A flat die pellet mill is a machine designed to compress raw materials into dense pellets, commonly used for biomass, animal feed, and other materials. It operates by forcing feedstock through holes in a flat die using a press roller, creating pellets under high pressure and temperature. The process relies on the plasticization of lignin in biomass, which acts as a natural binder. The mill is compact, portable, and easy to operate, making it ideal for small-scale production. Key components include the flat die, press roller, feeder, and power source. The mill's design allows for quick maintenance, observation of the pelletizing process, and the ability to produce pellets of varying diameters by changing the die.
Key Points Explained:
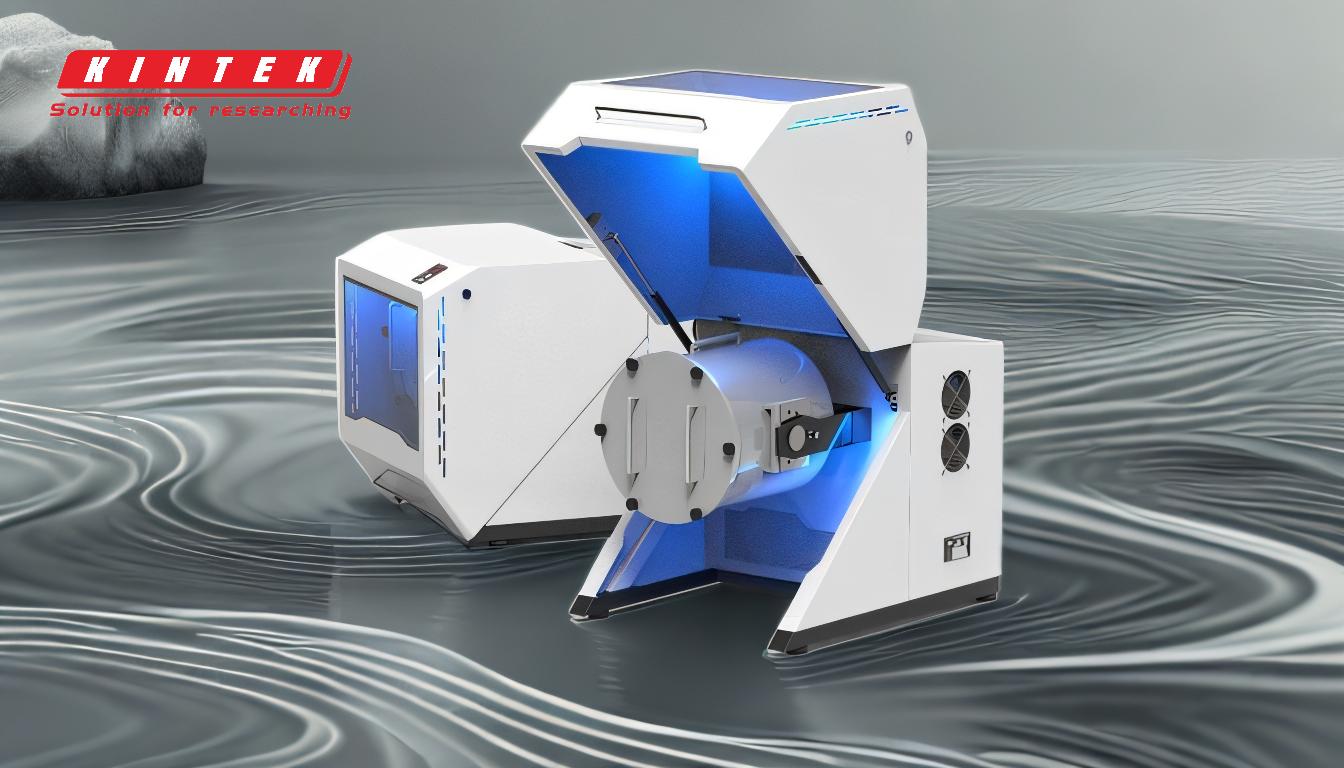
-
Main Components of a Flat Die Pellet Mill:
- The mill consists of several critical parts, including the press roller, flat die, feeder, gear bearings, and power source. Additional components include the feed hopper, upper box body, adjusting nut, pellet outlet, spindle box, gear box, transmission shaft, foundation, wheels, electric motor, and electric control cabinet. The power source can be an electric motor, diesel engine, or gasoline engine, providing flexibility in operation.
-
Pelletizing Process:
- Feedstock with appropriate size and moisture content is fed into the hopper. The press roller forces the material through the holes in the flat die under high pressure and temperature. This process causes the lignin in the biomass to plasticize, acting as a natural binder. The extruded pellets are hot and plastic initially but harden and gain mechanical resistance upon cooling.
-
Flat Die Design and Function:
- The flat die is a disc made of ductile cast iron with multiple holes. The thickness, hole size, and quantity of the die significantly impact production quality and capacity. The hole size determines the pellet diameter, and the mill can accommodate dies with different hole sizes to produce pellets of varying diameters.
-
Role of the Press Roller:
- The press roller, made of superior alloy steel, works in tandem with the flat die to compress the feedstock. The roller's hardness (55-60HRC) is slightly lower than the die to prolong its lifespan. A larger roller diameter increases the grabbing force on raw materials, allowing for a thicker material layer and improved production efficiency.
-
Advantages of Flat Die Pellet Mills:
- Flat die pellet mills are known for their simple structure, small size, light weight, and portability. They are easy to operate and maintain, with the pelletizing process being easily observable for quick fault detection. The flat dies, being wearing parts, can be used on both sides, extending their working life and reducing production costs. Additionally, these mills are easier to clean and maintain compared to other types.
-
Applications and Suitability:
- Due to their compact design and low capacity, flat die pellet mills are ideal for home use and small-scale production. They can handle a variety of raw materials with different characteristics, making them versatile for producing pellets from biomass, animal feed, and other materials.
-
Maintenance and Longevity:
- The flat die and press roller are the core components that require regular maintenance. The flat die, being a wearing part, needs periodic replacement, but its double-sided usability extends its lifespan. The roller's lower hardness compared to the die ensures it lasts longer, contributing to the mill's overall durability.
By understanding these key points, users can effectively operate and maintain a flat die pellet mill, ensuring optimal performance and longevity. The mill's simplicity, versatility, and ease of maintenance make it a valuable tool for small-scale pellet production.
Summary Table:
Key Aspect | Details |
---|---|
Main Components | Press roller, flat die, feeder, power source, feed hopper, gear box, etc. |
Pelletizing Process | Feedstock forced through die holes under high pressure and temperature. |
Flat Die Design | Ductile cast iron disc with holes; thickness and size affect pellet quality. |
Press Roller Role | Compresses feedstock; hardness slightly lower than die for durability. |
Advantages | Compact, portable, easy to operate, and maintain. |
Applications | Ideal for biomass, animal feed, and small-scale production. |
Maintenance | Flat die and press roller require regular maintenance for longevity. |
Discover how a flat die pellet mill can simplify your pellet production—contact our experts today for more information!