Ball milling is a widely used technique in material processing, and the size of the balls used plays a critical role in determining the efficiency and outcome of the process. The size of the balls affects the grinding mechanism, energy consumption, and the final particle size of the material being processed. Typically, ball sizes range from a few millimeters to several centimeters, depending on the specific application and the desired particle size. The selection of ball size is influenced by factors such as the material properties, mill dimensions, and the desired grinding outcome.
Key Points Explained:
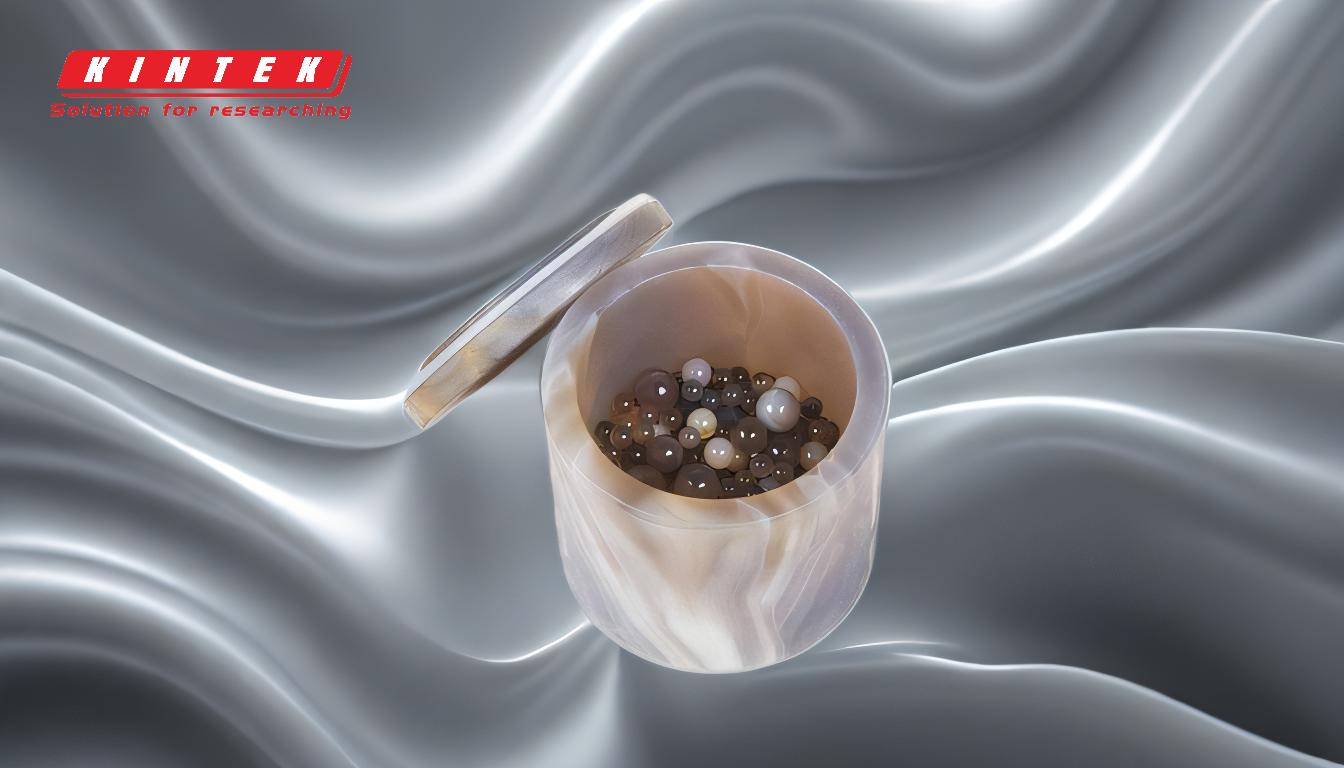
-
General Range of Ball Sizes
- Ball sizes used in ball milling typically range from 5 mm to 30 mm in diameter.
- Smaller balls (e.g., 5–10 mm) are used for fine grinding, while larger balls (e.g., 20–30 mm) are suitable for coarse grinding.
- The choice of ball size depends on the material being processed and the desired particle size distribution.
-
Factors Influencing Ball Size Selection
- Material Hardness: Harder materials require larger balls to achieve effective grinding.
- Mill Dimensions: The size of the mill (e.g., diameter and length) influences the optimal ball size. Larger mills can accommodate larger balls.
- Desired Particle Size: Smaller balls are preferred for achieving finer particle sizes, while larger balls are better for coarse grinding.
- Mill Speed: As mentioned in the reference, the speed of the mill affects the movement of the balls. Larger balls may be more effective at normal speeds, where cascading motion is achieved.
-
Impact of Ball Size on Grinding Efficiency
- Energy Consumption: Smaller balls require more energy to achieve the same grinding effect as larger balls due to their lower mass and impact force.
- Grinding Mechanism: Larger balls provide more impact force, which is effective for breaking down coarse particles, while smaller balls are better for fine grinding due to their increased surface area contact.
- Particle Size Distribution: The size of the balls directly affects the uniformity and fineness of the ground material.
-
Practical Considerations for Ball Size Selection
- Balancing Ball Size and Mill Capacity: Using balls that are too large for a small mill can reduce grinding efficiency and increase wear on the mill lining.
- Cost and Availability: Larger balls may be more expensive and harder to source, so practical considerations often influence the choice.
- Wear and Tear: Smaller balls tend to wear out faster, leading to higher maintenance costs over time.
-
Examples of Ball Size Applications
- Fine Grinding: In industries like pharmaceuticals or ceramics, smaller balls (5–10 mm) are used to achieve micron-sized particles.
- Coarse Grinding: In mining or metallurgy, larger balls (20–30 mm) are used to break down ores or minerals into coarse particles.
- Intermediate Grinding: For general-purpose grinding, medium-sized balls (10–20 mm) are often used.
-
Optimizing Ball Size for Specific Applications
- Experimentation: Trial runs with different ball sizes can help determine the optimal size for a specific material and mill setup.
- Mathematical Models: Some manufacturers use mathematical models to predict the ideal ball size based on material properties and mill parameters.
- Industry Standards: Many industries have established guidelines for ball size selection based on historical data and best practices.
-
Relationship Between Ball Size and Mill Speed
- As highlighted in the reference, mill speed affects the movement of the balls.
- At normal speeds, balls cascade and provide maximum grinding efficiency. The size of the balls should be chosen to ensure proper cascading motion.
- At high speeds, larger balls may be thrown against the mill wall, reducing grinding efficiency.
- At low speeds, smaller balls may not generate enough impact force for effective grinding.
By carefully selecting the appropriate ball size, users can optimize the grinding process, reduce energy consumption, and achieve the desired particle size distribution. The choice of ball size should be tailored to the specific application, considering factors such as material properties, mill dimensions, and operational parameters.
Summary Table:
Aspect | Details |
---|---|
Ball Size Range | 5 mm to 30 mm in diameter |
Fine Grinding | Smaller balls (5–10 mm) for micron-sized particles |
Coarse Grinding | Larger balls (20–30 mm) for breaking down ores or minerals |
Key Factors | Material hardness, mill dimensions, desired particle size, mill speed |
Energy Consumption | Smaller balls require more energy; larger balls are more energy-efficient |
Applications | Pharmaceuticals, ceramics, mining, metallurgy |
Optimization | Trial runs, mathematical models, and industry standards |
Need help selecting the right ball size for your ball milling process? Contact our experts today for personalized advice!