Chemical vapor deposition (CVD) is a versatile and widely used technique for synthesizing a variety of nanomaterials. It involves the deposition of solid materials from a gas-phase chemical reaction, which can be activated by heat or plasma. CVD is particularly valued for its ability to produce high-quality, pure, and durable materials, making it suitable for applications ranging from electronics to protective coatings. The process can be categorized into different types based on the activation source and the method of precursor delivery, such as thermally activated CVD, plasma-enhanced CVD, aerosol-assisted CVD, and direct liquid injection CVD. These variations allow for the synthesis of a wide range of nanomaterials, including graphene, carbon nanotubes, and various metal oxides and nitrides.
Key Points Explained:
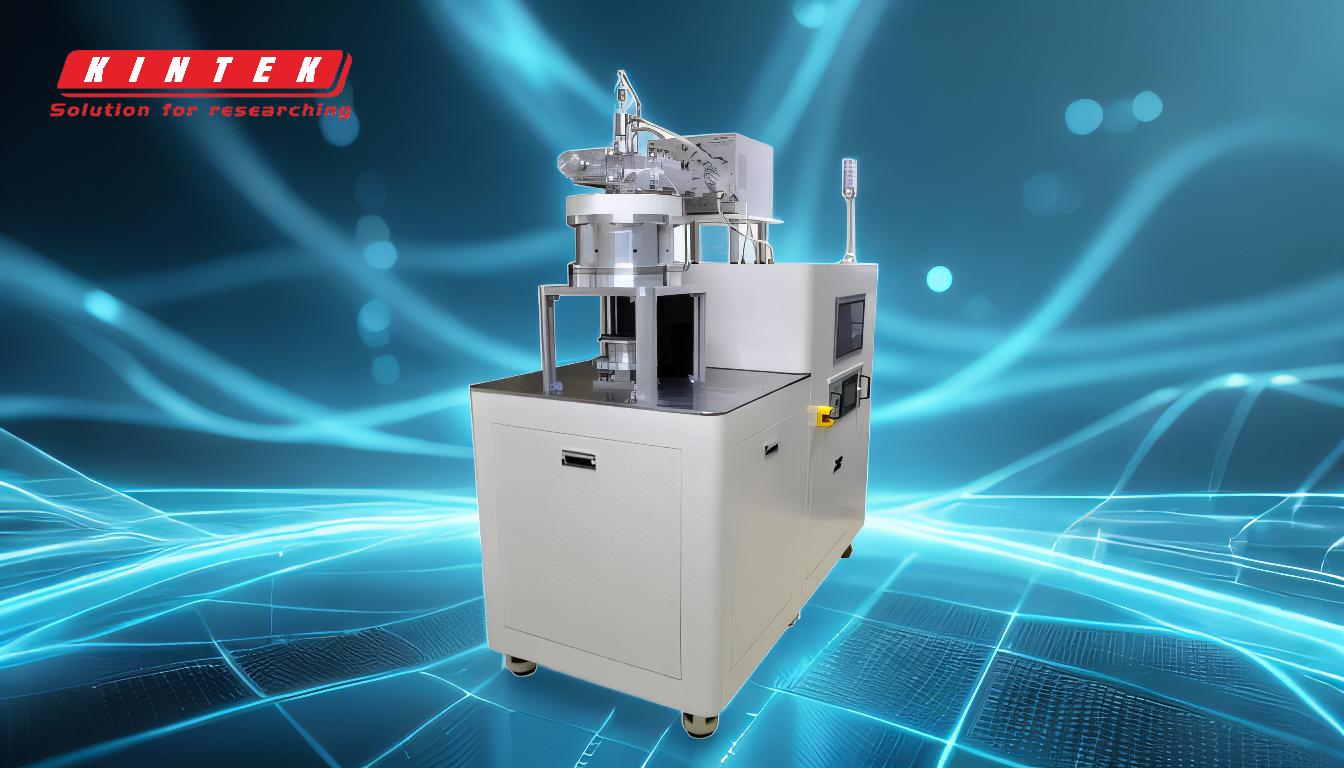
-
Types of Chemical Vapor Deposition:
- Thermally Activated CVD: This method uses heat to initiate the chemical reactions necessary for material deposition. It is commonly used for the synthesis of high-purity materials and is suitable for applications requiring high-temperature stability.
