Biomass pyrolysis for bio-oil production involves the use of various catalysts to enhance the yield and quality of the bio-oil. These catalysts play a crucial role in promoting desirable chemical reactions, reducing impurities, and improving the overall efficiency of the pyrolysis process. Commonly used catalysts include zeolites, clay minerals like kaolin, titanium compounds, metal nitrides (e.g., TiN and GaN), and biochar-based catalysts. The choice of catalyst depends on factors such as the type of biomass, desired end products, and specific process conditions. These catalysts help in cracking heavy hydrocarbons, condensing light hydrocarbons, and reducing oxygenates and acids, thereby producing a higher quality bio-oil that can be upgraded to drop-in fuels.
Key Points Explained:
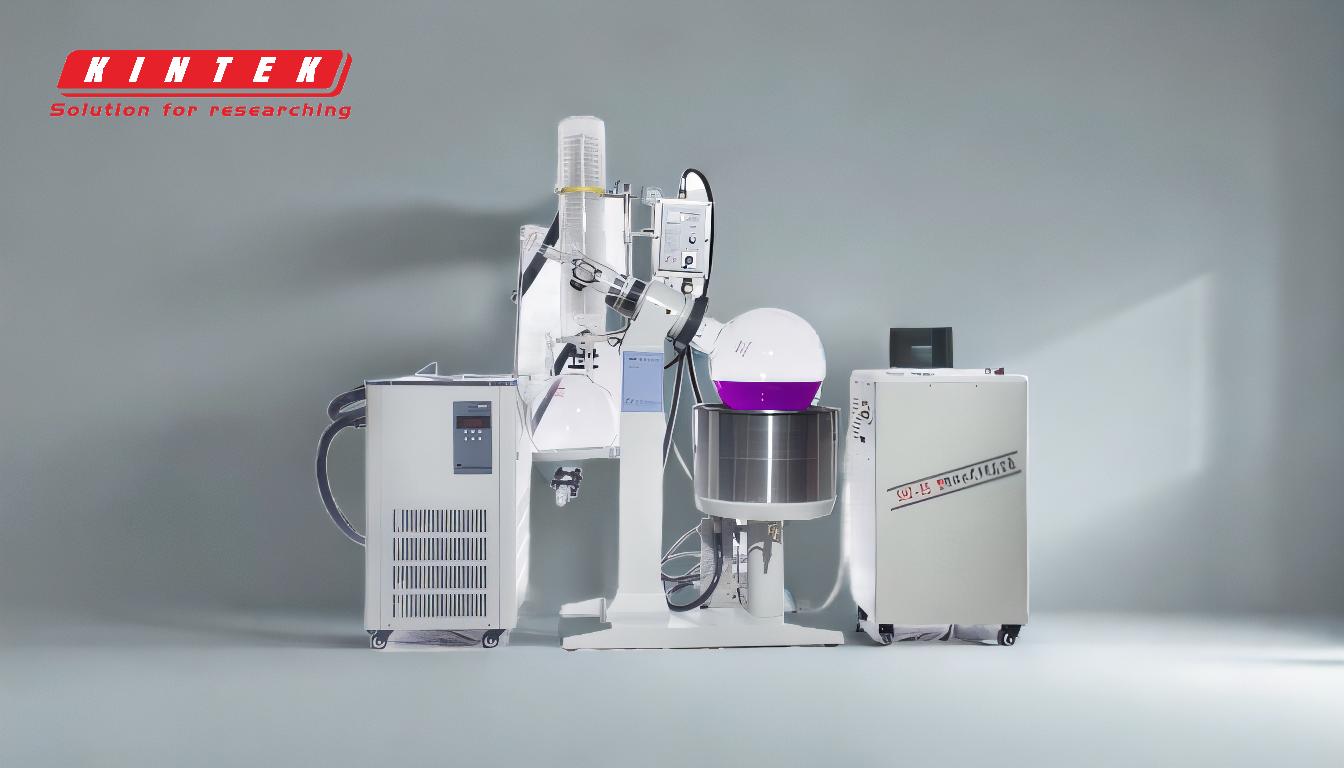
-
Role of Catalysts in Biomass Pyrolysis:
- Catalysts are essential in biomass pyrolysis as they enhance the yield and quality of bio-oil.
- They promote desirable chemical reactions, reduce impurities like oxygenates and acids, and improve the overall efficiency of the pyrolysis process.
-
Commonly Used Catalysts:
- Zeolites: These are porous materials composed of aluminum and silicon oxides. They are effective in cracking heavy hydrocarbons and condensing light hydrocarbons, which helps in producing C1, C2, and C3 hydrocarbons from biomass.
- Clay Minerals (e.g., Kaolin): Similar to zeolites, clay minerals like kaolin are used to selectively crack heavy hydrocarbons and condense light hydrocarbons, depending on the type of biomass and desired end products.
- Titanium Compounds and Metal Nitrides (e.g., TiN and GaN): These catalysts are particularly noted for promoting the production of furfural compounds during biomass fast pyrolysis.
- Biochar-Based Catalysts: These catalysts promote desirable chemical reactions during pyrolysis, improving the yield of valuable biofuels and chemicals.
-
Factors Influencing Catalyst Choice:
- Type of Biomass: Different types of biomass may require different catalysts to achieve optimal results.
- Desired End Products: The choice of catalyst can vary depending on whether the goal is to produce furfural, C1-C3 hydrocarbons, or other specific compounds.
- Process Conditions: The operating conditions of the pyrolysis process, such as temperature and pressure, can influence the effectiveness of different catalysts.
-
Benefits of Using Catalysts:
- Improved Bio-Oil Quality: Catalysts help in reducing the amount of oxygenates and acids, leading to a higher quality bio-oil.
- Enhanced Yield: Catalysts can increase the yield of valuable biofuels and chemicals, making the pyrolysis process more efficient.
- Upgradability: The use of catalysts produces a bio-oil that can be more easily upgraded to drop-in fuels, which contain only molecules found in current hydrocarbon fuels.
-
Specific Applications:
- Furfural Production: Catalysts like TiN and GaN are specifically noted for their role in promoting the production of furfural compounds during biomass fast pyrolysis.
- Hydrocarbon Production: Zeolites and clay minerals are effective in producing C1, C2, and C3 hydrocarbons from biomass, which are valuable components of biofuels.
By carefully selecting the appropriate catalyst based on the type of biomass, desired end products, and process conditions, the efficiency and quality of bio-oil production through biomass pyrolysis can be significantly enhanced.
Summary Table:
Catalyst Type | Key Role | Applications |
---|---|---|
Zeolites | Crack heavy hydrocarbons, condense light hydrocarbons | Production of C1, C2, and C3 hydrocarbons |
Clay Minerals (e.g., Kaolin) | Selectively crack heavy hydrocarbons, condense light hydrocarbons | Tailored bio-oil production based on biomass type |
Titanium Compounds & Metal Nitrides (e.g., TiN, GaN) | Promote furfural production | Furfural compound production during fast pyrolysis |
Biochar-Based Catalysts | Promote desirable chemical reactions, improve yield of biofuels and chemicals | Enhanced biofuel and chemical production |
Ready to optimize your biomass pyrolysis process? Contact our experts today to find the perfect catalyst for your needs!