Preventing a crucible from cracking during heating involves careful handling, proper storage, and controlled heating and cooling processes. Key strategies include avoiding thermal shock by gradually increasing and decreasing temperatures, ensuring the crucible is dry before use, and using appropriate handling tools and techniques. Additionally, placing insulation materials between the crucible and furnace base, and using separate crucibles for different metals, can prevent damage and contamination. Proper storage in a dry environment and pre-heating the crucible along with the metal are also essential to avoid cracking due to moisture or rapid temperature changes.
Key Points Explained:
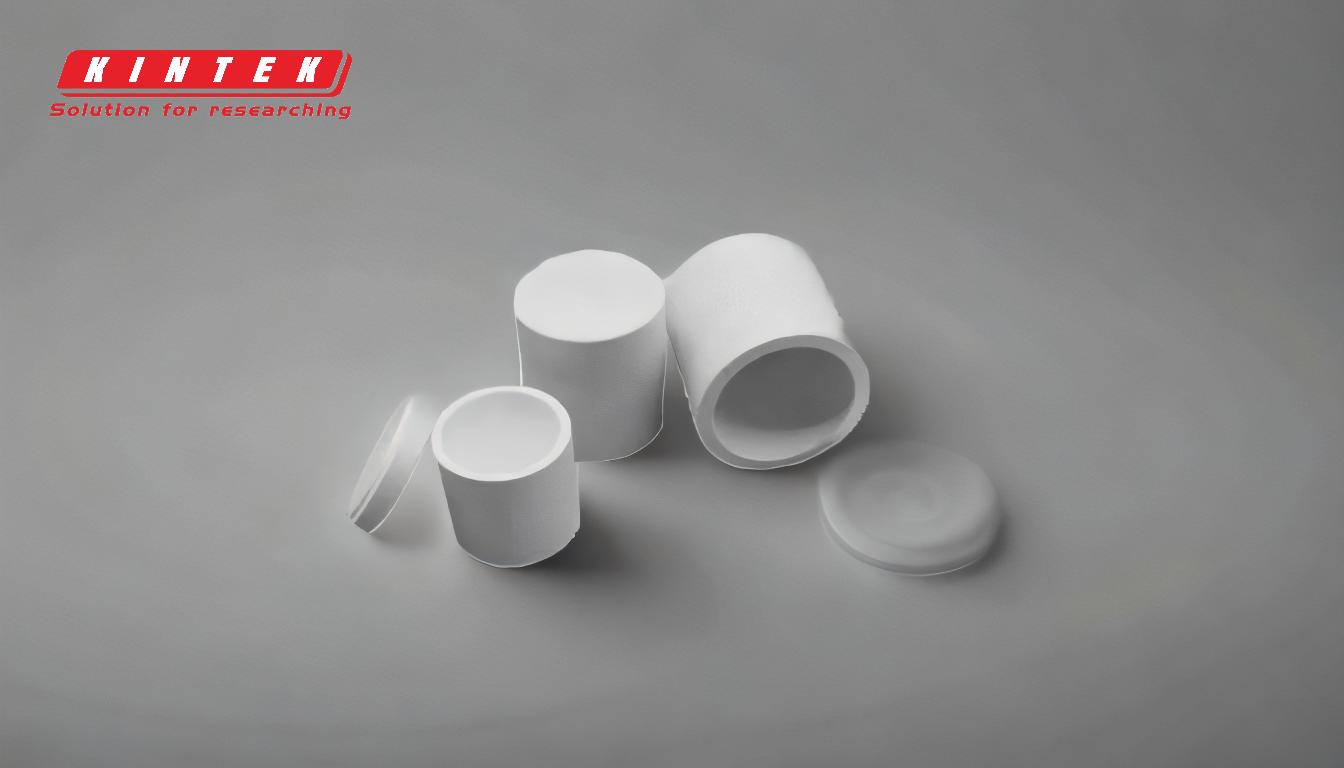
-
Gradual Heating and Cooling:
- Alumina crucibles are highly sensitive to thermal shock. To prevent cracking, it is crucial to heat the furnace chamber slowly, typically at a rate of 150°C/hour for the first 1-1.5 hours. This ensures even heating and minimizes stress on the crucible.
- Cooling should also be gradual, with the cooling rate often set to half of the heating rate. Rapid cooling can cause the crucible to contract too quickly, leading to cracks.
- Maintaining a hot crucible by consecutive heating of the furnace can also help reduce thermal stress.
-
Proper Handling Techniques:
- Crucibles should be handled with care using properly fitting tongs to avoid physical damage. Mishandling can lead to cracks or chips, especially when the crucible is hot.
- Before heating, placing a plate of cardboard or insulation material between the furnace base and the crucible can prevent bonding and reduce the risk of cracking due to uneven heating.
-
Moisture Control:
- Crucibles must be stored in a dry environment to prevent moisture absorption. Even a small amount of moisture can cause the crucible to crack when heated, as the moisture rapidly turns to steam and expands.
- Pre-heating the crucible along with the metal to be melted as the furnace heats up can help eliminate any residual moisture and reduce the risk of cracking.
-
Avoiding Contamination:
- Using separate crucibles for different metals is essential to prevent contamination. Residual metals from previous uses can react with new materials, leading to damage or cracking.
- Crucibles should be completely emptied after each use to prevent damage from expanding metal, which can exert pressure on the crucible walls during heating.
-
Proper Placement and Support:
- To avoid crushing the crucible, place the crucible cover on the sintered base first, and then place the crucible on the cover. This ensures proper alignment and reduces the risk of physical damage during the sintering process.
- Avoid placing heated crucibles on cold surfaces, as the sudden temperature difference can cause cracking. Instead, use insulation materials as support to maintain a consistent temperature.
By following these guidelines, you can significantly reduce the risk of crucible cracking during heating, ensuring the longevity and effectiveness of your crucibles in high-temperature applications.
Summary Table:
Key Strategies | Details |
---|---|
Gradual Heating and Cooling | Heat at 150°C/hour for 1-1.5 hours; cool at half the heating rate. |
Proper Handling Techniques | Use fitting tongs; place insulation between crucible and furnace base. |
Moisture Control | Store in a dry environment; pre-heat crucible with metal to eliminate moisture. |
Avoiding Contamination | Use separate crucibles for different metals; empty crucibles after each use. |
Proper Placement and Support | Place cover on base first; avoid cold surfaces; use insulation for support. |
Ensure your crucibles last longer—contact our experts today for personalized advice!