Steel quenching is a heat treatment process used to increase the hardness and strength of steel. Not all types of steel can be quenched effectively; the ability to be quenched depends on the steel's composition, particularly its carbon content and alloying elements. Generally, steels with sufficient carbon content (typically above 0.3%) and certain alloying elements can be quenched. The process involves heating the steel to a high temperature, holding it there to allow the structure to change, and then rapidly cooling it in a quenching medium like water, oil, or air. This rapid cooling transforms the steel's microstructure, making it harder and more durable.
Key Points Explained:
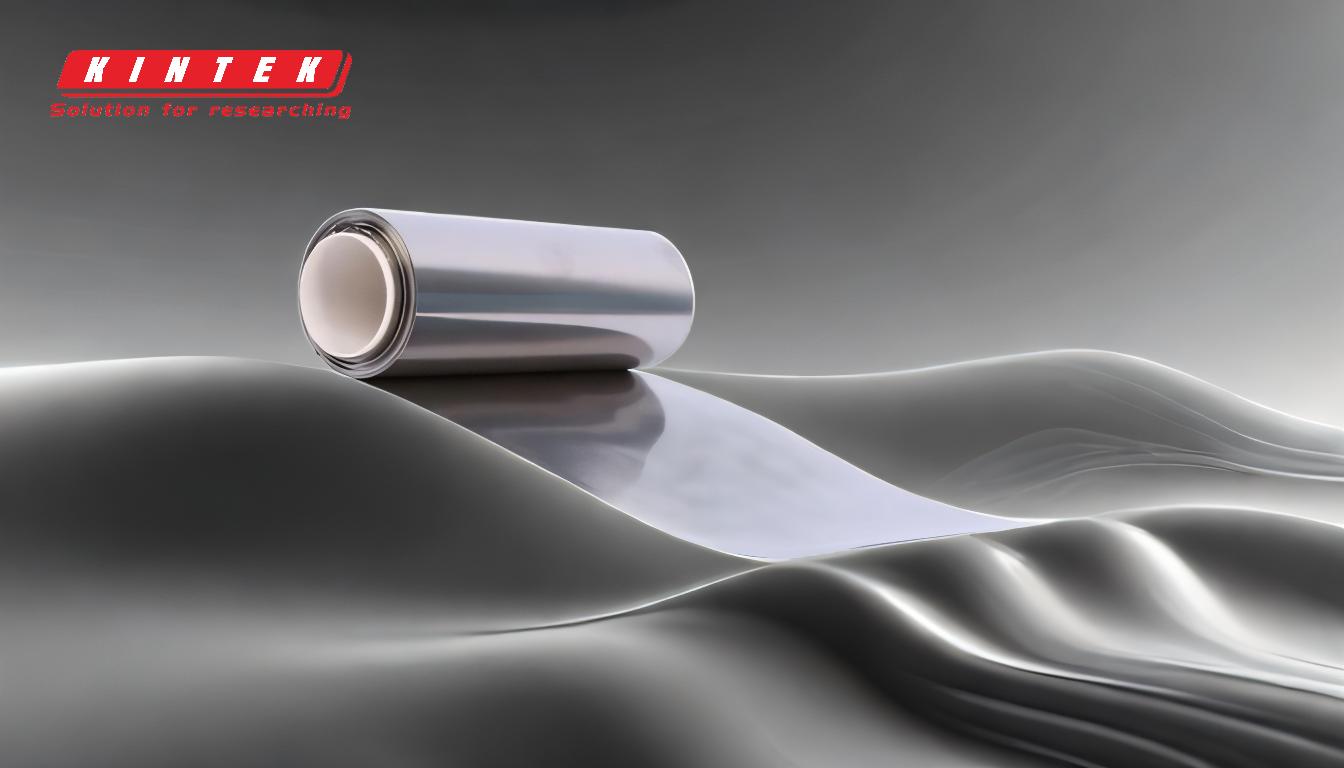
-
Carbon Content and Quenchability:
- The carbon content in steel is a critical factor in determining whether it can be quenched. Steels with a carbon content of 0.3% to 2.0% are typically suitable for quenching.
