The use of different sizes of balls in a ball mill is a critical factor in optimizing the grinding process. The size of the balls affects the efficiency, productivity, and fineness of the grinding operation. Smaller balls are more effective for producing finer particles due to their increased surface area and ability to create more collisions per unit time, while larger balls are better suited for breaking down larger chunks of material. The combination of various ball sizes ensures a more uniform grinding process, as it allows for both coarse and fine grinding to occur simultaneously. This approach maximizes the efficiency of the mill, reduces energy consumption, and ensures the desired particle size distribution is achieved.
Key Points Explained:
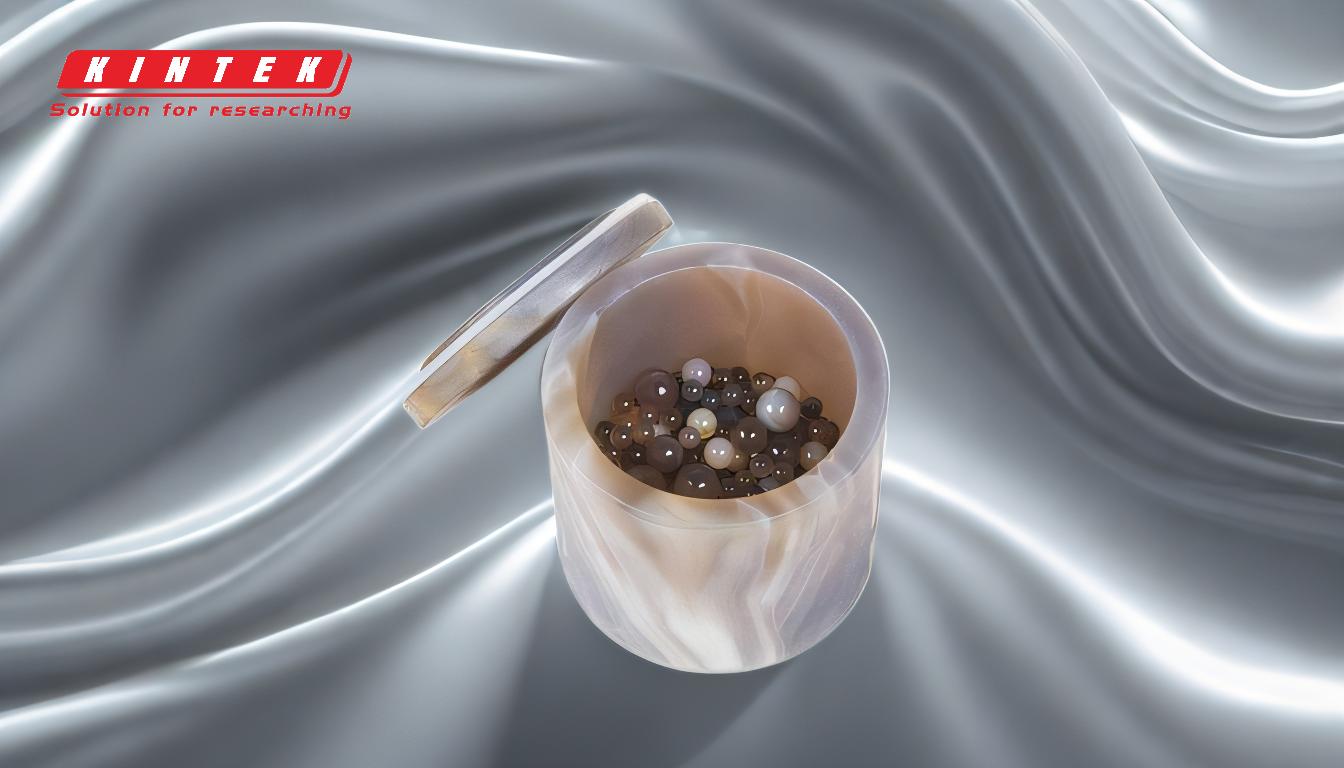
-
Impact of Ball Size on Grinding Efficiency:
- Smaller balls have a larger surface area relative to their mass, which increases the number of collisions with the material being ground. This results in finer particle sizes.
- Larger balls are more effective at breaking down larger chunks of material due to their greater kinetic energy upon impact.
- A mix of different ball sizes ensures that both coarse and fine grinding occur simultaneously, leading to a more uniform particle size distribution.
-
Residence Time and Particle Size:
- Smaller balls require longer grinding times to achieve finer particles because they generate more frequent but less forceful impacts.
- Larger balls can achieve coarser grinding more quickly due to their higher impact energy, but they may not be as effective for producing very fine particles.
-
Optimization of Ball Mill Productivity:
- The productivity of a ball mill depends on factors such as drum diameter, the ratio of drum diameter to length, and the physical-chemical properties of the feed material.
- Using a combination of different ball sizes helps to optimize the grinding process by ensuring that the mill can handle a wide range of particle sizes efficiently.
-
Energy Efficiency and Cost-Effectiveness:
- Using a mix of ball sizes can reduce energy consumption by ensuring that the grinding process is as efficient as possible. This is because the mill does not need to rely solely on either very small or very large balls, which can be less efficient when used alone.
- The combination of different ball sizes also reduces wear and tear on the mill, as the load is distributed more evenly across the balls.
-
Role of Ball Size in Achieving Desired Fineness:
- Smaller balls are essential for achieving very fine particles, as they can create more collisions and thus more opportunities for particle size reduction.
- Larger balls are necessary for initial size reduction of larger feed material, ensuring that the smaller balls can then work more effectively on the finer particles.
-
Practical Considerations for Ball Size Selection:
- The choice of ball sizes should be based on the specific requirements of the grinding process, including the desired particle size distribution, the hardness of the material being ground, and the capacity of the mill.
- It is often necessary to experiment with different ball size distributions to find the optimal combination for a particular application.
-
Importance of Ball Size Distribution:
- A well-distributed range of ball sizes ensures that the mill can handle a variety of particle sizes, from coarse to fine, without overloading or underutilizing the grinding capacity.
- This distribution helps to maintain a consistent grinding environment, which is crucial for achieving the desired product quality.
In summary, the use of different sizes of balls in a ball mill is essential for optimizing the grinding process. It ensures that the mill can efficiently handle a wide range of particle sizes, from coarse to fine, while minimizing energy consumption and wear on the equipment. By carefully selecting and combining different ball sizes, operators can achieve the desired particle size distribution and improve the overall efficiency of the grinding operation.
Summary Table:
Ball Size | Advantages | Applications |
---|---|---|
Small Balls | - Increased surface area for finer particles - More collisions per unit time |
Producing very fine particles |
Large Balls | - Higher kinetic energy for breaking large chunks - Faster coarse grinding |
Initial size reduction of feed material |
Mixed Sizes | - Simultaneous coarse and fine grinding - Uniform particle size distribution - Reduced energy consumption |
Optimizing grinding efficiency and productivity |
Want to optimize your ball mill grinding process? Contact our experts today for tailored solutions!