CVD (Chemical Vapor Deposition) and PVD (Physical Vapor Deposition) are two widely used thin-film deposition techniques, each with its own set of advantages and limitations. The choice between CVD and PVD depends on the specific application, material requirements, and operational constraints. CVD is better suited for applications requiring uniform coatings in complex geometries and high-temperature environments, while PVD is ideal for temperature-sensitive materials and applications needing faster deposition rates. Below, we explore the key differences, advantages, and limitations of both methods to help determine which is better for specific use cases.
Key Points Explained:
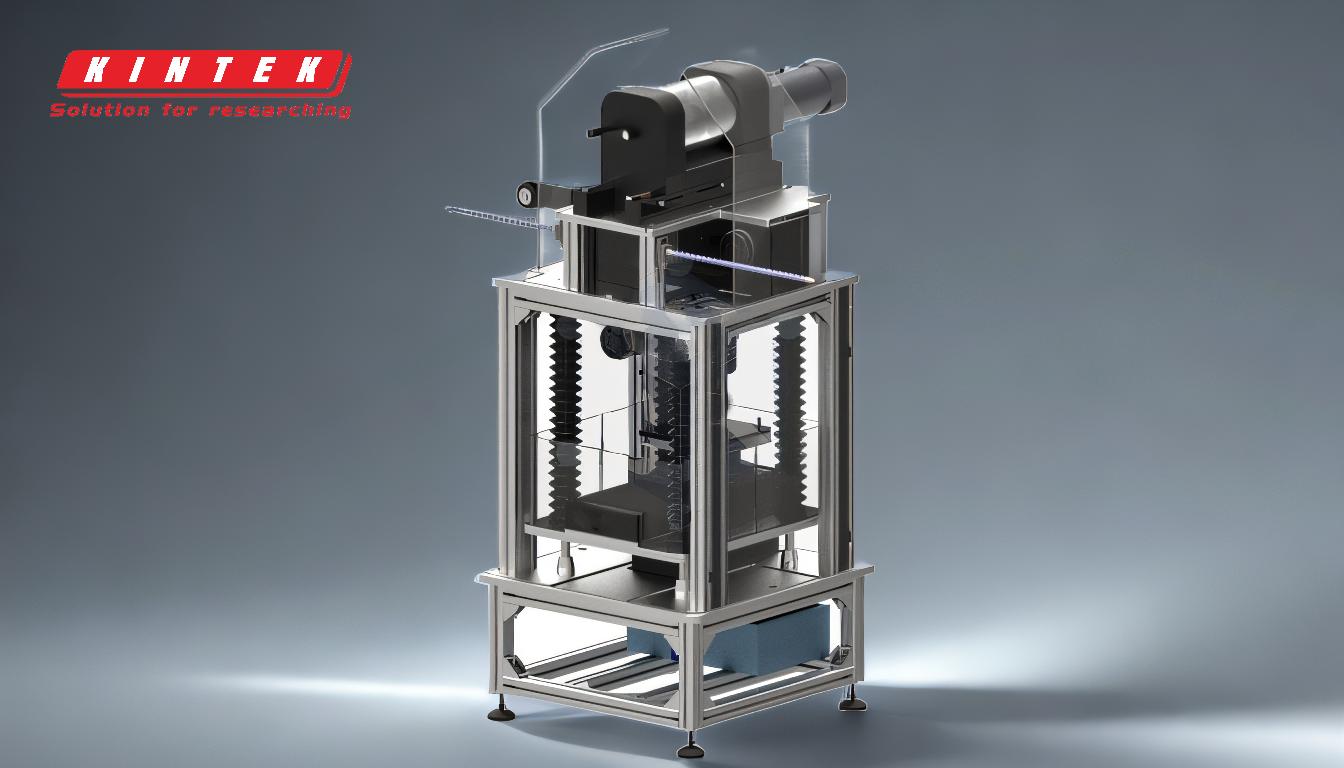
-
Deposition Mechanism:
- CVD: Involves chemical reactions between gaseous precursors and the substrate surface, forming a solid coating. This process is multidirectional, allowing for uniform coverage even in complex geometries and deep holes.
