Cleaning a sputter coater is a critical maintenance task to ensure its optimal performance and longevity. The process involves using appropriate cleaning agents and techniques to remove contaminants without damaging the equipment. Isopropyl alcohol is often recommended for cleaning metal surfaces due to its effectiveness and lower health and safety risks compared to acetone. Additionally, maintaining the purity and uniformity of sputter coater targets is essential for achieving high-quality sputtering results. Below, we’ll explore the key steps and considerations for cleaning a sputter coater in detail.
Key Points Explained:
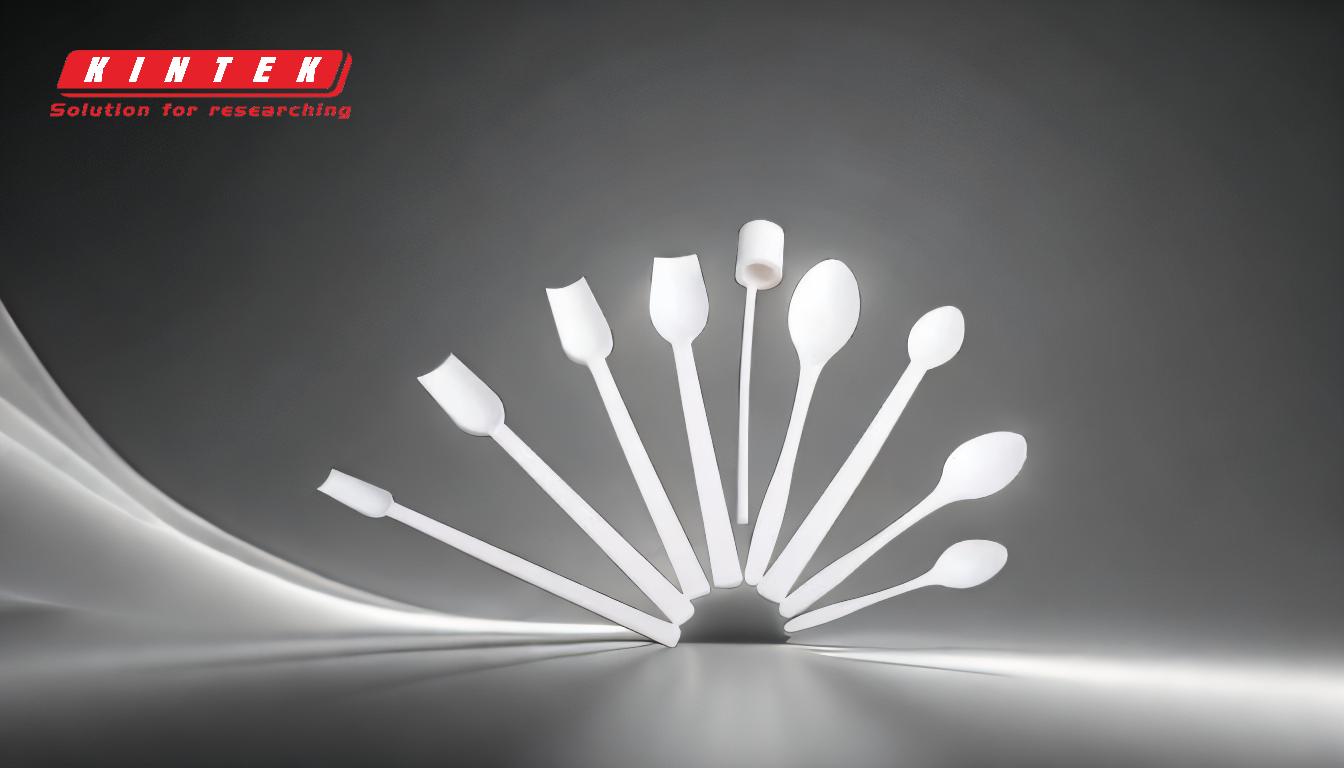
-
Use Isopropyl Alcohol for Cleaning Metal Surfaces
- Isopropyl alcohol is a preferred cleaning agent for sputter coaters because it evaporates quickly, leaves minimal residue, and poses fewer health and safety risks compared to acetone.
- Acetone, while effective, takes longer to outgas and can compromise vacuum performance if not fully evaporated.
- When cleaning, apply isopropyl alcohol using a lint-free cloth or swab to avoid leaving fibers or particles on the surface.
-
Clean the Sputter Coater Chamber and Components
- Regularly clean the chamber walls, electrodes, and other internal components to remove accumulated debris or sputtered material.
- Use a vacuum-compatible cleaner or isopropyl alcohol to wipe down surfaces, ensuring no residue is left behind.
- Pay special attention to areas near the target and substrate holders, as these are prone to contamination.
-
Handle Sputter Coater Targets with Care
- Sputter coater targets have stringent requirements for purity, size, and grain size uniformity. Any contamination or damage can affect the quality of the sputtered films.
- Avoid touching the target surface with bare hands, as oils and dirt can compromise its performance.
- If cleaning is necessary, use a gentle cleaning solution and follow the manufacturer’s guidelines to prevent damage.
-
Inspect and Replace Worn-Out Components
- Regularly inspect the sputter coater for signs of wear, such as eroded targets, damaged seals, or contaminated shields.
- Replace components as needed to maintain the coater’s performance and prevent contamination of the sputtered films.
-
Follow Safety Protocols During Cleaning
- Wear appropriate personal protective equipment (PPE), such as gloves and safety goggles, when handling cleaning agents.
- Work in a well-ventilated area or use a fume hood to avoid inhaling fumes from cleaning solvents.
- Dispose of used cleaning materials according to local regulations to minimize environmental impact.
-
Maintain a Clean Environment Around the Sputter Coater
- Keep the area around the sputter coater clean and free of dust or debris to prevent contamination during operation.
- Use lint-free wipes and cleanroom-grade materials when working near the equipment.
By following these steps and considerations, you can effectively clean and maintain your sputter coater, ensuring consistent performance and high-quality sputtering results. Regular maintenance and careful handling of components are key to extending the lifespan of your equipment and achieving optimal outcomes.
Summary Table:
Key Steps | Details |
---|---|
Use Isopropyl Alcohol | Effective, quick-evaporating, and safe for metal surfaces. |
Clean Chamber and Components | Remove debris with vacuum-compatible cleaners or isopropyl alcohol. |
Handle Targets Carefully | Avoid contamination; clean gently following manufacturer guidelines. |
Inspect and Replace Worn Components | Regularly check for wear and replace parts to maintain performance. |
Follow Safety Protocols | Use PPE, work in well-ventilated areas, and dispose of materials properly. |
Maintain a Clean Environment | Keep the area dust-free and use cleanroom-grade materials. |
Need expert advice on maintaining your sputter coater? Contact us today for personalized guidance!