Pyrolysis is a thermal decomposition process that breaks down organic materials in the absence of oxygen. While pyrolysis can occur without a catalyst, the use of catalysts can significantly enhance the process by promoting desirable chemical reactions, improving product quality, and increasing the yield of valuable biofuels and chemicals. Catalysts like biochar-based catalysts are particularly effective in deoxygenation and upgrading the quality of the final product, making it more suitable for use as drop-in fuels. The basicity of the catalyst also plays a crucial role in determining its efficiency.
Key Points Explained:
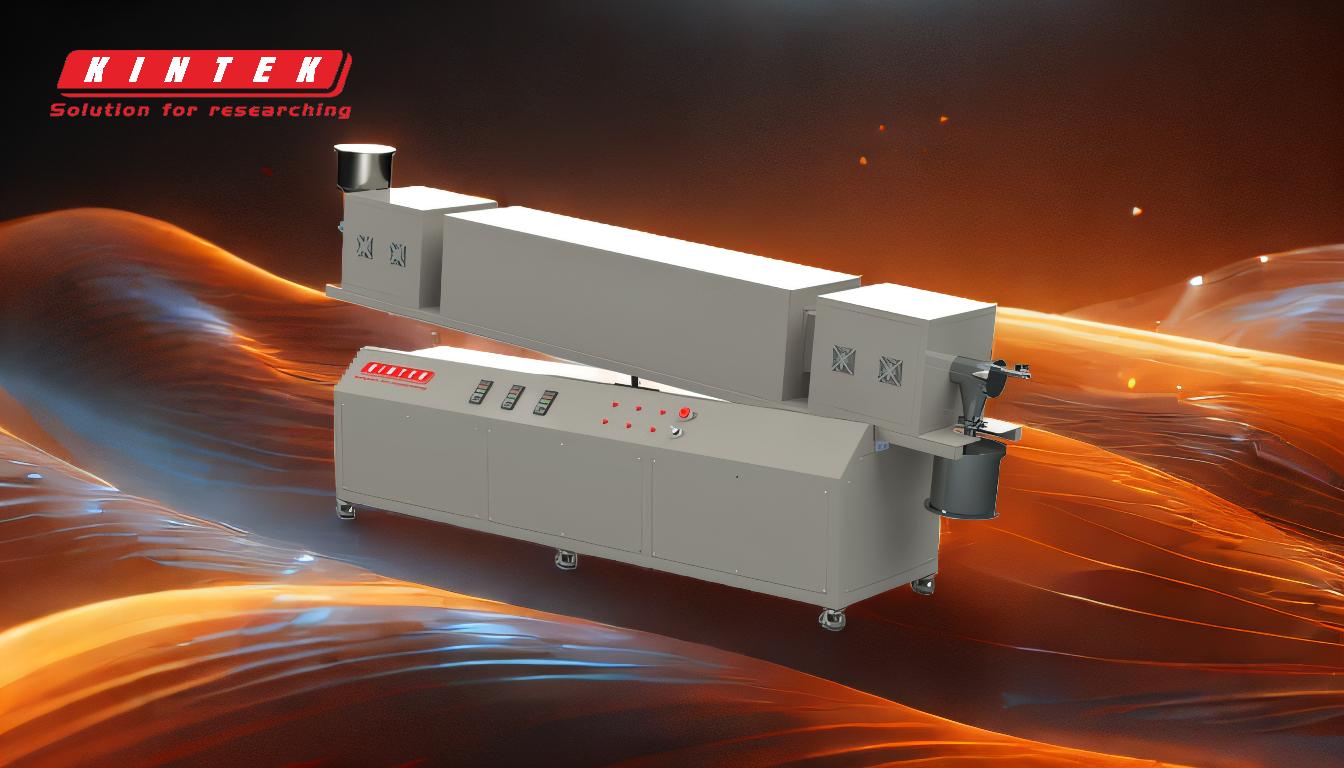
-
Pyrolysis Without a Catalyst:
- Pyrolysis can occur without a catalyst, relying solely on thermal decomposition.
- The process breaks down organic materials into simpler compounds like gases, liquids (bio-oil), and solids (char).
- However, the products may require further refining to be useful, as they often contain a mix of oxygenated compounds and other impurities.
-
Role of Catalysts in Pyrolysis:
- Catalysts are used to promote specific chemical reactions during pyrolysis, enhancing the overall efficiency and quality of the process.
- They help in deoxygenation, reducing the oxygen content in the bio-oil, which improves its stability and compatibility with existing hydrocarbon fuels.
- Catalysts can also increase the yield of valuable biofuels and chemicals by steering the reaction pathways toward more desirable products.
-
Types of Catalysts Used:
- Biochar-Based Catalysts: These are derived from the char produced during pyrolysis and are effective in promoting desirable reactions.
- Basic Catalysts: Catalysts with higher basicity are more efficient due to their strong deoxygenation capacity. This is crucial for producing high-quality biofuels.
-
Benefits of Using Catalysts:
- Improved Product Quality: Catalysts help produce a higher quality bio-oil that can be more easily upgraded to drop-in fuels, which are compatible with current hydrocarbon fuels.
- Increased Yield: The use of catalysts can increase the yield of valuable products, making the process more economically viable.
- Enhanced Reaction Control: Catalysts allow for better control over the chemical reactions, leading to more predictable and desirable outcomes.
-
Applications in Plastic Pyrolysis:
- In the context of plastic pyrolysis, catalysts are used to convert plastic waste into oil. This not only helps in waste management but also produces a valuable resource.
- The catalytic process ensures that the resulting oil is of higher quality and can be used as a feedstock for further refining into fuels or chemicals.
-
Economic and Environmental Considerations:
- While the use of catalysts can increase the initial cost of the pyrolysis process, the improved product quality and yield can offset these costs.
- Catalytic pyrolysis is also more environmentally friendly, as it reduces the need for further refining processes, which can be energy-intensive and polluting.
In summary, while pyrolysis does not strictly require a catalyst, the use of catalysts significantly enhances the process by improving product quality, increasing yield, and making the process more economically and environmentally sustainable.
Summary Table:
Aspect | Without Catalyst | With Catalyst |
---|---|---|
Process Efficiency | Relies solely on thermal decomposition | Enhances chemical reactions |
Product Quality | Bio-oil may require further refining | Produces high-quality, stable bio-oil |
Yield | Lower yield of valuable products | Increases yield of biofuels and chemicals |
Environmental Impact | May require energy-intensive refining | Reduces need for further refining |
Economic Viability | Less cost-effective due to lower yield | More economically viable due to higher yield |
Interested in optimizing your pyrolysis process? Contact our experts today to learn more!