When selecting the best type of plastic for pyrolysis, it is essential to consider factors such as the yield of pyrolysis oil, the potential for toxic gas emissions, and the ease of processing. Plastics like HDPE, LDPE, PP, and PS are generally suitable for pyrolysis due to their high oil yield and low toxicity during the process. In contrast, PVC and PET are unsuitable because they release toxic gases when pyrolyzed. The quality of the plastic waste, including its composition, moisture content, and contamination levels, also significantly impacts the quality and yield of the pyrolysis oil. Advanced technologies like Pyrolysis Oil Purification can help mitigate variations in raw material quality, ensuring consistent oil output.
Key Points Explained:
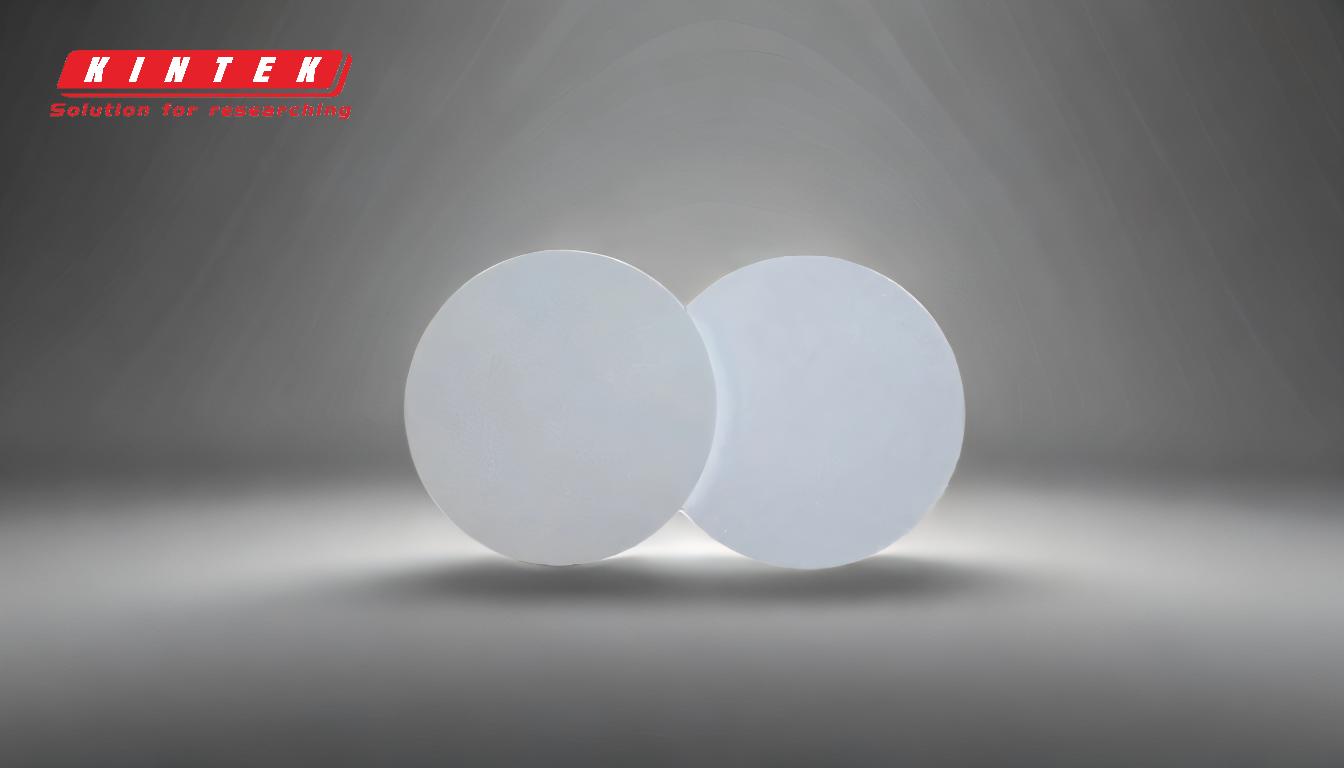
-
Suitable Plastics for Pyrolysis:
- HDPE (High-Density Polyethylene): Known for its high oil yield and low toxicity during pyrolysis.
- LDPE (Low-Density Polyethylene): Similar to HDPE, it produces a good yield of pyrolysis oil.
- PP (Polypropylene): Offers a moderate to high oil yield and is commonly found in packaging materials.
- PS (Polystyrene): Produces the highest liquid oil yield among the plastics, making it highly efficient for pyrolysis.
-
Unsuitable Plastics for Pyrolysis:
- PVC (Polyvinyl Chloride): Releases toxic gases such as hydrogen chloride when pyrolyzed, making it unsuitable for the process.
- PET (Polyethylene Terephthalate): Also produces toxic gases and is not recommended for pyrolysis.
-
Impact of Plastic Quality on Pyrolysis:
- Source and Composition: The origin and type of plastic significantly affect the pyrolysis oil yield and quality.
- Moisture Content: High moisture levels can reduce the efficiency of the pyrolysis process.
- Non-Plastic Content: Contaminants and non-plastic materials can degrade the quality of the pyrolysis oil.
-
Technological Solutions:
- Pyrolysis Oil Purification: This technology helps in producing consistent oil quality by addressing variations in raw material quality.
-
Common Plastics Recycled via Pyrolysis:
- Woven Bags, Acrylic, Packaging Bags, Disposable Cups, Freezer Food Bags, Cotton Swabs: These items are often made from HDPE, LDPE, PP, or PS, making them suitable for pyrolysis.
By focusing on these key points, one can make informed decisions about the types of plastics to use in pyrolysis, ensuring optimal yield and minimizing environmental hazards.
Summary Table:
Category | Details |
---|---|
Suitable Plastics | HDPE, LDPE, PP, PS (high oil yield, low toxicity) |
Unsuitable Plastics | PVC, PET (release toxic gases during pyrolysis) |
Plastic Quality Factors | Source, composition, moisture content, non-plastic contaminants |
Technological Solutions | Pyrolysis Oil Purification (ensures consistent oil quality) |
Common Recycled Plastics | Woven bags, acrylic, packaging bags, disposable cups, freezer food bags, cotton swabs |
Ready to optimize your pyrolysis process? Contact our experts today for tailored solutions!