Rotary kilns are industrial equipment used for high-temperature processing of materials, and their size varies depending on the application, design, and operational requirements. Typically, rotary kilns are cylindrical structures made from rolled mild steel plates, with lengths ranging from 30 meters to over 230 meters and diameters from 0.9 meters to 6 meters. The size is influenced by factors such as the aspect ratio (length-to-diameter ratio), material properties, and the specific reactions or processes being carried out. Larger kilns are used for industrial-scale operations, while smaller kilns are suitable for specialized or laboratory applications. The size directly impacts thermal efficiency, throughput, and operational stability.
Key Points Explained:
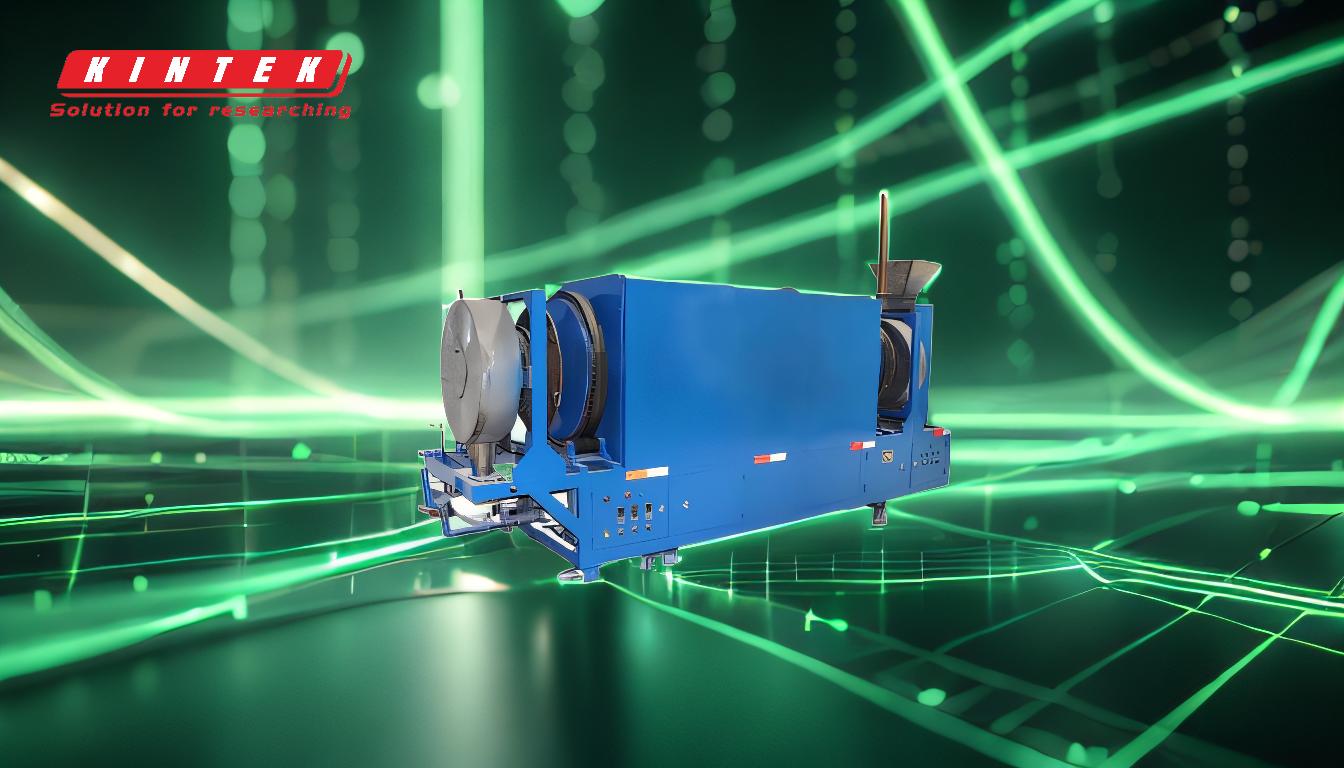
-
Typical Dimensions of Rotary Kilns:
- Length: Rotary kilns can range from 30 meters to over 230 meters in length. For example, a typical rotary furnace might be 30 ft to 60 ft (9.1 m to 18.3 m) long, while industrial-scale kilns can extend up to 230 meters.
- Diameter: The diameter of rotary kilns typically ranges from 0.9 meters to 6 meters. Smaller kilns, such as those used in laboratory settings, may have diameters around 0.9 m to 1.8 m, while larger industrial kilns can reach up to 6 meters in diameter.
-
Aspect Ratio (L/D Ratio):
- The aspect ratio, defined as the length-to-diameter ratio (L/D), is a critical design parameter. It influences the residence time of materials in the kiln, heat distribution, and overall efficiency. Higher aspect ratios are often used for processes requiring longer reaction times or more uniform heat distribution.
-
Material and Construction:
- Rotary kilns are constructed from rolled mild steel plates, typically 15 to 30 mm thick, welded into a cylindrical shape. This construction provides durability and resistance to high temperatures and mechanical stresses.
- The shell's thickness and material quality are essential to prevent deformation, especially in larger kilns where the weight of the structure can cause structural issues.
-
Inclination and Rotation:
- Rotary kilns are often inclined at a slight angle (typically 2-5°) and rotate slowly (1-5 rpm) to facilitate the movement of materials through the kiln. This design ensures even heat distribution and efficient processing.
-
Internal Features:
- Internal fixtures such as constriction dams, lifters, and refractory linings are used to optimize material flow, heat transfer, and residence time. These features are tailored to the specific process requirements and material properties.
- The free board (open space above the material bed) and the shape of the free surface are influenced by operational parameters like feed rate, rotational speed, and material characteristics.
-
Applications and Size Variations:
- Smaller Kilns (0.9 m to 1.8 m diameter): Used for specialized applications such as laboratory testing, small-scale pyrolysis, or pilot projects.
- Larger Kilns (up to 6 m diameter and 230 m length): Employed in industrial processes like cement production, mineral processing, and large-scale pyrolysis. These kilns are designed for high throughput and efficiency.
-
Thermal Efficiency and Output:
- The size of the kiln directly impacts its thermal efficiency and output. Larger kilns with higher L/D ratios generally offer better heat distribution and higher throughput but may require more energy to operate.
- Straight cylinder-type kilns, while simpler and easier to maintain, often have lower thermal efficiency compared to enlarged or customized designs.
-
Customization and Operational Flexibility:
- Rotary kilns can be customized to meet specific process requirements, such as heat patterns, cooling mechanisms, and sealing measures to prevent contamination or gas leakage.
- Features like 360° heater placement and air cooling mechanisms enhance temperature control and operational stability.
In summary, the size of a rotary kiln is determined by its application, material properties, and process requirements. Understanding the relationship between dimensions, aspect ratio, and internal features is crucial for selecting or designing a rotary kiln that meets specific operational needs.
Summary Table:
Parameter | Range |
---|---|
Length | 30m to 230m |
Diameter | 0.9m to 6m |
Aspect Ratio (L/D) | Varies based on process requirements |
Applications | Lab testing, cement production, pyrolysis |
Thermal Efficiency | Higher in larger kilns with higher L/D ratios |
Material | Rolled mild steel plates (15-30mm thick) |
Need help selecting the right rotary kiln for your application? Contact our experts today for tailored solutions!