Grinding balls used in ball mills come in various sizes, typically ranging from ½ inch to 2 inches in diameter. The size of the grinding balls is selected based on the specific requirements of the grinding process, such as the desired particle size of the final product, the nature of the material being ground, and the operational parameters of the ball mill. Smaller balls, like ½ inch, are used for fine grinding, while larger balls, such as 2 inches, are suitable for coarser grinding. The choice of grinding ball size, along with factors like density, hardness, and composition, significantly impacts the efficiency and outcome of the grinding process.
Key Points Explained:
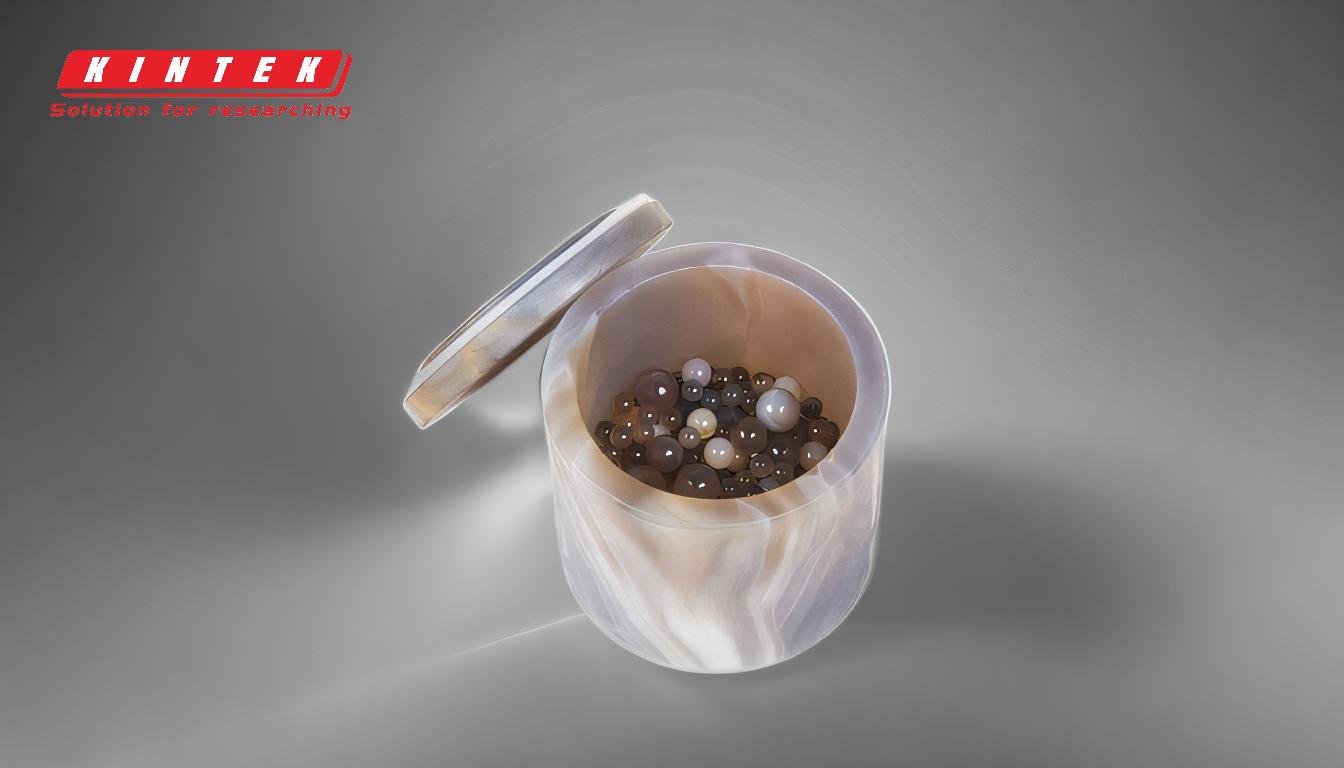
-
Common Sizes of Grinding Balls:
- ½ inch balls: These are the smallest grinding balls used in ball mills. They are ideal for grinding fine-grained materials such as cement and minerals. The small size allows for a higher surface area contact with the material, leading to finer particle sizes.
- ¾ inch balls: Slightly larger than ½ inch balls, these are used for intermediate grinding tasks. They offer a balance between fine and coarse grinding.
- 1-inch balls: These are commonly used for general-purpose grinding. They are versatile and can handle a wide range of materials and particle sizes.
- 2-inch balls: The largest among the common sizes, 2-inch balls are used for coarse grinding. They are effective in breaking down larger particles and are often used in the initial stages of grinding.
-
Factors Influencing Grinding Ball Size Selection:
- Desired Particle Size: Smaller balls are used when the goal is to achieve a finer particle size. They provide more contact points and a larger surface area for grinding.
- Nature of the Material: The hardness and abrasiveness of the material being ground influence the choice of ball size. Harder materials may require larger or harder balls to effectively break down the particles.
- Operational Parameters: The rotation speed of the ball mill, the feed rate, and the residence time of the material in the mill chamber all affect the choice of ball size. For example, longer grinding times with smaller balls can produce finer particles.
-
Impact of Grinding Ball Size on Grinding Efficiency:
- Smaller Balls: These are more effective for fine grinding due to their higher surface area and ability to produce smaller particles. However, they may require longer grinding times.
- Larger Balls: These are better suited for coarse grinding and can handle larger particles more efficiently. They are often used in the initial stages of grinding to reduce particle size before switching to smaller balls for finer grinding.
-
Composition and Properties of Grinding Balls:
- Material Composition: Grinding balls can be made from various materials, including ceramic, flint, and stainless steel. The choice of material depends on the specific requirements of the grinding application, such as the need for non-reactive media or the presence of grinding media in the finished product.
- Density and Hardness: The density and hardness of the grinding balls affect their grinding efficiency and wear resistance. Harder and denser balls are more effective for grinding harder materials but may also cause more wear on the mill lining.
-
Practical Considerations for Equipment Purchasers:
- Cost vs. Performance: Smaller balls may require longer grinding times, which can increase operational costs. Purchasers need to balance the cost of grinding media with the desired grinding efficiency and product quality.
- Compatibility with Mill Design: The size and type of grinding balls must be compatible with the design of the ball mill, including the mill chamber size and rotation speed.
- Maintenance and Replacement: The wear rate of grinding balls varies depending on their size and material. Purchasers should consider the frequency of replacement and the availability of spare parts.
In summary, the size of grinding balls is a critical factor in the efficiency and outcome of the grinding process in ball mills. The selection of the appropriate ball size depends on the specific requirements of the grinding application, including the desired particle size, the nature of the material, and the operational parameters of the mill. Equipment purchasers must consider these factors, along with the cost, compatibility, and maintenance requirements, to make an informed decision.
Summary Table:
Grinding Ball Size | Application | Key Benefits |
---|---|---|
½ inch | Fine grinding | Higher surface area, finer particles |
¾ inch | Intermediate grinding | Balanced fine and coarse grinding |
1 inch | General-purpose grinding | Versatile for various materials |
2 inches | Coarse grinding | Effective for breaking down large particles |
Need help selecting the right grinding balls for your ball mill? Contact our experts today for tailored advice!