When selecting the best type of plastic for pyrolysis, it is crucial to consider both the efficiency of the process and the safety of the byproducts. Not all plastics are suitable for pyrolysis due to the potential release of toxic gases. Polyolefins such as HDPE, LDPE, PP, and PS are generally the most suitable for pyrolysis, with PS yielding the highest liquid oil. PVC and PET, on the other hand, are not recommended due to the production of harmful gases. Additionally, post-consumer plastics and municipal solid waste segregated plastics are also viable options for pyrolysis.
Key Points Explained:
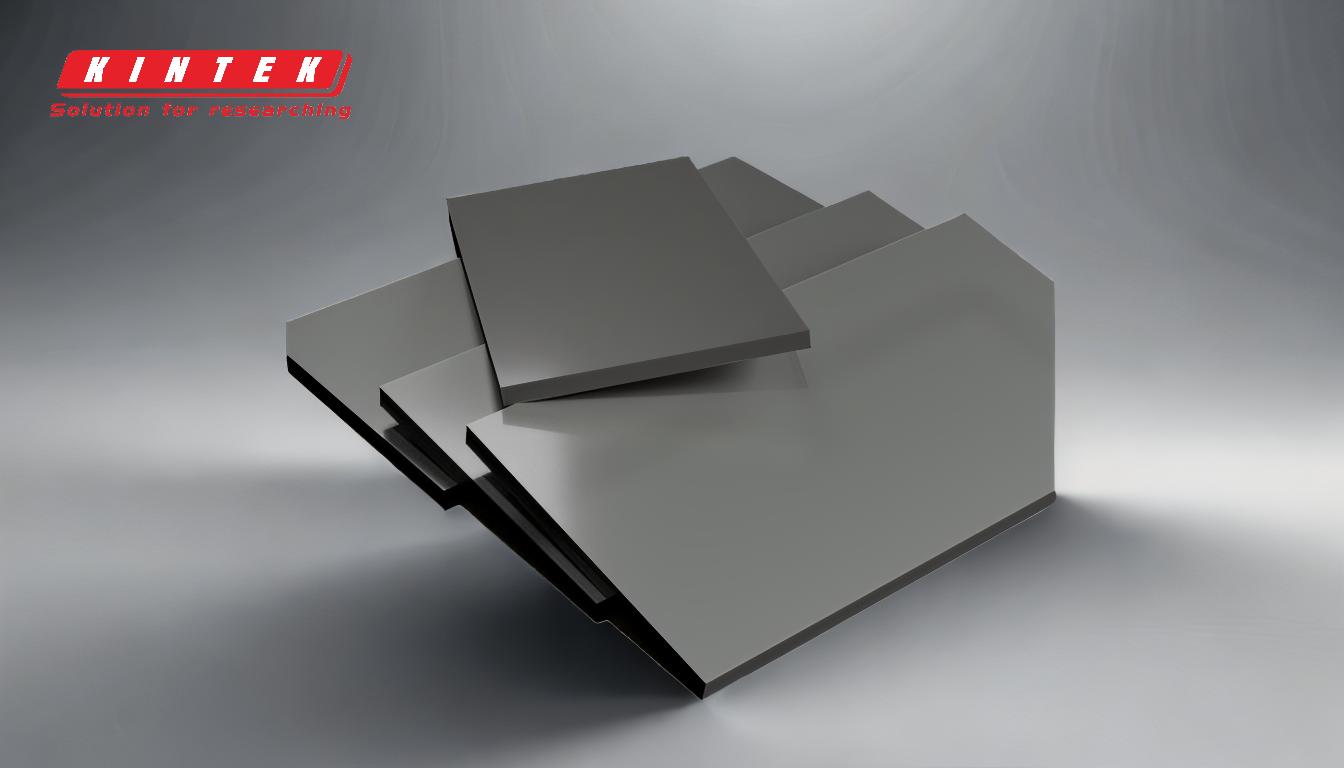
-
Suitability of Plastics for Pyrolysis:
- Polyolefins: Plastics such as HDPE (High-Density Polyethylene), LDPE (Low-Density Polyethylene), PP (Polypropylene), and PS (Polystyrene) are highly suitable for pyrolysis. These materials are known for their high yield of liquid oil and relatively safe byproducts.
- PVC and PET: Polyvinyl Chloride (PVC) and Polyethylene Terephthalate (PET) are not suitable for pyrolysis. When subjected to pyrolysis, these materials produce toxic gases, making them hazardous for this process.
-
Yield of Liquid Oil:
- Polystyrene (PS): Among the suitable plastics, PS produces the highest liquid oil yield, with 70% and 60% using different catalysts (TA-NZ and AA-NZ, respectively). This makes PS a particularly attractive option for pyrolysis.
- Polypropylene (PP) and Polyethylene (PE): While PP and PE also yield significant amounts of liquid oil, their yields are generally lower compared to PS.
-
Types of Plastic Waste Suitable for Pyrolysis:
- Post-Consumer Plastics: These are plastics that have been used and discarded by consumers. They are a major source of plastic waste and are suitable for pyrolysis.
- Municipal Solid Waste Segregated Plastics: Plastics that have been separated from municipal solid waste are also suitable for pyrolysis.
- Reject of Mechanical Recycling: Plastics that are not suitable for mechanical recycling due to contamination or other issues can be processed through pyrolysis.
- Multi-Layer Packaging: Packaging materials that consist of multiple layers of different plastics can be challenging to recycle through traditional methods but are suitable for pyrolysis.
- Mixed PET/PVC Contaminated Plastics: While PET and PVC are generally not suitable for pyrolysis, mixed plastics that contain these materials can still be processed, although with caution due to the potential release of toxic gases.
-
Safety Considerations:
- Toxic Gas Emission: The pyrolysis of PVC and PET can release toxic gases such as hydrogen chloride and benzene, which are harmful to both human health and the environment. Therefore, these materials should be avoided in pyrolysis processes.
- Catalyst Use: The use of catalysts such as TA-NZ and AA-NZ can enhance the efficiency of the pyrolysis process, particularly for PS, by increasing the yield of liquid oil.
-
Environmental and Economic Benefits:
- Waste Reduction: Pyrolysis offers a way to reduce the volume of plastic waste that would otherwise end up in landfills or the environment.
- Resource Recovery: The liquid oil produced through pyrolysis can be used as a fuel or further refined into other valuable products, providing an economic incentive for the process.
In summary, the best types of plastic for pyrolysis are polyolefins such as HDPE, LDPE, PP, and PS, with PS offering the highest liquid oil yield. PVC and PET should be avoided due to the production of toxic gases. Post-consumer plastics, municipal solid waste segregated plastics, and other types of plastic waste are also suitable for pyrolysis, offering both environmental and economic benefits.
Summary Table:
Plastic Type | Suitability for Pyrolysis | Liquid Oil Yield | Key Notes |
---|---|---|---|
HDPE, LDPE, PP | Highly Suitable | Moderate | Safe byproducts, high efficiency |
PS (Polystyrene) | Highly Suitable | Highest (70% with TA-NZ) | Best liquid oil yield |
PVC, PET | Not Suitable | N/A | Releases toxic gases |
Post-Consumer Plastics | Suitable | Varies | Major waste source |
Municipal Solid Waste Plastics | Suitable | Varies | Segregated waste |
Multi-Layer Packaging | Suitable | Varies | Challenging for traditional recycling |
Ready to optimize your pyrolysis process? Contact our experts today for tailored solutions!