- Plasma-Enhanced CVD (PECVD): In PECVD, plasma is used to activate the chemical reactions, allowing for lower deposition temperatures. This is particularly useful for depositing materials on temperature-sensitive substrates.
- Aerosol-Assisted CVD (AACVD): This method uses aerosols to deliver the precursor materials. It is advantageous for depositing materials with complex compositions and for coating large or irregularly shaped surfaces.
- Direct Liquid Injection CVD (DLI-CVD): In DLI-CVD, a liquid precursor is injected into a heated chamber, where it vaporizes and reacts to form the desired material. This method is useful for depositing materials with high vapor pressure or for precise control over the deposition process.
-
Advantages of CVD:
- Versatility: CVD can be used to deposit a wide range of materials, including ceramics, metals, and glass. This makes it suitable for a variety of applications, from electronics to protective coatings.
- High-Quality Materials: CVD produces materials with high purity, hardness, and resistance to damage. This is particularly important for applications in harsh environments or where material performance is critical.
- Durable Coatings: The coatings produced by CVD are durable and can withstand high-stress environments, making them ideal for protective applications.
- Precision and Complexity: CVD can be used to coat precision and complex surfaces, making it suitable for applications in microelectronics and nanotechnology.
- Temperature Resistance: CVD coatings can maintain their properties even when exposed to extreme temperatures or temperature variations, which is important for applications in aerospace and automotive industries.
-
Types of CVD Reactors:
- Hot Wall Reactors: These reactors are heated uniformly, which can lead to more uniform deposition but may also result in higher energy consumption and potential contamination from the reactor walls.
- Cold Wall Reactors: In these reactors, only the substrate is heated, which can reduce energy consumption and contamination. However, it may also lead to less uniform deposition.
-
Nanomaterials Synthesized by CVD:
- Graphene: CVD is one of the most common methods for synthesizing graphene, a single layer of carbon atoms arranged in a hexagonal lattice. Graphene produced by CVD is known for its high electrical conductivity, mechanical strength, and thermal conductivity.
- Carbon Nanotubes (CNTs): CVD is also widely used for the synthesis of carbon nanotubes, which have applications in electronics, materials science, and nanotechnology.
- Metal Oxides and Nitrides: CVD can be used to synthesize various metal oxides and nitrides, such as titanium dioxide (TiO2), zinc oxide (ZnO), and aluminum nitride (AlN). These materials have applications in catalysis, electronics, and protective coatings.
- Other Nanomaterials: CVD can also be used to synthesize other nanomaterials, such as silicon carbide (SiC), boron nitride (BN), and various thin films used in semiconductor devices.
In summary, chemical vapor deposition is a highly versatile and effective method for synthesizing a wide range of nanomaterials. Its ability to produce high-quality, durable, and pure materials makes it suitable for a variety of applications, from electronics to protective coatings. The different types of CVD, including thermally activated, plasma-enhanced, aerosol-assisted, and direct liquid injection, offer flexibility in terms of the materials that can be synthesized and the conditions under which they can be deposited. This makes CVD an indispensable tool in the field of nanotechnology and materials science.
Summary Table:
Nanomaterial | Applications |
---|---|
Graphene | Electronics, sensors, energy storage |
Carbon Nanotubes (CNTs) | Electronics, materials science, nanotechnology |
Metal Oxides (e.g., TiO2, ZnO) | Catalysis, electronics, protective coatings |
Metal Nitrides (e.g., AlN) | Electronics, protective coatings |
Silicon Carbide (SiC) | Semiconductor devices, high-temperature applications |
Boron Nitride (BN) | Thermal management, lubricants, protective coatings |
Learn how CVD can revolutionize your material synthesis—contact our experts today!