The temperature of a carbon regeneration kiln typically ranges between 650°C to 800°C. This temperature range is critical for ensuring that the carbon is exposed to a steam-rich, oxygen-deprived atmosphere, which facilitates the regeneration process. The kiln's heat tube rotates and agitates the carbon, ensuring uniform exposure to the high-temperature environment for approximately 20 minutes. This process effectively removes impurities and restores the carbon's adsorption properties.
Key Points Explained:
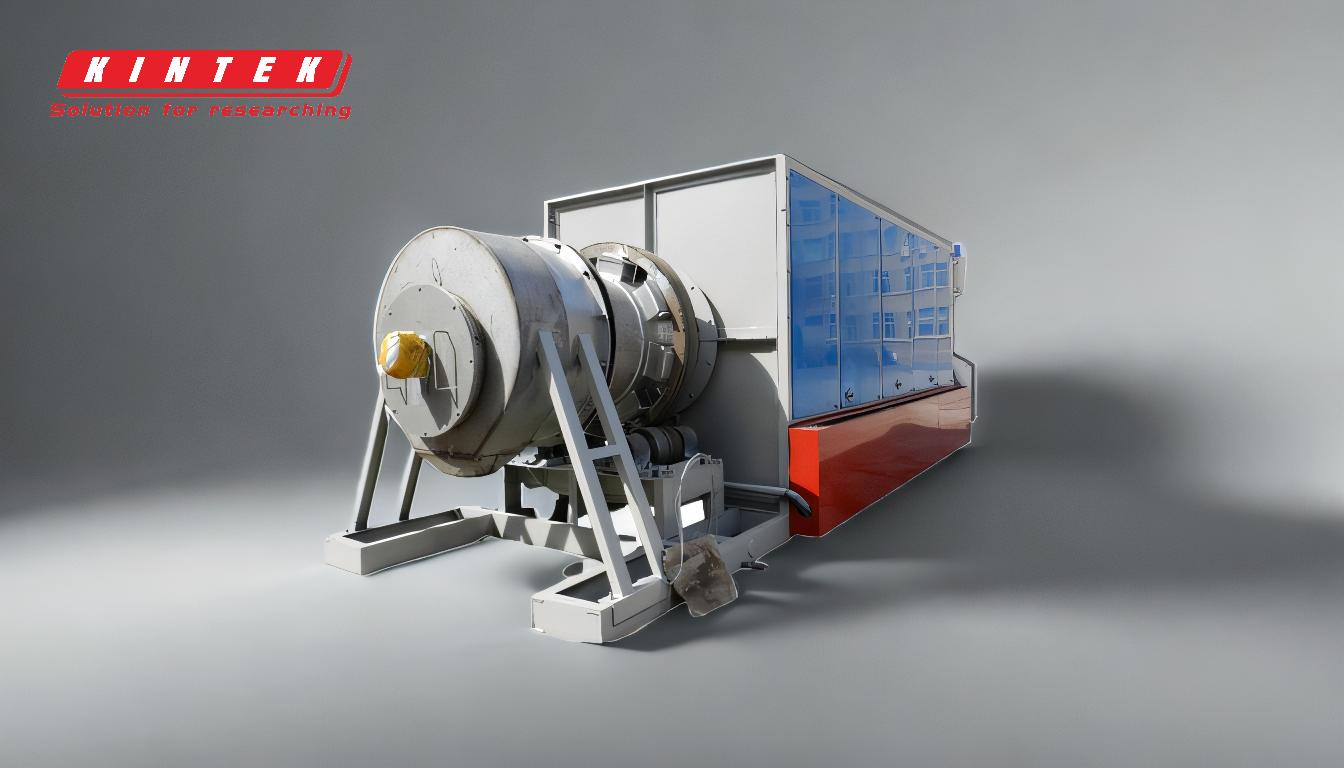
-
Temperature Range of 650°C to 800°C:
- The carbon regeneration process requires high temperatures to effectively remove impurities and regenerate the carbon's adsorption capacity.
- This range ensures that the carbon is heated sufficiently to break down contaminants without causing excessive degradation of the carbon material.
-
Steam-Rich, Oxygen-Deprived Atmosphere:
- The heat tube creates an environment rich in steam but low in oxygen, which is essential for the regeneration process.
- Steam aids in the removal of volatile organic compounds (VOCs) and other contaminants adsorbed on the carbon surface.
-
Rotation and Agitation of the Heat Tube:
- The heat tube rotates and agitates the carbon, ensuring uniform exposure to the high-temperature environment.
- This mechanical action prevents localized overheating and ensures consistent regeneration across all carbon particles.
-
Exposure Time of Approximately 20 Minutes:
- The carbon is exposed to the high-temperature environment for about 20 minutes, which is sufficient to achieve effective regeneration.
- This duration balances the need for thorough regeneration with operational efficiency.
-
Purpose of the Regeneration Process:
- The primary goal is to restore the carbon's adsorption properties by removing adsorbed impurities.
- This process extends the lifespan of the carbon, making it reusable and cost-effective.
-
Importance for Equipment and Consumable Purchasers:
- Understanding the temperature requirements helps purchasers select kilns that can maintain the necessary conditions for effective carbon regeneration.
- It also aids in evaluating the operational efficiency and energy consumption of the kiln, which are critical factors in procurement decisions.
By maintaining the temperature within the specified range, the carbon regeneration kiln ensures optimal performance and longevity of the carbon material, making it a crucial consideration for purchasers and operators alike.
Summary Table:
Key Factor | Details |
---|---|
Temperature Range | 650°C to 800°C for effective impurity removal and carbon regeneration. |
Atmosphere | Steam-rich, oxygen-deprived to aid in VOC and contaminant removal. |
Heat Tube Mechanism | Rotates and agitates carbon for uniform exposure and consistent regeneration. |
Exposure Time | Approximately 20 minutes to balance thorough regeneration and efficiency. |
Purpose | Restores carbon's adsorption properties, extending its lifespan. |
Importance for Purchasers | Helps select kilns with optimal temperature control and energy efficiency. |
Need a carbon regeneration kiln that meets your needs? Contact us today for expert guidance!