Zirconium oxide (zirconia) typically sinters at high temperatures ranging from 1400°C to 1600°C, with most processes occurring closer to 1500°C to 1550°C. This temperature range is critical for achieving the desired hardness, density, and strength of the final product. Sintering at these temperatures transforms the zirconia from a monoclinic to a polytetragonal structure, significantly enhancing its mechanical properties. However, deviations from this optimal range, even by 150°C, can lead to reduced strength due to grain growth. Specialized high-temperature sintering furnaces are required for this process, as standard porcelain furnaces cannot reach these temperatures.
Key Points Explained:
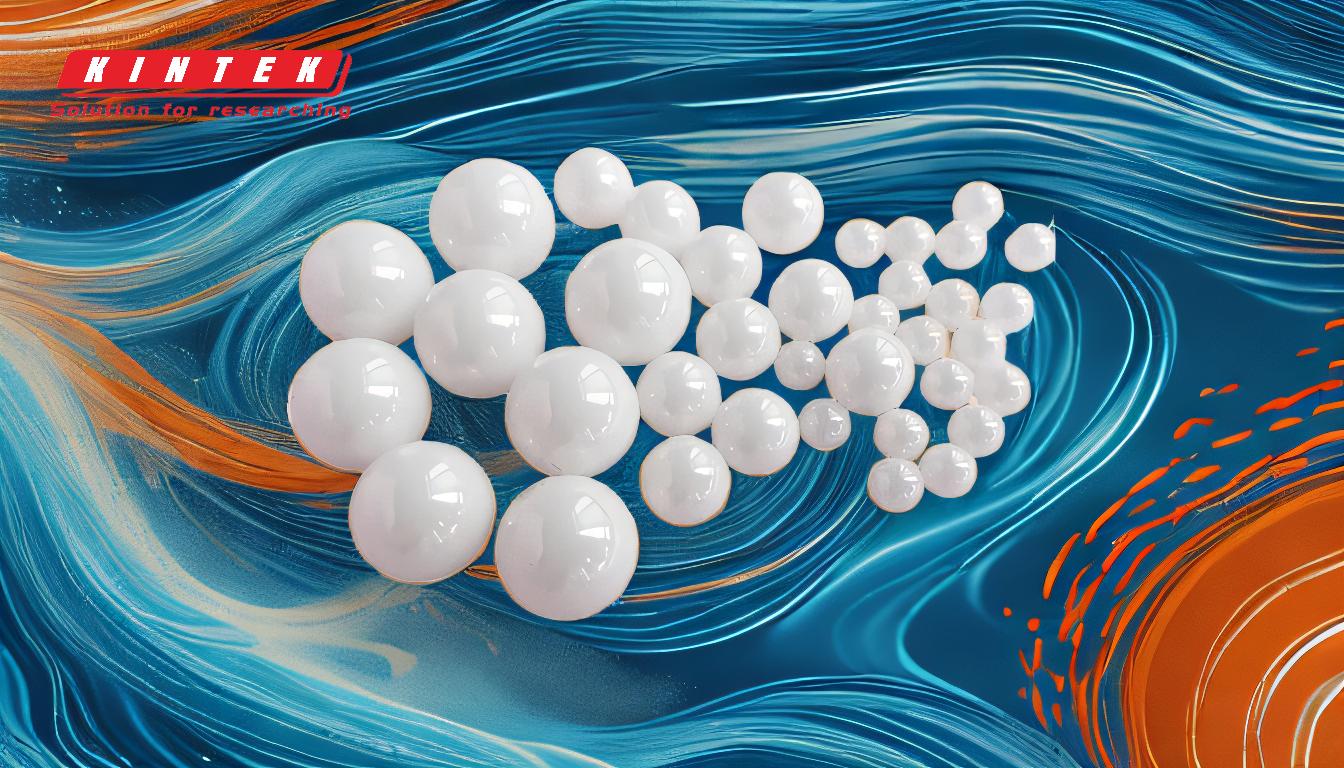
-
Optimal Sintering Temperature Range:
- Zirconia sinters effectively between 1400°C and 1600°C, with most processes targeting 1500°C to 1550°C.
- This range ensures the transformation from a monoclinic to a polytetragonal crystal structure, which is essential for achieving high density and strength.
- Sintering at these temperatures results in zirconia reaching close to 99% of its theoretical maximum density.
-
Impact of Temperature on Strength:
- Firing zirconia at 1500°C to 1550°C produces maximum strength, with values around 1280 MPa.
- Deviating from this range by ±150°C can significantly reduce strength:
- At 1600°C, strength drops to about 980 MPa.
- At 1700°C, strength further decreases to approximately 600 MPa.
- This reduction in strength is attributed to excessive grain growth at higher temperatures.
-
Heat Rise Rate:
- A slow heat rise rate of 4°C to 10°C per minute is recommended during sintering.
- This controlled heating ensures uniform densification and minimizes internal stresses, which could otherwise lead to defects in the final product.
-
Furnace Requirements:
- Specialized high-temperature sintering furnaces are necessary for processing zirconia.
- Standard porcelain furnaces, typically used for glass infiltration firing, cannot achieve the high temperatures required for zirconia sintering.
-
Structural Transformation:
- The transformation from monoclinic to polytetragonal zirconia occurs at 1100°C to 1200°C.
- However, achieving full densification and optimal mechanical properties requires sintering at higher temperatures (1400°C to 1600°C).
-
Practical Considerations for Purchasers:
- When selecting a sintering furnace, ensure it can consistently maintain temperatures within the 1500°C to 1550°C range.
- Verify the furnace's temperature accuracy and uniformity, as small deviations can impact the final product's strength.
- Consider furnaces with programmable heat rise rates to achieve the recommended 4°C to 10°C per minute heating profile.
By adhering to these guidelines, purchasers can ensure the production of high-quality zirconia components with optimal mechanical properties.
Summary Table:
Key Factor | Details |
---|---|
Optimal Sintering Range | 1400°C–1600°C (target 1500°C–1550°C) |
Strength at 1500°C–1550°C | ~1280 MPa |
Strength Reduction at 1600°C | ~980 MPa |
Strength Reduction at 1700°C | ~600 MPa |
Heat Rise Rate | 4°C–10°C per minute |
Furnace Type | Specialized high-temperature sintering furnace (standard porcelain furnaces insufficient) |
Density Achieved | ~99% of theoretical maximum |
Structural Transformation | Monoclinic to polytetragonal at 1100°C–1200°C |
Ensure your zirconia sintering process meets industry standards—contact our experts today for tailored solutions!