Sintering time significantly affects the marginal fit of zirconia copings. Studies have shown that longer sintering times can lead to better densification and reduced shrinkage, which improves the marginal fit. However, excessive sintering times may cause over-sintering, leading to distortions and poor fit. Optimal sintering time is crucial to achieve a balance between material properties and dimensional accuracy, ensuring a precise marginal fit for zirconia restorations.
Key Points Explained:
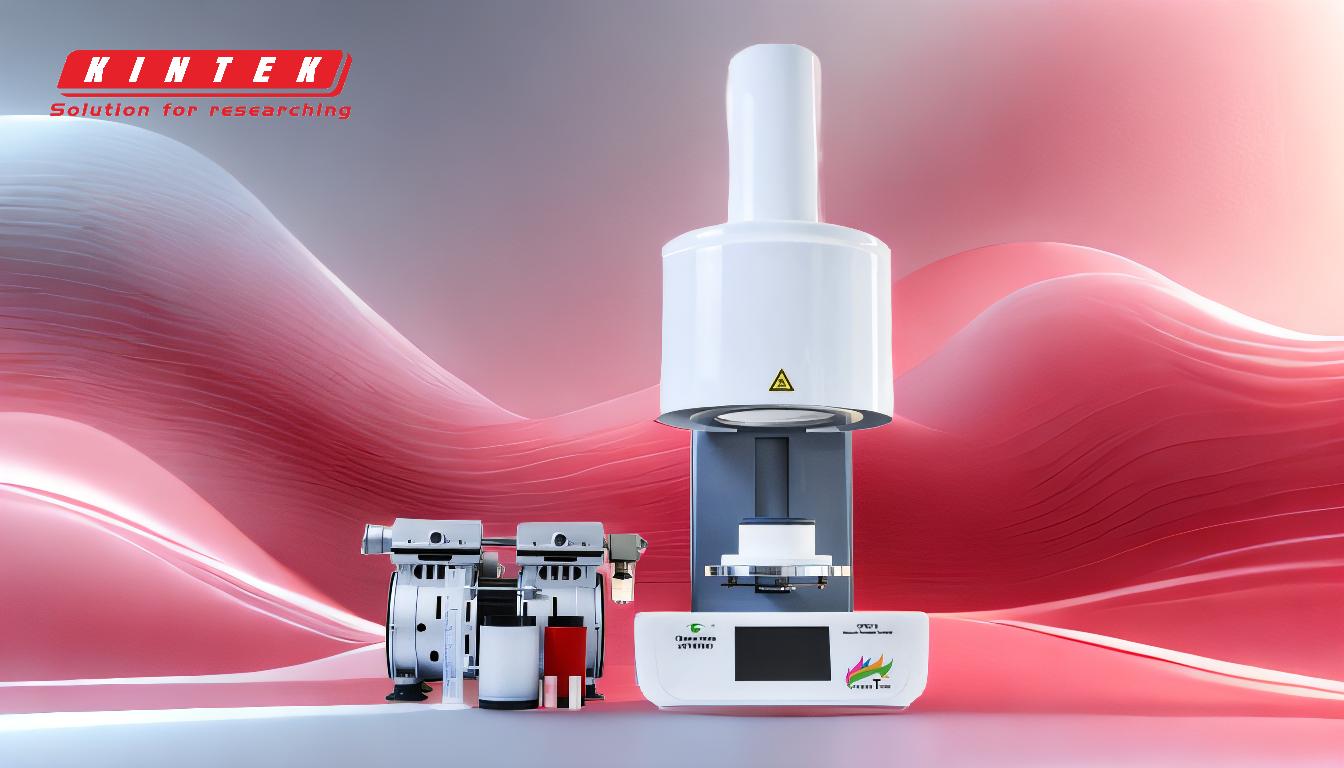
-
Sintering Time and Densification:
- Sintering is a critical process in the fabrication of zirconia copings, where the material is heated to a high temperature to achieve densification.
- Longer sintering times allow for more complete densification, reducing porosity and improving the mechanical properties of the zirconia.
- Improved densification leads to better marginal fit, as the material becomes more uniform and stable.
-
Shrinkage and Dimensional Accuracy:
- Zirconia undergoes shrinkage during sintering, which can affect the dimensional accuracy of the final restoration.
- Longer sintering times can help control and reduce shrinkage, leading to a more accurate fit of the zirconia coping to the prepared tooth.
- However, if sintering time is too long, it can cause excessive shrinkage or distortions, negatively impacting the marginal fit.
-
Over-Sintering and Distortions:
- Over-sintering occurs when the zirconia is sintered for too long or at too high a temperature, leading to grain growth and potential distortions.
- Distortions can cause the zirconia coping to deviate from the intended shape, resulting in a poor marginal fit.
- It is essential to optimize sintering time to avoid over-sintering while still achieving the desired material properties.
-
Optimal Sintering Time:
- The optimal sintering time for zirconia copings depends on the specific material and furnace used.
- Manufacturers typically provide recommended sintering protocols, which should be followed to achieve the best results.
- Clinicians and technicians should ensure that the sintering process is carefully controlled to maintain the balance between material strength and dimensional accuracy.
-
Clinical Implications:
- A precise marginal fit is crucial for the long-term success of zirconia restorations, as it helps prevent microleakage, secondary caries, and periodontal issues.
- Proper sintering time ensures that the zirconia coping fits accurately on the prepared tooth, reducing the need for adjustments and improving patient outcomes.
- Clinicians should work closely with dental laboratories to ensure that the sintering process is optimized for each case.
In summary, sintering time plays a vital role in determining the marginal fit of zirconia copings. While longer sintering times can improve densification and reduce shrinkage, excessive sintering can lead to distortions and poor fit. Therefore, it is essential to follow recommended sintering protocols to achieve the best balance between material properties and dimensional accuracy, ensuring a precise and durable restoration.
Summary Table:
Factor | Impact on Marginal Fit |
---|---|
Sintering Time | Longer times improve densification and reduce shrinkage, enhancing fit. |
Over-Sintering | Excessive time causes distortions, leading to poor fit. |
Optimal Sintering Time | Follow manufacturer protocols to balance material properties and dimensional accuracy. |
Clinical Implications | Precise fit prevents microleakage, secondary caries, and improves patient outcomes. |
Ensure your zirconia restorations achieve the perfect fit—contact our experts today for optimized sintering solutions!