Several deposition techniques are used for the deposition of metals, with resistive and electron beam evaporative techniques being the most common and flexible for most metals. Other methods include chemical vapor deposition (CVD), sputtering, and physical vapor deposition (PVD) techniques like Arc-PVD and pulsed laser deposition. These techniques vary in their mechanisms and applications but are all effective for creating thin metal films on various surfaces.
Key Points Explained:
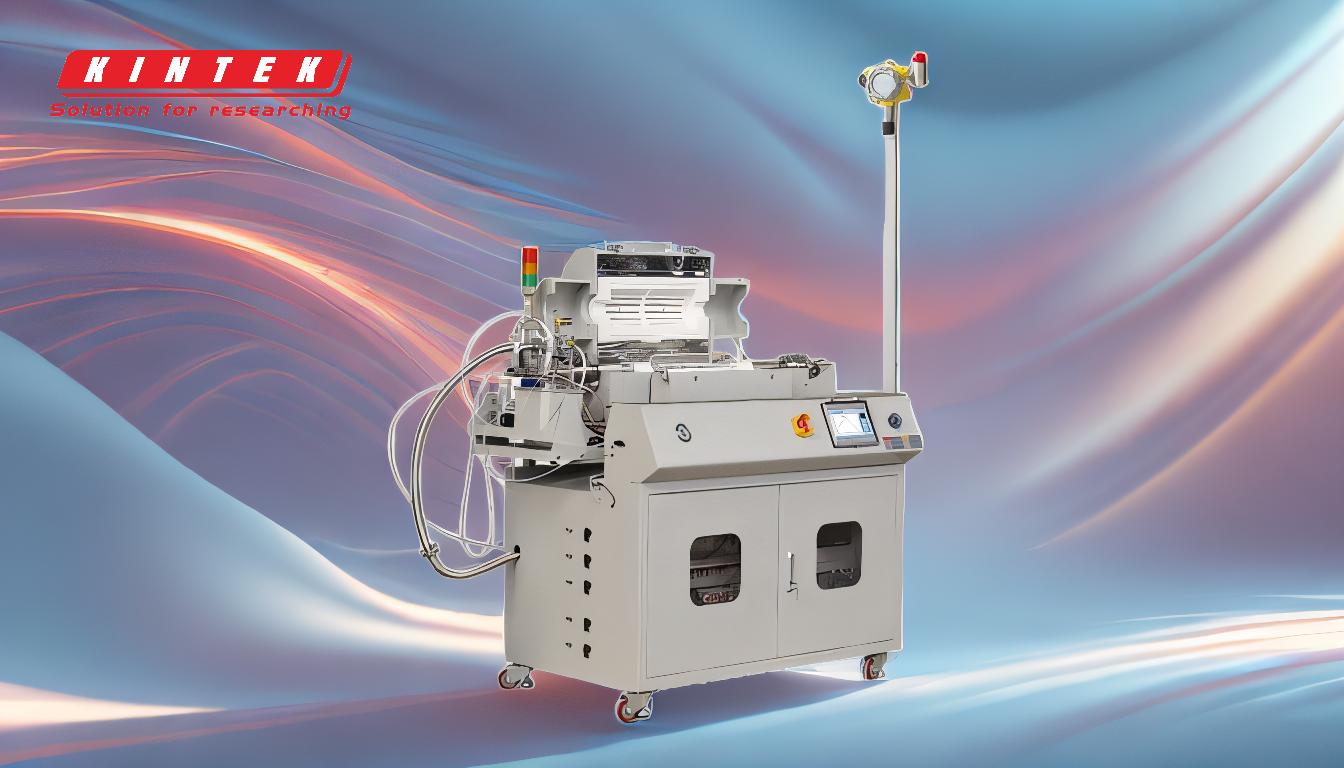
-
Resistive and Electron Beam Evaporative Techniques:
- Mechanism: These techniques involve heating the metal until it evaporates and then condensing it onto a substrate.
- Flexibility: They are highly flexible and can be used for depositing most metals.
- Applications: Commonly used in microelectronics and optical coatings.
-
Chemical Vapor Deposition (CVD):
- Mechanism: Involves the chemical reaction of gaseous precursors to form a solid metal film on the substrate.
- Applications: Used in semiconductor manufacturing and for creating high-purity metal films.
-
Sputtering:
- Mechanism: Involves bombarding a target material with high-energy particles to eject atoms, which then deposit onto the substrate.
- Applications: Widely used in the production of thin films for electronics, optics, and decorative coatings.
-
Physical Vapor Deposition (PVD) Techniques:
- Arc-PVD (Cathodic Arc Deposition): Uses an electric arc to vaporize the metal, which then deposits onto the substrate.
- Pulsed Laser Deposition: Uses high-power laser pulses to ablate material from the target, which then deposits onto the substrate.
- Applications: These techniques are used for creating high-quality, dense metal films, often in research and high-tech industries.
-
Thermal Evaporation:
- Mechanism: Similar to resistive evaporation but typically uses a filament or boat to heat the metal.
- Applications: Used in the deposition of simple metals and alloys, often in simpler applications compared to electron beam evaporation.
Each of these techniques has its own advantages and is chosen based on the specific requirements of the application, such as film purity, thickness, and the nature of the substrate.
Summary Table:
Technique | Mechanism | Applications |
---|---|---|
Resistive & Electron Beam Evaporation | Heating metal until it evaporates and condenses on a substrate | Microelectronics, optical coatings |
Chemical Vapor Deposition (CVD) | Chemical reaction of gaseous precursors to form a solid metal film | Semiconductor manufacturing, high-purity films |
Sputtering | Bombarding target material with high-energy particles to eject atoms | Electronics, optics, decorative coatings |
Arc-PVD | Electric arc vaporizes metal, which deposits onto the substrate | Research, high-tech industries |
Pulsed Laser Deposition | High-power laser pulses ablate material from the target for deposition | High-quality, dense metal films |
Thermal Evaporation | Similar to resistive evaporation, uses a filament or boat to heat metal | Deposition of simple metals and alloys |
Need help selecting the right metal deposition technique for your project? Contact our experts today!