion resistance, these steels are ideal for applications requiring longevity and resistance to harsh environments.
- High-Strength Low-Alloy Steels (HSLA): These steels offer a good balance of strength and weight, making them suitable for structural applications.
- Medium- and High-Carbon Steels: These steels are used for their hardness and wear resistance.
- Diffusion Hardenable Steels: These steels can be heat-treated to improve their surface hardness while maintaining a tough core.
- Brass and Bronze: These copper alloys are used for their machinability, corrosion resistance, and aesthetic appeal.
- Soft Iron Magnetic Alloys: These alloys are used in applications requiring magnetic properties.
- Aluminum: Lightweight and corrosion-resistant, aluminum is used in applications where weight reduction is critical.
-
Customization Through Powder Mixing:
- Metal powders can be mixed to create unique alloys tailored to specific client requirements.
- This customization allows for the creation of products with precise mechanical and physical properties.
- The ability to mix powders also enables the production of complex shapes and intricate designs that would be difficult to achieve with traditional manufacturing methods.
-
Advantages of Sintering:
- Material Efficiency: Sintering minimizes material waste, as the process uses only the necessary amount of metal powder.
- Cost-Effectiveness: The process is generally more cost-effective than traditional manufacturing methods, especially for complex parts.
- Consistency and Precision: Sintering allows for the production of parts with consistent properties and precise dimensions.
- Versatility: The wide range of metals that can be sintered makes this process suitable for a variety of industries, including automotive, aerospace, electronics, and medical devices.
-
Applications of Sintered Metals:
- Automotive Industry: Sintered metals are used in the production of gears, bearings, and other components that require high strength and durability.
- Aerospace Industry: Lightweight and strong sintered metals are ideal for aerospace applications, where weight reduction is critical.
- Electronics: Sintered metals are used in the production of connectors, sensors, and other electronic components.
- Medical Devices: The biocompatibility and precision of sintered metals make them suitable for use in medical implants and surgical instruments.
In conclusion, sintering is a highly adaptable manufacturing process that can be used with a wide range of metals to produce high-quality, durable products. The ability to mix powders and create custom alloys further enhances the versatility and applicability of this process across various industries.
Summary Table:
Metal Type | Key Properties | Common Applications |
---|---|---|
Iron and Iron Alloys | Versatile, widely available | Automotive gears, bearings |
Copper Steels, Nickel Steels | High strength, durability | Structural components, industrial machinery |
Stainless Steels (300/400) | Corrosion resistance, longevity | Medical devices, harsh environment applications |
HSLA Steels | Strength-to-weight ratio | Aerospace, automotive frames |
Medium- and High-Carbon Steels | Hardness, wear resistance | Cutting tools, heavy-duty machinery |
Diffusion Hardenable Steels | Surface hardness, tough core | Gears, shafts |
Brass, Bronze | Machinability, corrosion resistance, aesthetic appeal | Decorative fittings, electronic connectors |
Soft Iron Magnetic Alloys | Magnetic properties | Electrical components, sensors |
Aluminum | Lightweight, corrosion-resistant | Aerospace, lightweight structural parts |
Unlock the potential of sintering for your next project—contact us today to get started!