Yes, titanium can be PVD coated. PVD (Physical Vapor Deposition) is a versatile process that allows for the deposition of thin films on a wide range of materials, including titanium. The process involves vaporizing a target material in a vacuum chamber and depositing it onto the substrate, which in this case is titanium. This results in a thin, durable coating that enhances the properties of the titanium, such as wear resistance, hardness, and aesthetic appeal. The PVD process is carried out in a vacuum chamber at extremely low pressures, involving three key steps: evaporation, transportation, and condensation.
Key Points Explained:
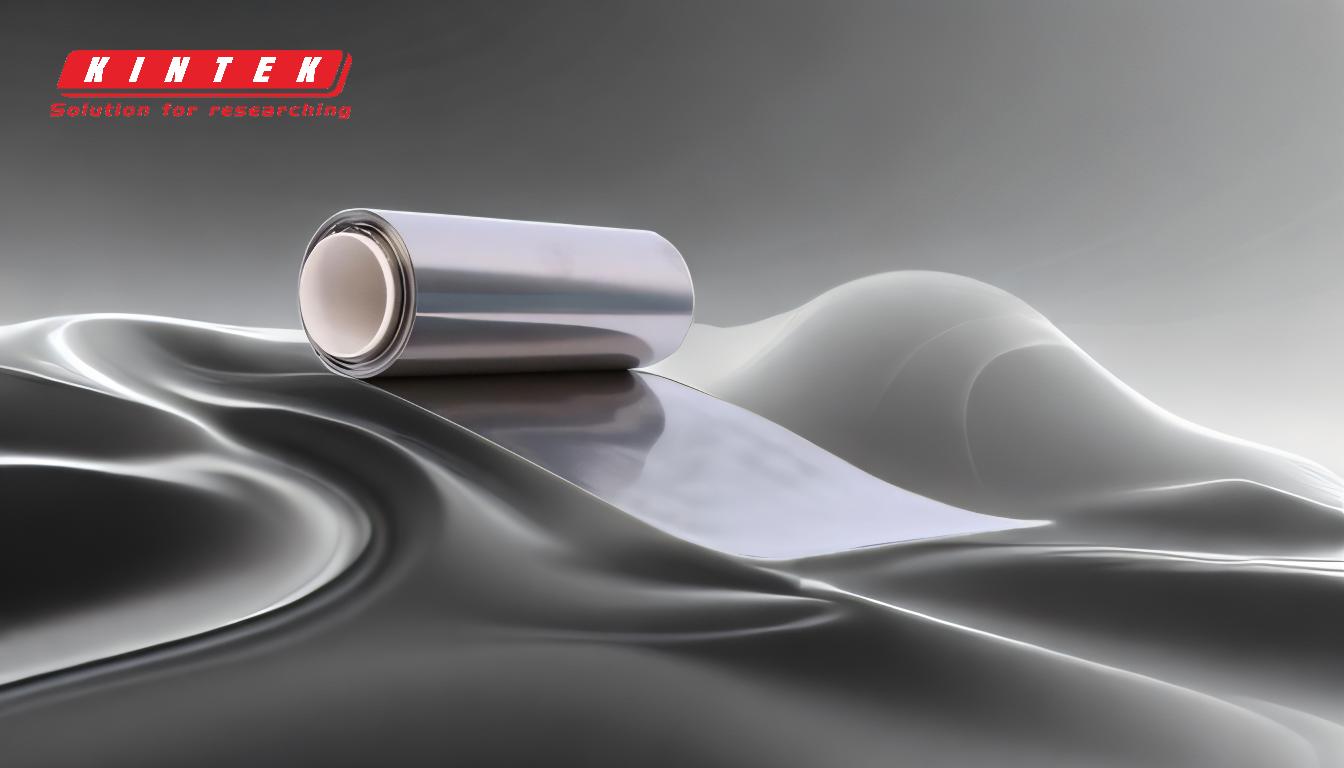
-
PVD Coating Process Overview:
- PVD coating involves depositing thin films of material onto a substrate through a process called Physical Vapor Deposition.
- The process is carried out in a vacuum chamber at extremely low pressures, typically ranging from 10-3 to 10-9 Torr.
- The component to be coated, such as titanium, is placed in front of a high-purity target source in a plasma environment.
-
Steps Involved in PVD Coating:
- Evaporation: The target material is heated until it vaporizes. This is the first step where the material is removed from the target source.
- Transportation: The vaporized material is then transferred to the surface of the component (titanium in this case).
- Condensation: The vapor condenses on the component surface, forming a thin film through nucleation and growth.
-
Benefits of PVD Coating on Titanium:
- Improved Wear Resistance: The thin film deposited through PVD enhances the wear resistance of titanium, making it more durable.
- Increased Hardness: The coating increases the surface hardness of titanium, which is beneficial for applications requiring high strength.
- Enhanced Aesthetic Appearance: PVD coatings can also improve the visual appeal of titanium, offering a variety of colors and finishes.
-
Materials Suitable for PVD Coating:
- While stainless steel and titanium are the most typical materials used in PVD coating, the process is versatile and can be applied to a wide range of materials, including chrome-plated brass and other types of steel.
-
Applications of PVD Coated Titanium:
- PVD coated titanium is used in various industries, including aerospace, medical devices, and consumer electronics, where enhanced durability and aesthetic properties are required.
In summary, titanium can indeed be PVD coated, and the process offers significant benefits in terms of durability, hardness, and appearance. The PVD coating process is well-suited for titanium, making it a valuable technique for enhancing the properties of this versatile material.
Summary Table:
Key Aspect | Details |
---|---|
PVD Coating Process | Physical Vapor Deposition in a vacuum chamber at 10-3 to 10-9 Torr. |
Steps | Evaporation, Transportation, Condensation. |
Benefits | Improved wear resistance, increased hardness, enhanced aesthetic appeal. |
Materials Suitable | Titanium, stainless steel, chrome-plated brass, and other steels. |
Applications | Aerospace, medical devices, consumer electronics. |
Discover how PVD coating can enhance your titanium products—contact our experts today!