Silicon carbide and tungsten carbide are both extremely hard materials, but they differ in their hardness levels and applications. Tungsten carbide, composed of equal parts tungsten and carbon, is known for its exceptional hardness, comparable to corundum. It requires abrasives like cubic boron nitride or diamond powder for polishing. Silicon carbide, on the other hand, is a synthetic compound of silicon and carbon, often used in abrasive applications due to its hardness and thermal conductivity. While both materials are hard, silicon carbide is generally considered harder than tungsten carbide, making it suitable for more demanding applications.
Key Points Explained:
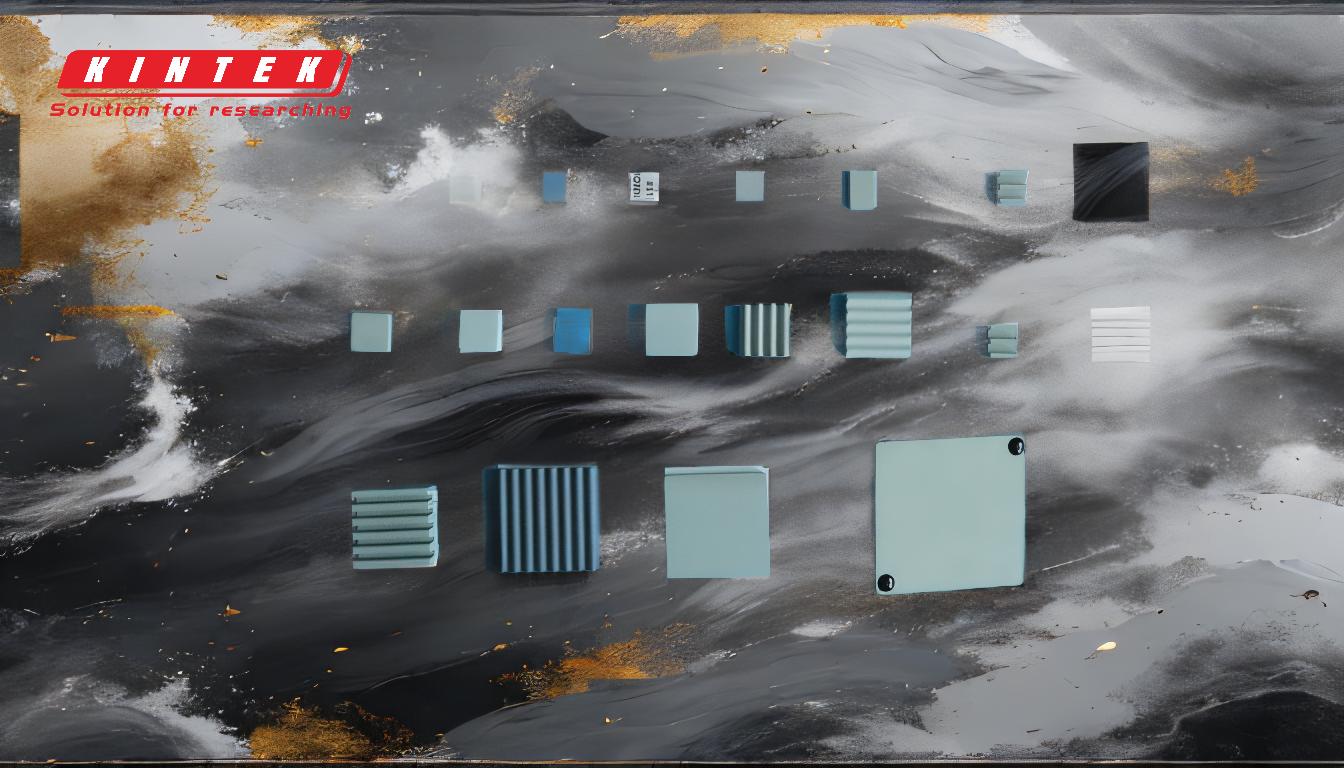
-
Composition and Hardness of Tungsten Carbide:
- Tungsten carbide is a chemical compound made of equal parts tungsten and carbon.
- Its hardness is comparable to corundum, which is a naturally occurring form of aluminum oxide.
- Due to its high hardness, tungsten carbide is often used in cutting tools, wear-resistant parts, and abrasives.
- Polishing and finishing tungsten carbide require abrasives with superior hardness, such as cubic boron nitride or diamond powder.
-
Composition and Hardness of Silicon Carbide:
- Silicon carbide is a synthetic compound composed of silicon and carbon.
- It is known for its high hardness, thermal conductivity, and chemical resistance.
- Silicon carbide is commonly used in abrasive applications, such as grinding wheels and cutting tools, due to its ability to withstand high temperatures and wear.
-
Comparison of Hardness:
- While both materials are extremely hard, silicon carbide is generally considered harder than tungsten carbide.
- This makes silicon carbide suitable for more demanding applications where higher hardness and thermal stability are required.
-
Applications and Uses:
- Tungsten carbide is often used in cutting tools, wear-resistant parts, and abrasives due to its hardness and durability.
- Silicon carbide is used in abrasive applications, high-temperature environments, and electronics due to its hardness, thermal conductivity, and chemical resistance.
-
Polishing and Finishing:
- Polishing tungsten carbide requires abrasives with superior hardness, such as cubic boron nitride or diamond powder.
- Silicon carbide, being harder, can be used as an abrasive material itself, often in the form of grinding wheels or cutting tools.
In conclusion, while both silicon carbide and tungsten carbide are extremely hard materials, silicon carbide is generally considered harder and is used in more demanding applications. Tungsten carbide, with its high hardness and durability, is widely used in cutting tools and wear-resistant parts. For more information on related topics, you can explore the coiled tungsten filament.
Summary Table:
Property | Silicon Carbide | Tungsten Carbide |
---|---|---|
Hardness | Higher | Slightly lower |
Composition | Silicon and carbon | Tungsten and carbon |
Applications | Abrasives, electronics | Cutting tools, wear parts |
Polishing Requirements | Self-abrasive | Cubic boron nitride/diamond |
Thermal Conductivity | High | Moderate |
Need help choosing the right material for your application? Contact our experts today for personalized advice!