Pyrolysis is a thermal decomposition process that breaks down plastic waste into smaller molecules, producing oil, gas, and char. However, not all plastics are suitable for pyrolysis due to the potential release of toxic gases or inefficiency in the process. Plastics like HDPE, LDPE, PP, and PS are commonly used in pyrolysis, while PVC and PET are unsuitable because they release harmful substances when heated. Additionally, post-consumer plastics, municipal solid waste, and mixed plastics can also be processed, provided they are free from contaminants like PVC or PET. Understanding the types of plastics suitable for pyrolysis is crucial for efficient and safe recycling.
Key Points Explained:
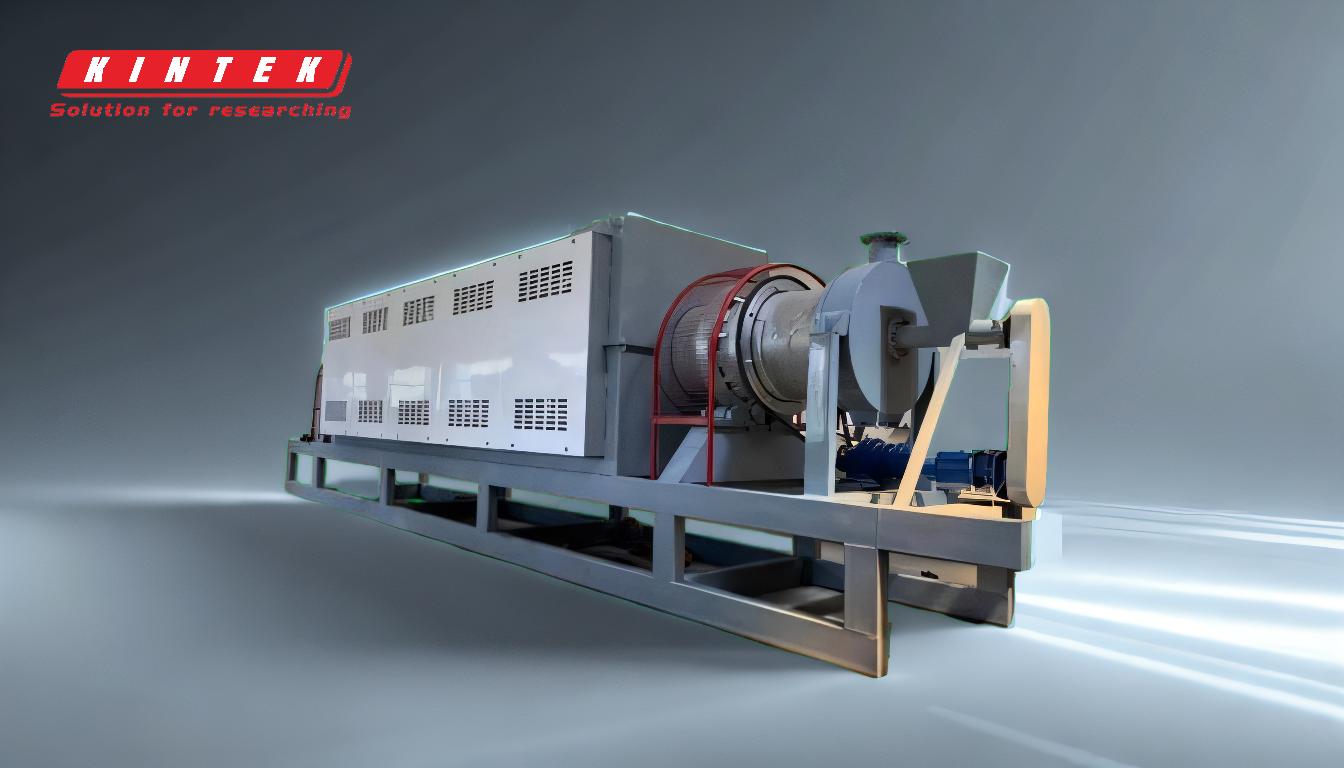
-
Plastics Suitable for Pyrolysis:
- HDPE (High-Density Polyethylene): Commonly found in woven bags, packaging bags, and freezer food bags. It is widely used in pyrolysis due to its high yield of oil and gas.
- LDPE (Low-Density Polyethylene): Used in items like disposable cups and cotton swabs. It is also suitable for pyrolysis, producing valuable outputs.
- PP (Polypropylene): Found in packaging materials and disposable containers. It is another plastic that performs well in pyrolysis.
- PS (Polystyrene): Often used in disposable cups and food packaging. It can be processed through pyrolysis, though it may require specific conditions to optimize output.
- PC (Polycarbonate): While less common, it can be processed in pyrolysis systems, though it is not as widely used as HDPE or LDPE.
-
Plastics Unsuitable for Pyrolysis:
- PVC (Polyvinyl Chloride): Releases toxic chlorine gas when pyrolyzed, making it hazardous and unsuitable for the process.
- PET (Polyethylene Terephthalate): Produces harmful byproducts and is not recommended for pyrolysis due to its chemical structure.
-
Types of Plastic Waste for Pyrolysis:
- Post-Consumer Plastics: These are plastics that have been used and discarded by consumers, such as packaging materials and disposable items.
- Municipal Solid Waste Segregated Plastics: Plastics separated from municipal waste streams, which can be processed if free from contaminants.
- Reject of Mechanical Recycling: Plastics that cannot be recycled through traditional mechanical methods but are suitable for pyrolysis.
- Multi-Layer Packaging: Complex packaging materials that combine multiple layers of plastic, which can be challenging to recycle mechanically but are suitable for pyrolysis.
- Mixed PET/PVC Contaminated Plastics: While PET and PVC are generally unsuitable, mixed plastics with low contamination levels can sometimes be processed, though this requires careful handling.
-
Other Materials Suitable for Pyrolysis:
- Rubber: Includes natural and synthetic rubber products, such as tires from cars, trucks, and industrial vehicles.
- Oil Sludge: Various types of oil sludge, including refinery waste and drill cuttings, can be processed through pyrolysis.
- Biomass: Materials like wood waste, agricultural residues, and algae can also be used in pyrolysis, especially when co-fed with plastics.
-
Considerations for Pyrolysis:
- Contamination: Plastics contaminated with PVC or PET should be avoided due to the release of toxic gases.
- Feedstock Composition: The type of plastic and its composition significantly impact the efficiency and output of the pyrolysis process.
- Process Conditions: Temperature, pressure, and residence time must be optimized based on the type of plastic being processed.
By understanding the types of plastics suitable for pyrolysis and the associated considerations, stakeholders can make informed decisions about recycling and waste management, ensuring both efficiency and environmental safety.
Summary Table:
Category | Details |
---|---|
Suitable Plastics | HDPE, LDPE, PP, PS, PC |
Unsuitable Plastics | PVC, PET |
Plastic Waste Types | Post-consumer, municipal solid waste, mixed plastics, multi-layer packaging |
Other Suitable Materials | Rubber, oil sludge, biomass |
Key Considerations | Avoid PVC/PET contamination, optimize feedstock and process conditions |
Need help identifying the right plastics for pyrolysis? Contact our experts today for tailored advice!