PVD (Physical Vapor Deposition) and DLC (Diamond-Like Carbon) coatings are both advanced surface treatment technologies, each with unique properties and applications. PVD coatings are known for their high hardness, corrosion resistance, and ability to withstand high temperatures, making them ideal for cutting tools, molds, and decorative finishes. They are environmentally friendly, operate at lower temperatures, and can deposit a wide range of materials. On the other hand, DLC coatings, which mimic synthetic diamonds, offer even greater hardness and wear resistance, making them superior for applications requiring extreme durability, such as in high-end watches and precision tools. The choice between PVD and DLC depends on the specific requirements of the application, including hardness, wear resistance, and environmental considerations.
Key Points Explained:
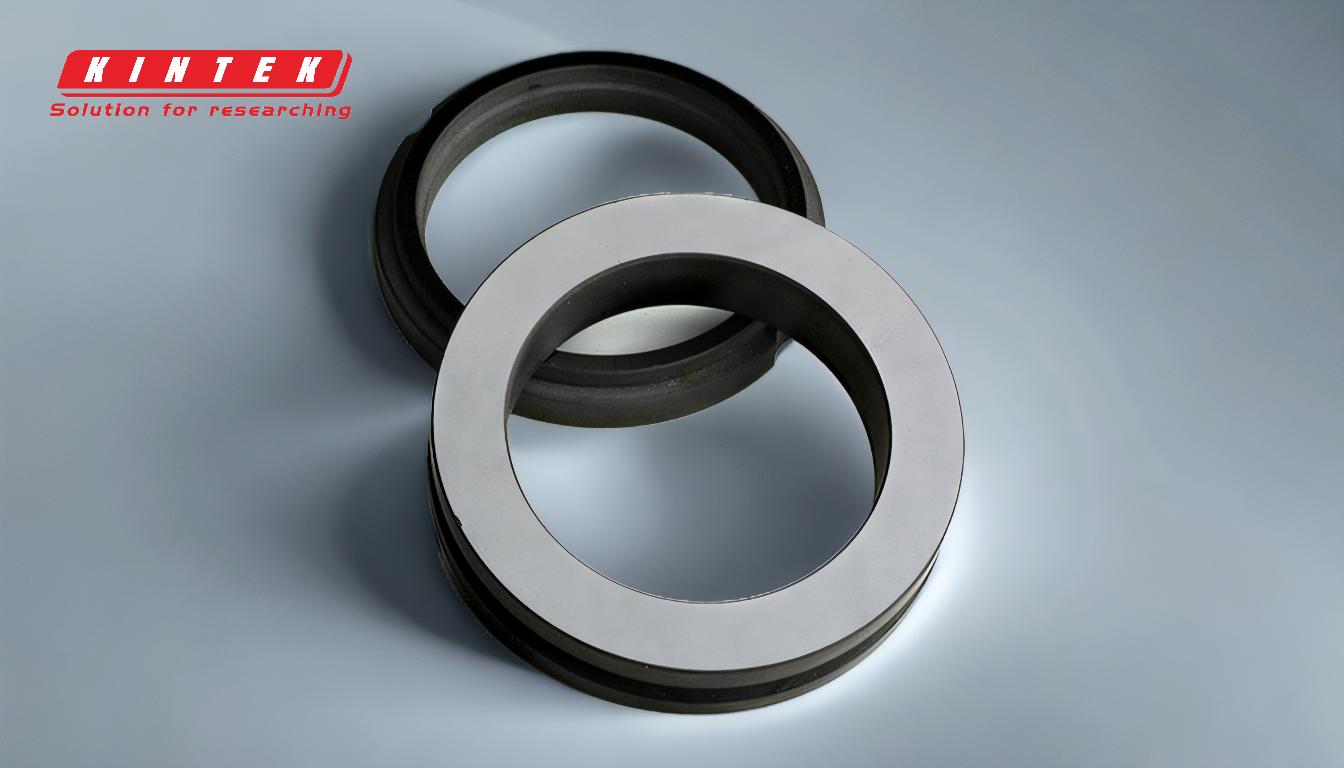
-
PVD Coating Advantages:
- High Hardness and Durability: PVD coatings provide excellent hardness and resistance to wear, corrosion, and high temperatures, making them suitable for demanding applications like cutting tools and molds.
- Environmental Friendliness: Unlike chemical-based methods, PVD is safer and more eco-friendly, reducing the need for toxic substances and extensive cleanups.
- Versatility in Materials: PVD can deposit a wide range of materials, including metals, alloys, and ceramics, offering flexibility in application.
- Aesthetic Appeal: PVD can replicate the appearance of expensive metals like gold and bronze, making it popular in jewelry and watchmaking.
-
DLC Coating Advantages:
- Superior Hardness: DLC coatings, created by blasting carbon particles onto surfaces, are significantly harder than PVD coatings, providing exceptional wear resistance.
- Enhanced Durability: The diamond-like structure of DLC coatings makes them ideal for applications requiring extreme durability, such as high-end watches and precision tools.
- Specialized Applications: DLC is particularly suited for industries where hardness and wear resistance are paramount, such as aerospace and automotive.
-
Process Differences:
- PVD Process: Operates under vacuum conditions at high temperatures, using physical processes to deposit thin films. It is faster and suitable for a broader range of materials.
- DLC Process: Mimics synthetic diamond creation, resulting in a denser and harder coating. However, it may take longer to apply compared to PVD.
-
Application Suitability:
- PVD: Ideal for industries requiring precise, thin coatings with minimal distortion, such as plastic injection molding, fine blanking tools, and optical coatings.
- DLC: Best for applications needing extreme hardness and wear resistance, such as high-performance watches and precision engineering components.
-
Environmental and Safety Considerations:
- PVD: Safer and more environmentally friendly, with reduced use of toxic substances and lower energy consumption.
- DLC: While also environmentally friendly, the process may require more specialized equipment and longer processing times.
In conclusion, the choice between PVD and DLC coatings depends on the specific needs of the application. PVD is more versatile and environmentally friendly, while DLC offers superior hardness and wear resistance. Both technologies have their unique strengths, making them suitable for different industrial and decorative applications.
Summary Table:
Feature | PVD Coating | DLC Coating |
---|---|---|
Hardness | High, but lower than DLC | Superior hardness, diamond-like |
Wear Resistance | Excellent | Exceptional |
Corrosion Resistance | High | Moderate |
Temperature Tolerance | High | Moderate |
Material Versatility | Wide range of materials | Limited to carbon-based coatings |
Environmental Impact | Eco-friendly, low toxicity | Eco-friendly, but requires more energy |
Applications | Cutting tools, molds, decorative finishes | High-end watches, precision tools |
Still unsure which coating is right for your application? Contact our experts today for personalized advice!