The industrial process of titanium is expensive due to its unique material properties and the specialized techniques required for its extraction, refining, and machining. Titanium's high affinity for oxygen and nitrogen necessitates processing in inert or vacuum environments, which increases costs. Additionally, its high toughness and low thermal conductivity make machining difficult, requiring specialized tools and slower processing speeds. These factors, combined with the energy-intensive nature of titanium extraction and refining, contribute to its high production costs.
Key Points Explained:
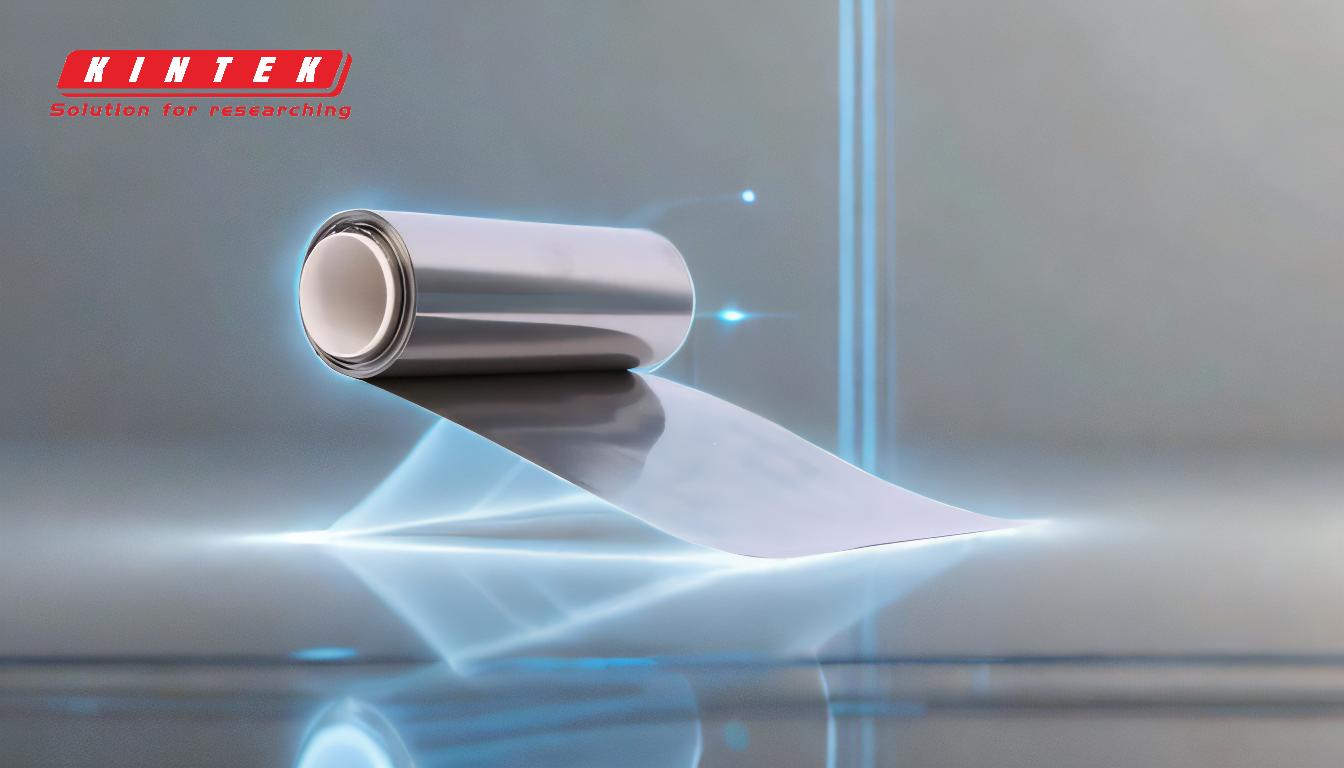
-
High Affinity for Oxygen and Nitrogen
- Titanium readily reacts with oxygen and nitrogen at high temperatures, forming oxides and nitrides that degrade its mechanical properties.
- To prevent contamination, titanium must be processed in inert atmospheres (e.g., argon) or vacuum environments, which are expensive to maintain.
- This requirement adds significant costs to both extraction and fabrication processes.
-
Difficult Machining Characteristics
- Titanium's high toughness and low thermal conductivity make it challenging to machine.
- The material tends to gall and weld to cutting tools, leading to rapid tool wear and frequent replacements.
- Machining must be done at slower speeds to manage heat buildup, increasing production time and costs.
-
Energy-Intensive Extraction and Refining
- Titanium is extracted from ores like ilmenite and rutile using the Kroll process, which involves multiple high-temperature steps and consumes large amounts of energy.
- The Kroll process produces titanium in a sponge form, which must then be further refined and melted using specialized equipment, adding to the overall cost.
- Alternative extraction methods, such as the FFC Cambridge process, are still under development and not yet commercially viable at scale.
-
Specialized Fabrication Techniques
- Titanium's unique properties require specialized techniques for casting, welding, and forming.
- For example, welding titanium requires shielding gases to prevent contamination, and casting must be done in vacuum or inert environments.
- These techniques demand advanced equipment and skilled labor, further driving up costs.
-
Limited Economies of Scale
- Titanium production volumes are relatively low compared to other metals like steel or aluminum, limiting economies of scale.
- The high cost of raw materials and processing discourages widespread use, creating a feedback loop that keeps production volumes and costs high.
-
High Material Waste
- Due to the difficulty in machining and forming titanium, there is often significant material waste during manufacturing.
- The cost of raw titanium compounds this issue, as wasted material represents a substantial financial loss.
-
Corrosion Resistance and Durability
- While titanium's corrosion resistance and durability are advantageous for end-use applications, they also contribute to higher costs.
- The material's resistance to corrosion means it can replace more expensive alloys or coatings, but its initial cost remains a barrier.
In summary, the high cost of titanium processing stems from its unique chemical and physical properties, which demand specialized and energy-intensive techniques. These factors, combined with limited production volumes and high material waste, make titanium one of the most expensive industrial metals.
Summary Table:
Key Factor | Impact on Cost |
---|---|
High affinity for oxygen/nitrogen | Requires inert/vacuum environments, increasing processing costs |
Difficult machining characteristics | High tool wear, slower speeds, and specialized tools raise production expenses |
Energy-intensive extraction | Kroll process consumes large amounts of energy, adding to overall costs |
Specialized fabrication techniques | Advanced equipment and skilled labor drive up costs |
Limited economies of scale | Low production volumes prevent cost reductions |
High material waste | Significant waste during machining and forming increases raw material costs |
Corrosion resistance and durability | While beneficial, these properties contribute to higher initial costs |
Learn how titanium's unique properties impact your projects—contact our experts today for tailored solutions!