Coating thickness is a critical parameter in manufacturing and surface treatment processes, as it directly impacts product quality, performance, and cost efficiency. Proper coating thickness ensures that materials meet functional and aesthetic requirements, such as wear resistance, rust prevention, and appearance. Excessive coating can lead to unnecessary material usage and increased production costs, while insufficient coating may compromise the product's durability and performance. Accurate measurement and control of coating thickness are essential for maintaining high-quality standards, optimizing costs, and ensuring consistent product performance across industries like metal finishing, electroplating, and galvanizing.
Key Points Explained:
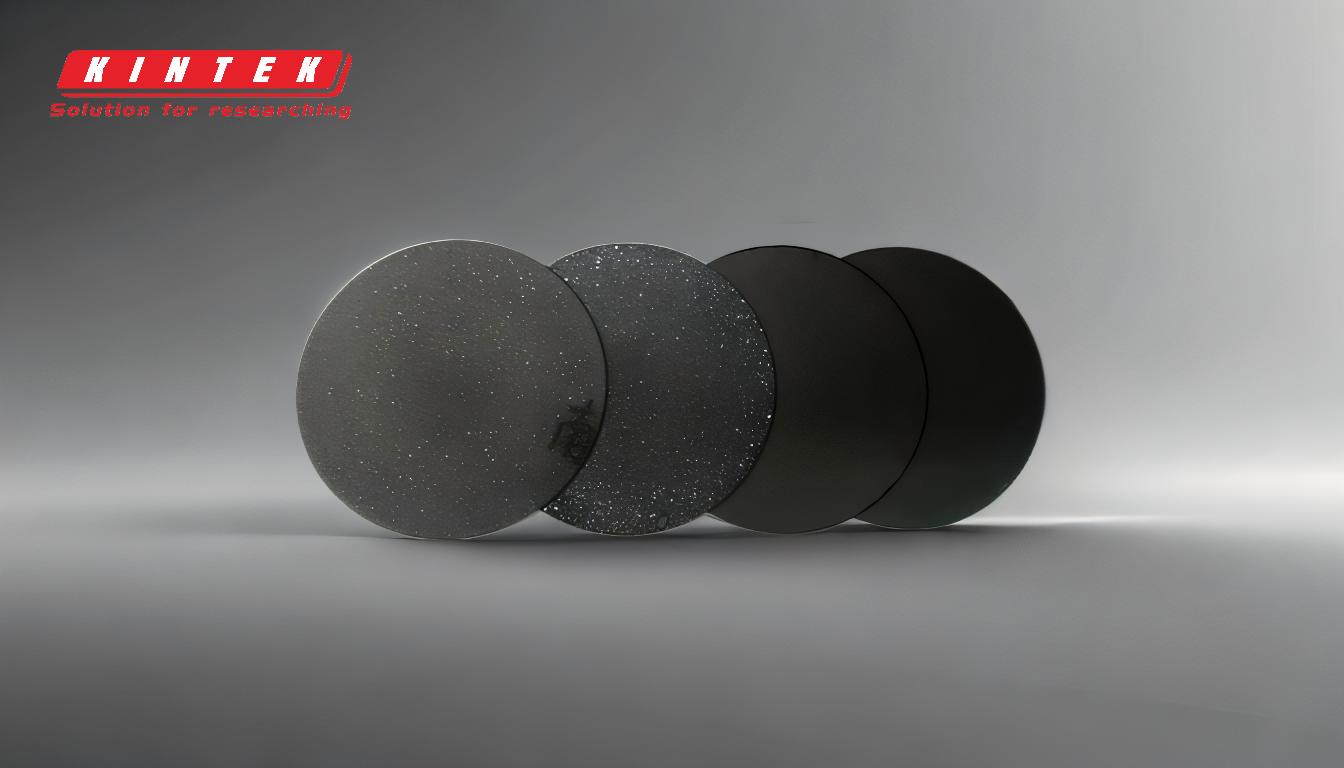
-
Ensures Product Quality and Performance
- Coating thickness directly affects the functional properties of a product, such as wear resistance, corrosion protection, and durability.
- For example, in metal finishing processes like electroplating and galvanizing, precise coating thickness is crucial to prevent defects and ensure the longevity of metal components.
- Insufficient coating may fail to meet performance requirements, leading to premature wear or failure, while excessive coating can alter material properties and reduce effectiveness.
-
Controls Manufacturing Costs
- Excessive coating thickness results in higher material consumption, increasing production costs without providing additional benefits.
- Accurate measurement and control of coating thickness help manufacturers optimize material usage, reducing waste and improving cost efficiency.
- Conversely, insufficient coating may lead to rework or product rejection, further escalating costs.
-
Meets Aesthetic and Functional Requirements
- Coating thickness impacts the appearance and surface finish of products, which is critical in industries where aesthetics matter, such as automotive or consumer goods.
- Functional requirements, such as electrical conductivity or thermal insulation, also depend on precise coating thickness to ensure optimal performance.
-
Prevents Defects and Ensures Consistency
- Inconsistent coating thickness can lead to defects like uneven surfaces, poor adhesion, or inadequate protection, compromising product reliability.
- Precise control of coating thickness ensures uniformity across batches, maintaining consistent quality and reducing the risk of defects.
-
Supports Compliance with Industry Standards
- Many industries have strict regulations and standards for coating thickness to ensure safety, reliability, and performance.
- Accurate measurement and control help manufacturers comply with these standards, avoiding legal or financial penalties and enhancing customer trust.
-
Enhances Product Lifespan and Durability
- Proper coating thickness is essential for protecting materials from environmental factors like moisture, chemicals, and UV exposure.
- For example, in galvanizing, the correct zinc coating thickness ensures long-term rust prevention, extending the lifespan of metal components.
By understanding and controlling coating thickness, manufacturers can achieve a balance between quality, performance, and cost, ensuring that products meet both customer expectations and industry standards.
Summary Table:
Key Benefit | Description |
---|---|
Ensures Product Quality | Affects wear resistance, corrosion protection, and durability. |
Controls Manufacturing Costs | Optimizes material usage, reduces waste, and prevents rework. |
Meets Aesthetic Requirements | Impacts appearance and surface finish for industries like automotive. |
Prevents Defects | Ensures uniformity and reduces risks of poor adhesion or inadequate protection. |
Supports Industry Compliance | Helps meet safety and performance standards, avoiding penalties. |
Enhances Product Lifespan | Protects against environmental factors, extending durability. |
Need help optimizing coating thickness for your products? Contact our experts today!