- Carbon acts as a hardening agent during quenching by forming martensite, a hard and brittle microstructure. Without sufficient carbon, the steel will not harden effectively.
- Examples of quenchable steels include medium-carbon steels (0.3%–0.6% carbon) and high-carbon steels (0.6%–2.0% carbon).
-
Alloying Elements and Their Role:
- Alloying elements such as manganese, chromium, nickel, and molybdenum enhance the steel's ability to be quenched. These elements improve hardenability, which is the depth to which the steel can be hardened during quenching.
- For instance, chromium increases hardenability and corrosion resistance, while molybdenum improves strength and toughness at high temperatures.
- Alloy steels like 4140 steel (chromium-molybdenum steel) and 4340 steel (nickel-chromium-molybdenum steel) are excellent candidates for quenching due to their alloying elements.
-
Types of Quenchable Steels:
- Carbon Steels: Medium and high-carbon steels are commonly quenched for applications requiring high hardness, such as cutting tools and springs.
- Alloy Steels: Steels like 4140, 4340, and tool steels (e.g., D2, A2) are quenched to achieve high strength and wear resistance.
- Tool Steels: These steels, designed for cutting and shaping tools, often contain high carbon and alloying elements like tungsten, vanadium, and cobalt, making them ideal for quenching.
- Stainless Steels: Certain stainless steels, particularly martensitic grades like 410 and 420, can be quenched to achieve high hardness and corrosion resistance.
-
Quenching Process and Its Effects:
- Quenching involves heating the steel to its austenitizing temperature (typically between 800°C and 900°C), holding it to ensure uniform heating, and then rapidly cooling it.
- The rapid cooling prevents the formation of softer microstructures like pearlite and promotes the formation of martensite, which is extremely hard but brittle.
- Post-quenching, steels often undergo tempering to reduce brittleness and improve toughness.
-
Limitations of Quenching:
- Not all steels can be quenched. Low-carbon steels (below 0.3% carbon) lack sufficient carbon to form martensite and are not suitable for quenching.
- Over-quenching can lead to excessive brittleness and cracking, especially in high-carbon steels.
- The choice of quenching medium (water, oil, or air) depends on the steel type and desired properties. For example, water quenching is faster and used for high-carbon steels, while oil quenching is slower and suitable for alloy steels to minimize distortion and cracking.
-
Applications of Quenched Steels:
- Quenched steels are used in applications requiring high strength, hardness, and wear resistance, such as:
- Cutting tools (drills, saws, and blades).
- Automotive components (gears, axles, and crankshafts).
- Industrial machinery (bearings, shafts, and dies).
- Construction equipment (reinforcing bars and structural components).
- Quenched steels are used in applications requiring high strength, hardness, and wear resistance, such as:
By understanding the types of steel that can be quenched and the factors influencing the process, manufacturers and engineers can select the appropriate steel and heat treatment method to achieve the desired mechanical properties for specific applications.
Summary Table:
Type of Steel | Carbon Content | Alloying Elements | Applications |
---|---|---|---|
Medium-Carbon Steels | 0.3%–0.6% | - | Cutting tools, springs |
High-Carbon Steels | 0.6%–2.0% | - | Blades, dies |
Alloy Steels (e.g., 4140) | 0.3%–0.6% | Chromium, Molybdenum | Gears, axles, crankshafts |
Tool Steels (e.g., D2) | 0.6%–2.0% | Tungsten, Vanadium, Cobalt | Cutting and shaping tools |
Martensitic Stainless | 0.1%–1.2% | Chromium | High hardness, corrosion resistance |
Need help selecting the right steel for quenching? Contact our experts today for personalized advice!