Stainless steel can be used as a crucible for melting certain metals, such as aluminum and zinc, due to its higher melting point compared to these metals. However, it is not ideal for all applications because of issues like flaking or scaling of the interior surface, which can lead to contamination of the melt and thinning of the crucible walls. Protective coatings, such as marcote-7, can mitigate some of these issues, but stainless steel crucibles still have limitations compared to materials specifically designed for high-temperature applications, like graphite or ceramic crucibles.
Key Points Explained:
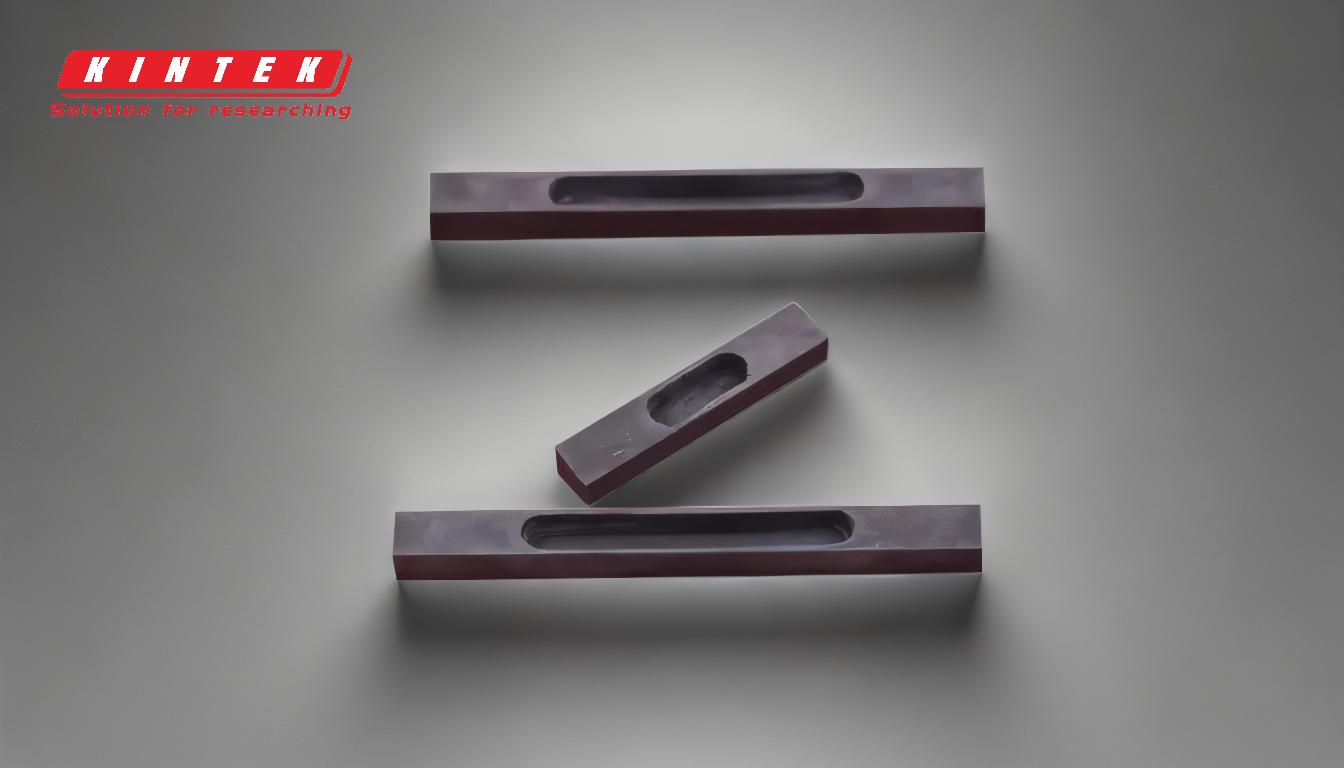
-
Suitability for Low-Melting-Point Metals:
- Stainless steel has a melting point significantly higher than metals like aluminum (660°C) and zinc (420°C). This makes it suitable for melting these metals without the crucible itself melting or deforming.
- However, stainless steel is not suitable for melting metals with higher melting points, such as copper (1085°C) or iron (1538°C), as these temperatures approach or exceed the limits of stainless steel.
-
Scaling and Contamination Risks:
- A major drawback of using stainless steel as a crucible is the flaking or scaling of its interior surface when exposed to high temperatures. This occurs due to oxidation and thermal stress.
- The flakes can contaminate the molten metal, affecting its purity and properties. This is particularly problematic in applications requiring high-purity metals, such as in electronics or aerospace industries.
- Over time, scaling can also thin the walls of the crucible, reducing its structural integrity and lifespan.
-
Protective Coatings:
- Applying protective coatings, such as marcote-7, can help reduce scaling and extend the life of the stainless steel crucible. These coatings act as a barrier between the molten metal and the crucible surface, minimizing direct contact and oxidation.
- However, coatings are not a perfect solution. They can wear off over time, especially with repeated use, and may require reapplication, adding to maintenance costs.
-
Comparison with Other Crucible Materials:
- Graphite and ceramic crucibles are often preferred for high-temperature applications because they are more resistant to scaling and contamination. They also have higher thermal stability and can withstand more extreme conditions.
- Stainless steel crucibles are generally more cost-effective and easier to manufacture than graphite or ceramic crucibles, making them a viable option for low-temperature applications or when budget constraints are a concern.
-
Practical Considerations:
- When choosing a crucible material, consider the specific requirements of your application, including the melting temperature of the metal, the desired purity of the melt, and the expected lifespan of the crucible.
- For occasional or low-temperature use, stainless steel crucibles may be sufficient, especially if protective coatings are used. However, for high-temperature or high-purity applications, alternative materials like graphite or ceramics are likely a better choice.
In summary, while stainless steel can function as a crucible for melting low-melting-point metals, its limitations—such as scaling and contamination risks—make it less ideal for high-temperature or high-purity applications. Protective coatings can mitigate some of these issues, but they do not eliminate them entirely. For demanding applications, alternative materials like graphite or ceramics are generally more suitable.
Summary Table:
Aspect | Stainless Steel Crucibles | Graphite/Ceramic Crucibles |
---|---|---|
Suitable Metals | Aluminum, zinc (low melting point) | High melting point metals (e.g., copper, iron) |
Scaling/Contamination | High risk due to flaking and oxidation | Low risk, more resistant to scaling and contamination |
Protective Coatings | Required (e.g., marcote-7) but may wear off over time | Not required |
Cost | Cost-effective and easier to manufacture | More expensive but better for high-temperature applications |
Lifespan | Shorter due to scaling and thinning | Longer lifespan due to higher thermal stability |
Need help choosing the right crucible for your application? Contact our experts today for personalized advice!