An induction coil can indeed melt steel, as it generates a magnetic field that transfers energy to the metal, heating it to its melting point. The process relies on the coil's design, the electrical current, and the properties of the metal being melted. Steel, with a melting point of approximately 1370°C (2500°F), can be effectively melted using an induction furnace. The efficiency of this process depends on factors such as the coil's material, the strength of the magnetic field, and the crucible's design. This method is widely used in industrial applications due to its precision and energy efficiency.
Key Points Explained:
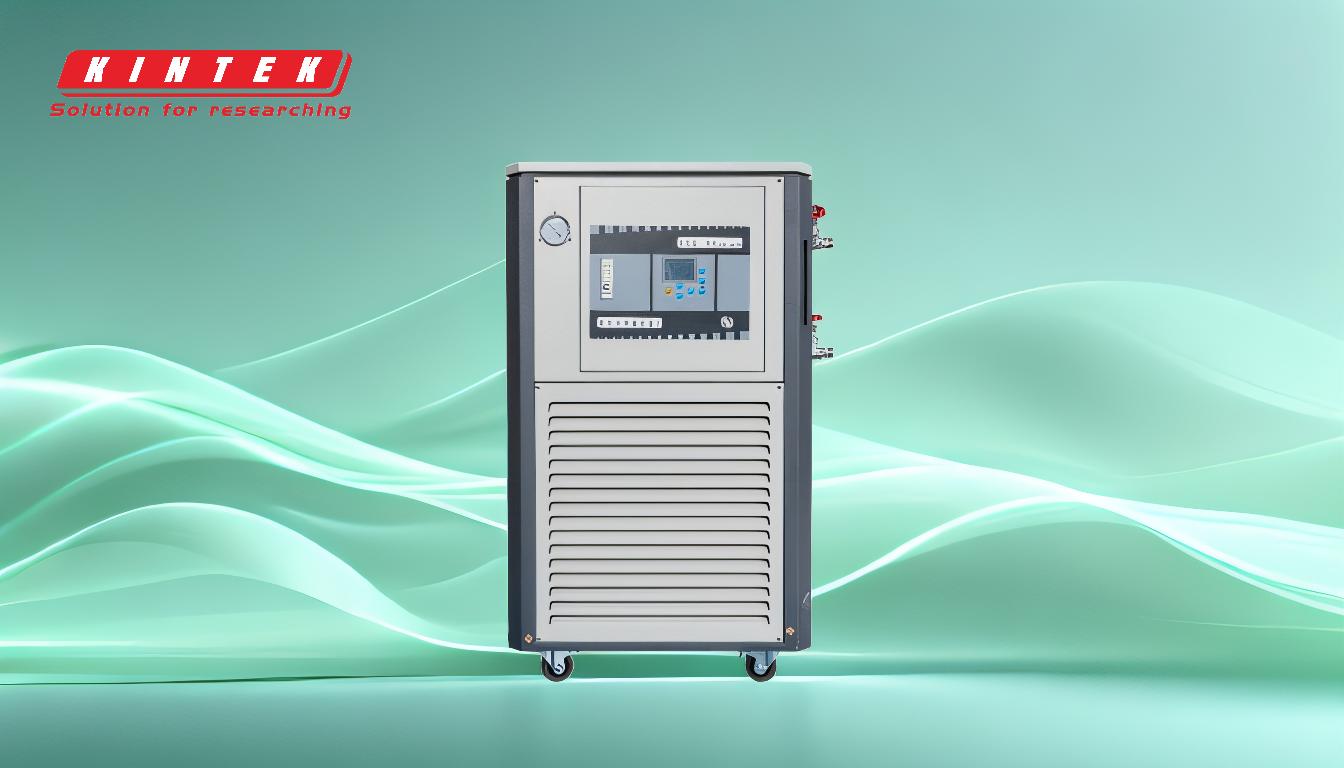
-
How Induction Coils Work:
- Induction coils are made of conductive materials like copper.
- When an electrical current flows through the coil, it generates a magnetic field around it.
- This magnetic field transfers energy to the metal inside the crucible, heating it to the desired temperature.
-
Melting Steel with Induction Coils:
- Steel has a melting point of approximately 1370°C (2500°F).
- The energy from the induction coil's magnetic field can heat steel to this temperature, allowing it to melt.
- The process is efficient and widely used in industrial settings for melting metals, including steel.
-
Factors Affecting the Melting Process:
- Coil Design: The design of the coil, including its material and shape, influences the strength and effectiveness of the magnetic field.
- Electrical Current: The amount of current flowing through the coil determines the intensity of the magnetic field and, consequently, the heating capability.
- Crucible Design: The crucible must be designed to withstand high temperatures and efficiently transfer heat to the metal.
-
Advantages of Induction Melting:
- Precision: Induction furnaces allow for precise control over the heating process, ensuring consistent results.
- Energy Efficiency: The direct transfer of energy from the coil to the metal minimizes energy loss, making the process more efficient compared to traditional melting methods.
- Cleanliness: Induction melting produces fewer contaminants, as it does not involve combustion or direct contact with heating elements.
-
Applications of Induction Melting:
- Induction melting is commonly used in industries such as metallurgy, automotive, and aerospace for melting and casting metals.
- It is particularly useful for melting high-temperature metals like steel, which require precise temperature control and high energy input.
In summary, an induction coil is fully capable of melting steel, thanks to its ability to generate a strong magnetic field that efficiently transfers energy to the metal. This method is not only effective but also offers significant advantages in terms of precision, energy efficiency, and cleanliness, making it a preferred choice in various industrial applications.
Summary Table:
Key Aspect | Details |
---|---|
How It Works | Induction coils generate a magnetic field to transfer energy and heat steel. |
Steel Melting Point | Approximately 1370°C (2500°F). |
Key Factors | Coil design, electrical current, and crucible design. |
Advantages | Precision, energy efficiency, and cleanliness. |
Applications | Metallurgy, automotive, aerospace, and more. |
Ready to explore induction melting solutions? Contact our experts today for tailored advice!