Diamond coatings are crucial due to their exceptional properties, which make them highly versatile and valuable in a wide range of applications. These coatings exhibit high hardness, excellent thermal conductivity, chemical inertness, and optical transparency, making them suitable for industries ranging from manufacturing to renewable energy. Their ability to reduce friction in mechanical parts, enhance tool efficiency, and extend tool life further underscores their importance. Additionally, the tunable microstructure and morphology of diamond coatings allow for customization to meet specific application requirements, making them indispensable in modern technology and industrial processes.
Key Points Explained:
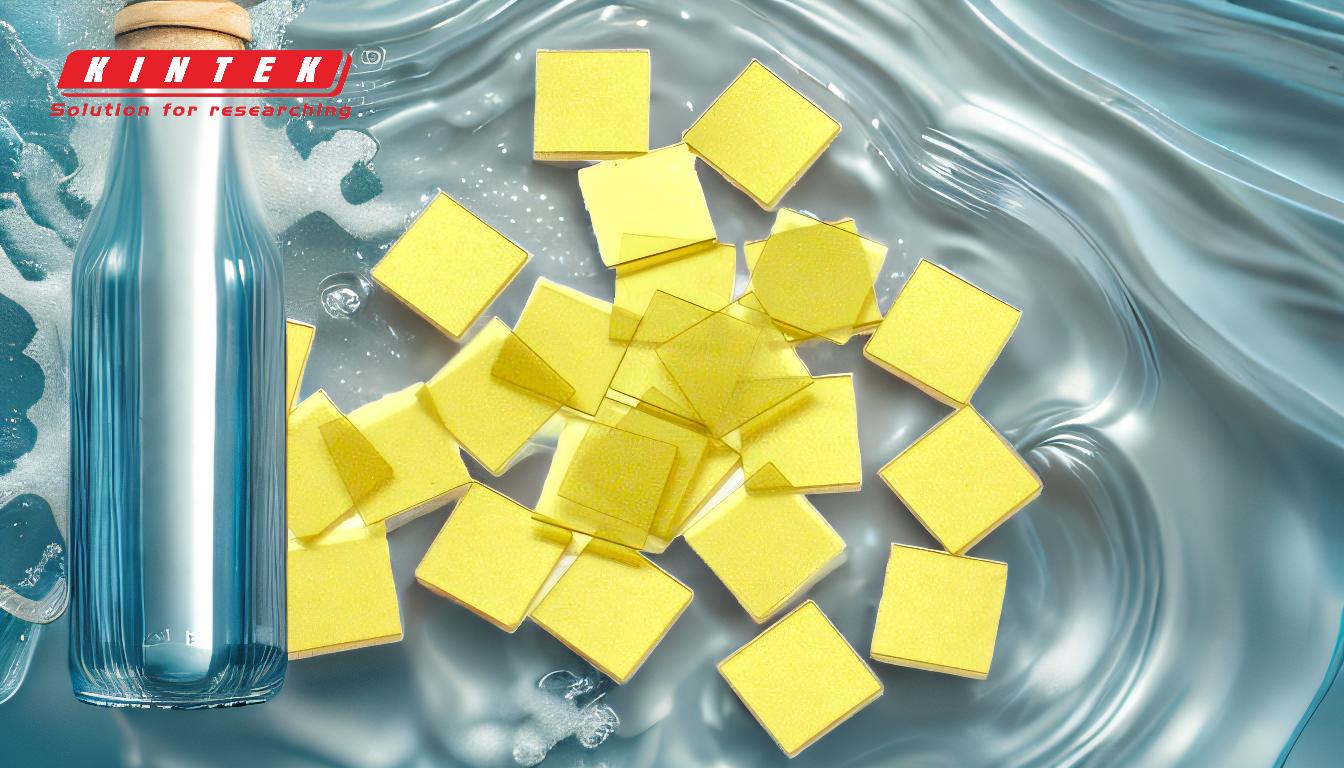
-
Exceptional Mechanical Properties
- Diamond coatings are renowned for their high hardness, which makes them ideal for protective coatings and tool coatings. This hardness ensures durability and resistance to wear and tear, extending the lifespan of components.
- They also exhibit excellent thermal conductivity, which is critical in applications where heat dissipation is essential, such as in electronic devices and high-performance machinery.
-
Chemical Inertness and Robustness
- Diamond coatings are chemically inert, meaning they do not react with most substances. This property makes them suitable for use in harsh environments, such as in chemical processing or biosensors, where resistance to corrosion and degradation is crucial.
- Their mechanical robustness ensures they can withstand physical stresses, making them reliable for long-term use.
-
Reduction in Friction
- Diamond coatings have been shown to reduce friction in moving mechanical parts. For example, Nissan reported a 40% reduction in friction in engine parts when using diamond film. This reduction leads to improved energy efficiency, reduced wear, and lower maintenance costs in applications like automotive and windmill components.
-
Tunable Microstructure and Morphology
- The grain size, surface roughness, and crystallinity of diamond coatings can be tailored by controlling deposition parameters and gas phase composition. This tunability allows manufacturers to customize coatings for specific applications, such as high-precision tools or optical devices.
- The ability to fine-tune these properties ensures that diamond coatings can meet the demands of modern machinery industries, where precision and efficiency are paramount.
-
Versatility in Applications
- Diamond coatings are used in a wide range of industries, including:
- Solar cells and optical devices: Their high optical transparency and semi-conductivity make them ideal for these applications.
- Transparent electrodes and photochemical applications: Their unique properties enable efficient energy conversion and chemical processes.
- Biosensors and protective coatings: Their chemical inertness and durability make them suitable for sensitive and demanding environments.
- The combination of nanometer and diamond properties in nanometer diamond films further enhances their utility, particularly in tool coatings that require high precision and extended tool life.
- Diamond coatings are used in a wide range of industries, including:
-
Economic and Environmental Benefits
- By reducing friction and wear, diamond coatings contribute to energy savings and reduced material waste, aligning with sustainability goals.
- The extended lifespan of tools and components coated with diamond reduces the need for frequent replacements, leading to cost savings and lower environmental impact.
-
Advancements in Modern Technology
- The ability to tailor diamond coatings to specific needs has enabled advancements in high-performance machinery, renewable energy technologies, and precision manufacturing.
- Their use in cutting-edge applications, such as biosensors and photochemical devices, highlights their importance in driving innovation across multiple sectors.
In summary, diamond coatings are important because they combine unparalleled mechanical, thermal, and chemical properties with the ability to be customized for specific applications. Their role in reducing friction, enhancing durability, and enabling high-precision processes makes them indispensable in modern industrial and technological advancements.
Summary Table:
Key Benefits of Diamond Coatings | Applications |
---|---|
High hardness and durability | Tool coatings, protective layers |
Excellent thermal conductivity | Electronics, high-performance machinery |
Chemical inertness and robustness | Biosensors, chemical processing |
Reduced friction (e.g., 40% reduction) | Automotive, windmill components |
Tunable microstructure and morphology | High-precision tools, optical devices |
Versatility across industries | Solar cells, transparent electrodes |
Economic and environmental benefits | Energy savings, reduced material waste |
Ready to enhance your industrial processes with diamond coatings? Contact us today to learn more!