Chemical vapor deposition (CVD) is widely used for coating carbide tools due to its ability to create high-quality, durable, and uniform thin films. This process leverages chemical reactions to deposit materials onto surfaces, offering exceptional control over the coating's properties. CVD is particularly advantageous for carbide tools because it enhances their hardness, wear resistance, and thermal stability, which are critical for industrial applications. The method's versatility, precision, and ability to coat complex geometries make it a preferred choice for improving the performance and longevity of carbide tools.
Key Points Explained:
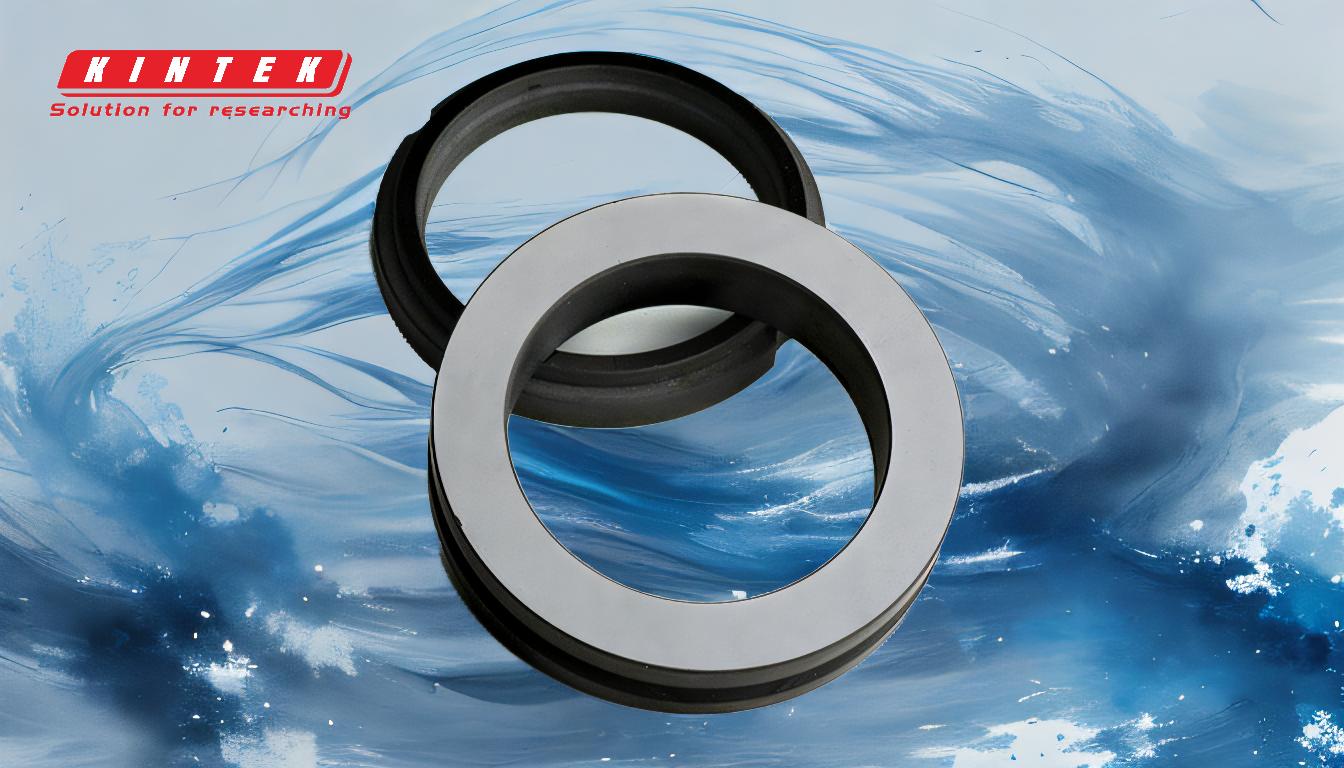
-
High-Quality Coatings:
- CVD produces coatings with high purity, density, and uniformity, which are essential for carbide tools used in demanding environments. These coatings improve the tools' hardness and resistance to wear, extending their lifespan and reducing maintenance costs.
-
Versatility in Material Deposition:
- CVD can deposit a wide range of materials, including ceramics, metals, and graphene, allowing for tailored coatings that meet specific performance requirements. This versatility ensures that carbide tools can be optimized for various applications, such as cutting, drilling, or milling.
-
Uniform Coating on Complex Geometries:
- The non-line-of-sight nature of CVD enables even coating of components with intricate shapes, which is crucial for carbide tools that often have complex designs. This ensures consistent performance across the entire tool surface.
-
Enhanced Durability and Performance:
- CVD coatings provide excellent adhesion and durability, enabling carbide tools to withstand high-stress environments, extreme temperatures, and abrasive conditions. This makes them suitable for heavy-duty industrial applications.
-
Control Over Coating Properties:
- By adjusting deposition parameters such as temperature, pressure, and gas composition, manufacturers can fine-tune the properties of the coating. This control allows for the creation of coatings with specific hardness, thermal stability, or corrosion resistance.
-
Cost-Effectiveness and Scalability:
- CVD is relatively affordable and scalable, making it a practical choice for large-scale production. Its high deposition rates and ability to produce consistent results contribute to its cost-effectiveness.
-
Applications in High-Performance Industries:
- CVD-coated carbide tools are widely used in industries such as aerospace, automotive, and manufacturing, where precision, durability, and performance are critical. The coatings enhance the tools' ability to handle challenging materials and conditions.
In summary, chemical vapor deposition is the preferred method for coating carbide tools due to its ability to produce high-quality, durable, and uniform coatings that enhance performance and longevity. Its versatility, precision, and cost-effectiveness make it an ideal choice for industrial applications.
Summary Table:
Key Benefits of CVD for Carbide Tools | Details |
---|---|
High-Quality Coatings | Produces high purity, density, and uniformity for improved hardness and wear resistance. |
Versatility in Material Deposition | Deposits ceramics, metals, and graphene for tailored performance. |
Uniform Coating on Complex Geometries | Ensures consistent performance on intricate tool designs. |
Enhanced Durability and Performance | Withstands high-stress, extreme temperatures, and abrasive conditions. |
Control Over Coating Properties | Adjustable parameters for specific hardness, thermal stability, and corrosion resistance. |
Cost-Effectiveness and Scalability | Affordable and scalable for large-scale production. |
Applications in High-Performance Industries | Widely used in aerospace, automotive, and manufacturing. |
Ready to enhance your carbide tools with CVD coatings? Contact our experts today to learn more!