PVD (Physical Vapor Deposition) coating is a versatile and advanced process that not only enhances the durability and functionality of materials but also allows for a wide range of color options. By vaporizing metals like titanium, zirconium, and chromium in a vacuum and reacting them with gases such as nitrogen, PVD coatings can produce thin, durable layers with specific colors. The color of the coating is determined by factors like the type of metal used, the reactive gas, and the process conditions (time, heat, etc.). This process enables the recreation of expensive metal finishes like gold, rose gold, and gunmetal, while also offering resistance to discoloration, corrosion, and wear. Thus, PVD coating does change color, and the resulting colors are highly customizable and durable.
Key Points Explained:
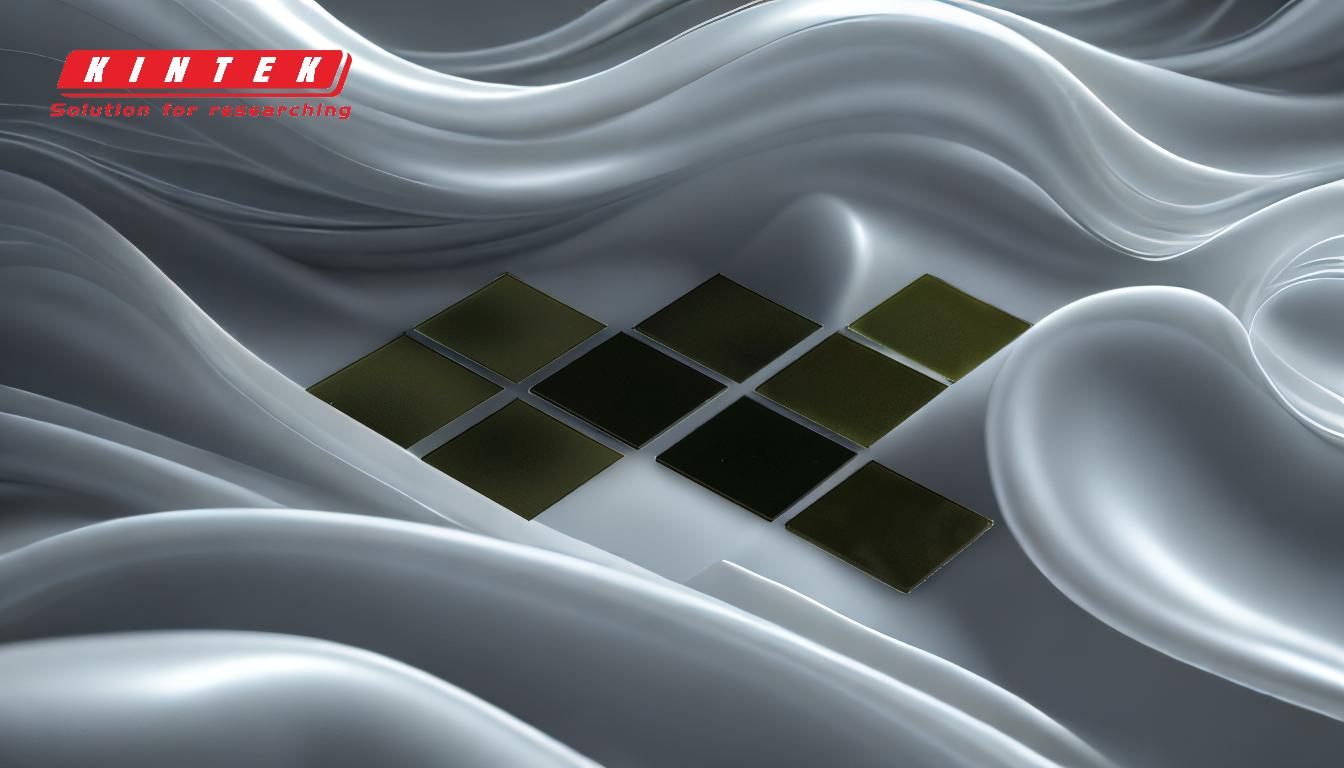
-
How PVD Coating Works:
- PVD coating involves vaporizing metals like titanium, zirconium, or chromium in a vacuum chamber.
- The vaporized metal ions react with a reactive gas (usually nitrogen) to form a thin, durable coating.
- This process alters the surface properties of the material, making it harder and more resistant to wear and corrosion.
-
Color Customization in PVD Coating:
- The color of the PVD coating is determined by the combination of the sacrificial metal, reactive gas, and process conditions (time, heat, etc.).
- For example, titanium combined with nitrogen can produce colors ranging from gold to rose gold, while other combinations can create black or gunmetal finishes.
- This allows for precise control over the final appearance, making it possible to replicate the look of expensive metals like gold, brass, and bronze.
-
Durability and Resistance of PVD Colors:
- PVD coatings are highly durable, being four times harder than chrome, which makes them resistant to scratches, corrosion, and wear.
- The colors produced through PVD are resistant to discoloration, pitting, and fading, even in harsh environments like coastal areas.
- This makes PVD-coated materials ideal for applications where both aesthetics and longevity are important, such as jewelry, watches, and architectural elements.
-
Applications of PVD Color Coatings:
- PVD coatings are widely used in industries like jewelry and watchmaking to create finishes like rose gold, black, and gunmetal.
- They are also used in architectural applications to preserve the vibrancy of colors in coastal properties, where exposure to salt and moisture can cause discoloration.
- The ability to recreate expensive metal finishes without the risk of patina makes PVD coatings a cost-effective and attractive option.
-
Advantages of PVD Over Other Coating Methods:
- Compared to CVD (Chemical Vapor Deposition), PVD coatings are more wear-resistant, have higher compressive stress, and can be deposited at lower temperatures.
- PVD coatings offer a wider range of color options and better resistance to environmental factors, making them superior for both functional and aesthetic purposes.
In summary, PVD coating not only changes the color of materials but does so in a highly customizable and durable manner. The process allows for the creation of a wide range of colors, from metallic finishes to darker tones, while ensuring that the coatings remain resistant to wear, corrosion, and discoloration. This makes PVD an excellent choice for applications where both appearance and durability are critical.
Summary Table:
Aspect | Details |
---|---|
Process | Vaporizes metals like titanium, zirconium, or chromium in a vacuum chamber. |
Color Customization | Determined by metal type, reactive gas (e.g., nitrogen), and process conditions. |
Durability | 4x harder than chrome; resistant to scratches, corrosion, and discoloration. |
Applications | Jewelry, watches, architectural elements, and coastal properties. |
Advantages | Wider color range, superior wear resistance, and lower deposition temperatures compared to CVD. |
Transform your materials with durable, customizable PVD coatings—contact us today to learn more!