Crucible breakage is a common issue that can significantly disrupt operations and increase costs. The primary reasons for crucible breakage are related to improper temperature management during heating and cooling processes. Specifically, incorrect ramp/soak levels and abrupt power supply shutdowns or insufficient ramp-down times after deposition are the main culprits. These issues cause rapid solidification of the melt, leading to thermal stress on the crucible liner and eventual breakage. Additionally, selecting the right crucible for your specific application is crucial, as factors like furnace type, alloy composition, melting temperatures, and operational requirements all play a role in ensuring the crucible's longevity.
Key Points Explained:
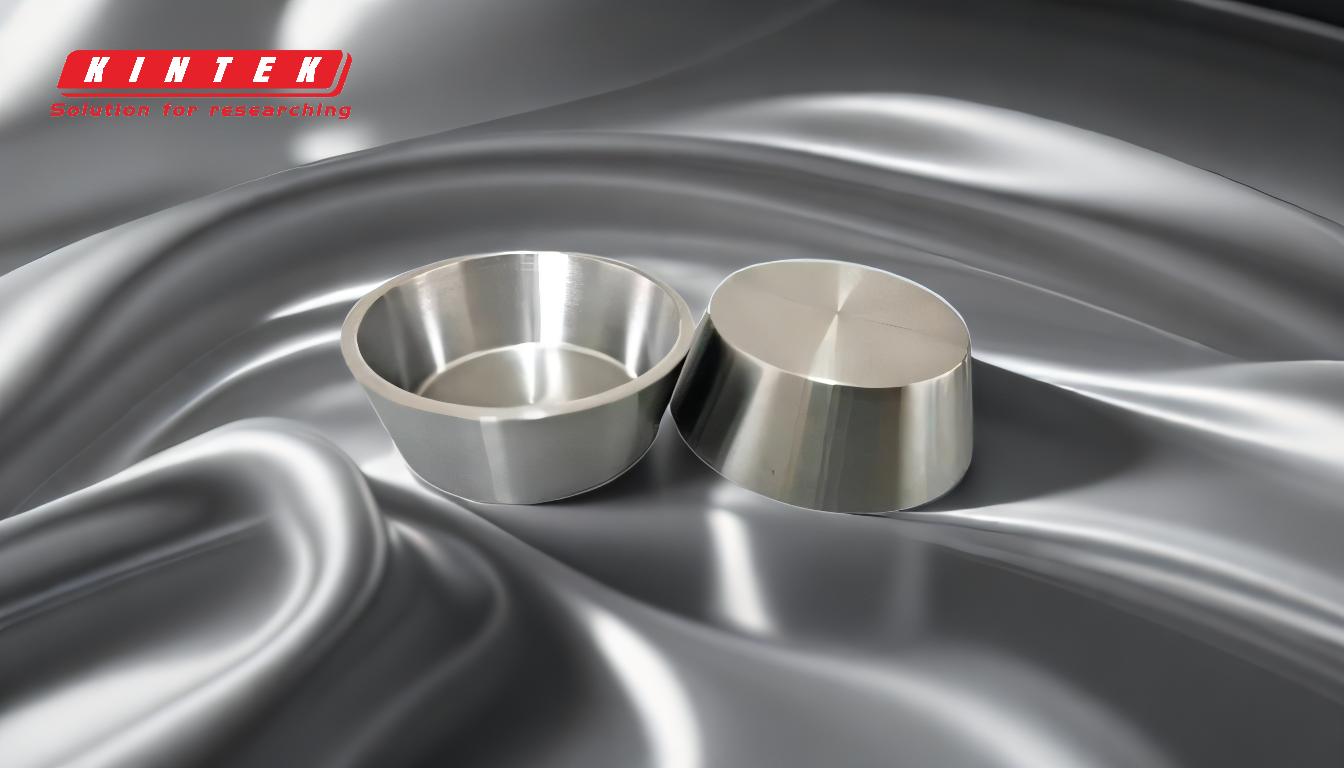
-
Incorrect Ramp/Soak Levels:
- Explanation: Ramp/soak levels refer to the rate at which the temperature is increased (ramp) and the duration it is held at a specific temperature (soak). If these levels are not optimized for the material being melted, it can lead to uneven heating or cooling, causing thermal stress on the crucible.