- PVD: Relies on physical processes like sputtering or evaporation to deposit solid materials onto the substrate. It is a line-of-sight process, meaning it is less effective for coating shaded areas or complex shapes.
-
Operating Temperatures:
- CVD: Operates at higher temperatures (450°C to 1050°C), making it unsuitable for temperature-sensitive materials like certain polymers or low-melting-point substrates.
- PVD: Operates at lower temperatures (250°C to 450°C), making it a better choice for temperature-sensitive materials.
-
Coating Material Range:
- CVD: Primarily used for depositing ceramics and polymers. It can utilize volatile chemical compounds, enabling the deposition of elements that are difficult to evaporate.
- PVD: Can deposit a broader range of materials, including metals, alloys, and ceramics, making it more versatile for various applications.
-
Coating Uniformity and Density:
- CVD: Produces denser and more uniform coatings due to the chemical reaction process, which ensures thorough coverage even in complex geometries.
- PVD: Coatings are less dense and less uniform but can be applied faster, making it suitable for applications where speed is critical.
-
Line-of-Sight Limitations:
- CVD: Not limited by line-of-sight effects, allowing for coating deposition in deep holes, shaded areas, and complex geometries.
- PVD: Limited by line-of-sight, making it less effective for coating intricate shapes or areas not directly exposed to the deposition source.
-
Energy Consumption and Thermal Constraints:
- CVD: Requires high energy costs to heat the gas phase and substrate, which can be a disadvantage in terms of operational expenses and environmental impact.
- PVD: Operates in a vacuum and at lower temperatures, reducing energy consumption and making it more suitable for temperature-sensitive applications.
-
Applications:
- CVD: Commonly used in semiconductor manufacturing, optoelectronics, and applications requiring high-purity, uniform coatings.
- PVD: Widely used in decorative coatings, wear-resistant coatings, and applications involving temperature-sensitive materials.
-
Material Waste:
- CVD: Produces less material waste since only the heated area is coated. Advanced techniques like computer-controlled lasers can further enhance selective coating.
- PVD: May result in more material waste due to the nature of the physical deposition process.
-
Film Thickness and Smoothness:
- CVD: Typically produces thicker and smoother films, which are ideal for applications requiring high durability and precision.
- PVD: Produces thinner films with less smoothness, suitable for applications where speed and versatility are prioritized.
-
Cost and Complexity:
- CVD: Easier to operate and does not require a complicated setup, but the high energy costs and thermal constraints can increase operational expenses.
- PVD: Requires a vacuum environment, which can add to the complexity and cost of the setup, but it offers faster deposition rates and lower energy consumption.
In conclusion, the choice between CVD and PVD depends on the specific requirements of the application. CVD is better for high-temperature, high-precision applications requiring uniform coatings, while PVD is more suitable for temperature-sensitive materials and applications needing faster deposition rates. Both methods have their unique advantages and limitations, and the decision should be based on a thorough evaluation of the operational and material requirements.
Summary Table:
Aspect | CVD | PVD |
---|---|---|
Deposition Mechanism | Chemical reactions, multidirectional, uniform coverage | Physical processes, line-of-sight, less effective for complex shapes |
Operating Temperatures | High (450°C to 1050°C), unsuitable for temperature-sensitive materials | Low (250°C to 450°C), ideal for temperature-sensitive materials |
Coating Material Range | Primarily ceramics and polymers | Metals, alloys, ceramics, broader material versatility |
Coating Uniformity | Denser, more uniform coatings | Less dense, less uniform, but faster deposition rates |
Line-of-Sight | Not limited, effective for complex geometries | Limited, less effective for shaded areas |
Energy Consumption | High energy costs due to high temperatures | Lower energy consumption, operates in a vacuum |
Applications | Semiconductor, optoelectronics, high-purity coatings | Decorative, wear-resistant, temperature-sensitive applications |
Material Waste | Less waste, selective coating techniques | More waste due to physical deposition process |
Film Thickness | Thicker, smoother films | Thinner, less smooth films |
Cost and Complexity | Easier setup, higher operational costs | Complex vacuum setup, faster deposition, lower energy costs |
Still unsure which thin-film deposition technique is right for your application? Contact our experts today for personalized advice!