Silicon carbide (SiC) is a versatile material with exceptional properties, making it suitable for a wide range of applications. The processing of silicon carbide involves several steps, including powder preparation, shaping, sintering, and post-processing. The material's high density, hardness, and thermal stability allow for precise dimensional control and minimal sintering after use. Silicon carbide ceramics are manufactured by mixing SiC powder with sintering additives and heating them at high temperatures, typically between 2000°C to 2600°C. This process results in extremely dense products that can be shaped using methods like casting and dry pressing. Additionally, advanced techniques such as chemical vapor deposition (CVD) are used to grow high-quality SiC crystals for electronics. The material's excellent mechanical, thermal, and chemical properties make it ideal for applications in traditional industries and high-tech fields like semiconductors, nuclear energy, and space technology.
Key Points Explained:
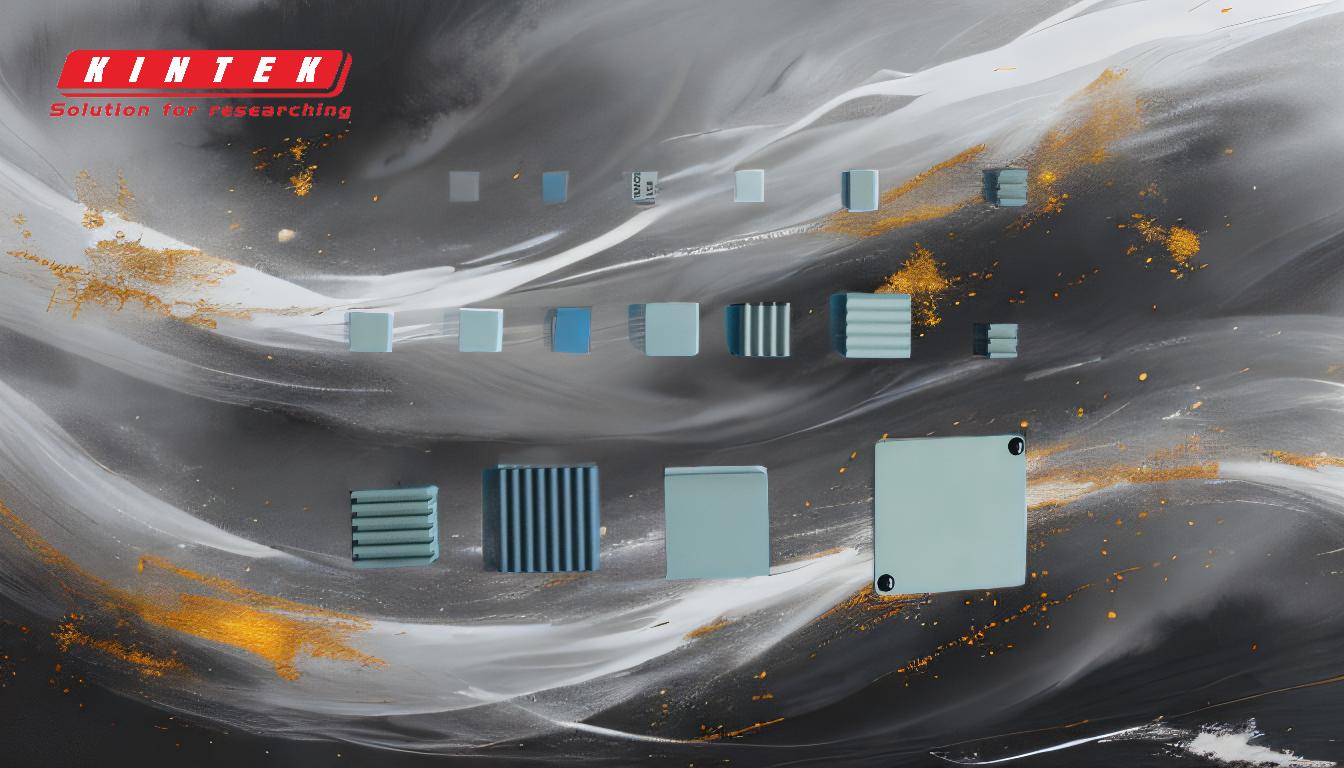
-
Raw Material Preparation:
- Silicon carbide is synthetically produced as a crystalline compound of silicon and carbon. The raw material is typically prepared in powder form, which is then mixed with non-oxide sintering additives to enhance its properties during the manufacturing process.
-
Shaping Methods:
- Silicon carbide ceramics can be shaped using various techniques, including casting and dry pressing. These methods allow for the creation of complex shapes, such as tubes, heating elements, and other components. The ability to form intricate designs is crucial for applications requiring tight dimensional control.
-
Sintering Process:
- The shaped silicon carbide products are sintered at extremely high temperatures, ranging from 2000°C to 2600°C. This high-temperature sintering process ensures the formation of dense and durable ceramic materials. The resulting products exhibit minimal sintering after use, maintaining their structural integrity over time.
-
Advanced Manufacturing Techniques:
- Chemical vapor deposition (CVD) is a key technique used to grow high-quality silicon carbide crystals, particularly for electronics applications. CVD allows for the production of thick, impurity-free SiC crystals, which are essential for manufacturing semiconductors and other electronic components. This method also enables the introduction of n-type and p-type dopants, enhancing the material's electrical properties.
-
Applications in High-Tech Fields:
- Silicon carbide ceramics are increasingly used in high-tech industries due to their excellent mechanical, thermal, and chemical properties. They are employed in semiconductors, nuclear energy, national defense, and space technology. The material's ability to withstand extreme conditions makes it ideal for these demanding applications.
-
Electric Discharge Machining (EDM):
- By controlling the resistivity of silicon carbide ceramics to below 100Ω·cm, the material becomes suitable for electric discharge machining (EDM). This process allows for fast and accurate processing of complex surfaces, making it beneficial for manufacturing large-sized or intricately shaped components.
-
Use in Traditional Industries:
- In the ceramic industry, silicon carbide is used for components such as receiving capsules and muffles, which are essential for the sintering of technical ceramics and porcelain. Its high thermal conductivity and resistance to wear make it an ideal material for these applications.
-
Properties and Benefits:
- Silicon carbide ceramics are known for their exceptional hardness, thermal stability, and chemical resistance. These properties make them suitable for a wide range of applications, from traditional industrial uses to cutting-edge technologies. The material's ability to maintain dimensional stability under extreme conditions is particularly valuable in high-performance applications.
By understanding these key points, purchasers of equipment and consumables can make informed decisions about the use of silicon carbide ceramic in their specific applications. The material's versatility and superior properties ensure its continued relevance across various industries.
Summary Table:
Step | Description |
---|---|
Raw Material Preparation | SiC powder is mixed with sintering additives to enhance properties. |
Shaping Methods | Techniques like casting and dry pressing are used to create complex shapes. |
Sintering Process | Products are sintered at 2000°C–2600°C for dense, durable ceramics. |
Advanced Techniques | CVD is used to grow high-quality SiC crystals for electronics applications. |
Applications | Used in semiconductors, nuclear energy, space tech, and traditional industries. |
Discover how silicon carbide can revolutionize your industry—contact us today for expert guidance!