- Impact: Uneven thermal expansion and contraction can create micro-cracks in the crucible material, which over time can lead to complete breakage. This is especially critical in high-temperature applications where the crucible is subjected to extreme thermal cycling.
-
Improper Power Supply Shutdown or Short Ramp-Down Time:
- Explanation: Abruptly shutting off the power supply or having a very short ramp-down time after deposition causes the molten material to solidify rapidly. This rapid solidification can create internal stresses within the crucible.
- Impact: The rapid cooling can cause the crucible liner to contract unevenly, leading to cracks or even catastrophic failure. This is particularly problematic in processes where the crucible is repeatedly subjected to such thermal shocks.
-
Crucible Selection:
- Explanation: Selecting the right crucible is critical to avoid breakage. Factors to consider include the capacity and dimensions of the furnace, the type of alloy being melted, melting and holding temperatures, temperature change rates, and specific operational requirements.
- Impact: A crucible that is not suited to the specific application can lead to premature failure. For example, a crucible designed for lower temperatures may not withstand the thermal stresses of a high-temperature process, leading to breakage.
-
Operational Practices:
- Explanation: How the crucible is charged, the use of fluxes or additions, degassing or refining processes, slag or dross removal methods, and how the crucible is emptied all play a role in its longevity.
- Impact: Improper charging can lead to uneven heating, while aggressive fluxing or slag removal can erode the crucible liner. Ensuring that these processes are carried out correctly can significantly extend the life of the crucible.
-
Avoiding Alloy Cross-Contamination:
- Explanation: In some applications, it is crucial to avoid cross-contamination between different alloys. This may require the use of dedicated crucibles for specific alloys.
- Impact: Cross-contamination can lead to chemical reactions that weaken the crucible material, making it more susceptible to breakage. Using dedicated crucibles for specific alloys can mitigate this risk.
-
Thermal Stress Management:
- Explanation: Managing thermal stress is key to preventing crucible breakage. This includes optimizing the heating and cooling cycles to minimize thermal shock.
- Impact: Proper thermal stress management can significantly reduce the likelihood of crucible breakage, ensuring a longer service life and more reliable operation.
-
Material Compatibility:
- Explanation: The crucible material must be compatible with the alloy being melted. Different materials have different thermal and chemical properties, and using an incompatible material can lead to premature failure.
- Impact: For example, a graphite crucible may be suitable for melting certain alloys but could react with others, leading to erosion or breakage. Ensuring material compatibility is essential for crucible longevity.
-
Regular Maintenance and Inspection:
- Explanation: Regular maintenance and inspection of the crucible can help identify potential issues before they lead to breakage.
- Impact: Cracks or erosion can be detected early, allowing for timely replacement or repair. This proactive approach can prevent unexpected failures and reduce downtime.
By addressing these key points, you can significantly reduce the likelihood of crucible breakage, ensuring more reliable and cost-effective operations.
Summary Table:
Cause | Explanation | Impact |
---|---|---|
Incorrect Ramp/Soak Levels | Uneven heating or cooling due to improper temperature control. | Micro-cracks and eventual breakage due to thermal stress. |
Improper Power Supply Shutdown | Rapid solidification from abrupt shutdowns or short ramp-down times. | Uneven contraction leading to cracks or catastrophic failure. |
Poor Crucible Selection | Using a crucible unsuitable for the application (e.g., wrong material or size). | Premature failure under thermal or chemical stress. |
Inefficient Operational Practices | Improper charging, fluxing, or slag removal. | Erosion and uneven heating, reducing crucible lifespan. |
Alloy Cross-Contamination | Chemical reactions from mixing incompatible alloys. | Weakening of crucible material, increasing breakage risk. |
Inadequate Thermal Stress Management | Failure to optimize heating and cooling cycles. | Higher risk of thermal shock and breakage. |
Material Incompatibility | Using crucible materials that react with the alloy. | Erosion or breakage due to chemical reactions. |
Lack of Maintenance | Skipping regular inspections and maintenance. | Undetected cracks or erosion leading to unexpected failures. |
Prevent crucible breakage and optimize your operations—contact our experts today for tailored solutions!