A hammer mill is a versatile machine used to grind, crush, or pulverize materials into smaller particles through repeated blows of hammers. It operates by feeding material into a chamber where rapidly rotating hammers strike the material, breaking it down into smaller pieces. The process involves several steps, including material feeding, impact grinding, particle size reduction, and discharge. The size of the final product is determined by the size of the screen or grate at the discharge end, which allows particles of a specific size to pass through while retaining larger particles for further grinding. Hammer mills are widely used in industries such as agriculture, food processing, and recycling.
Key Points Explained:
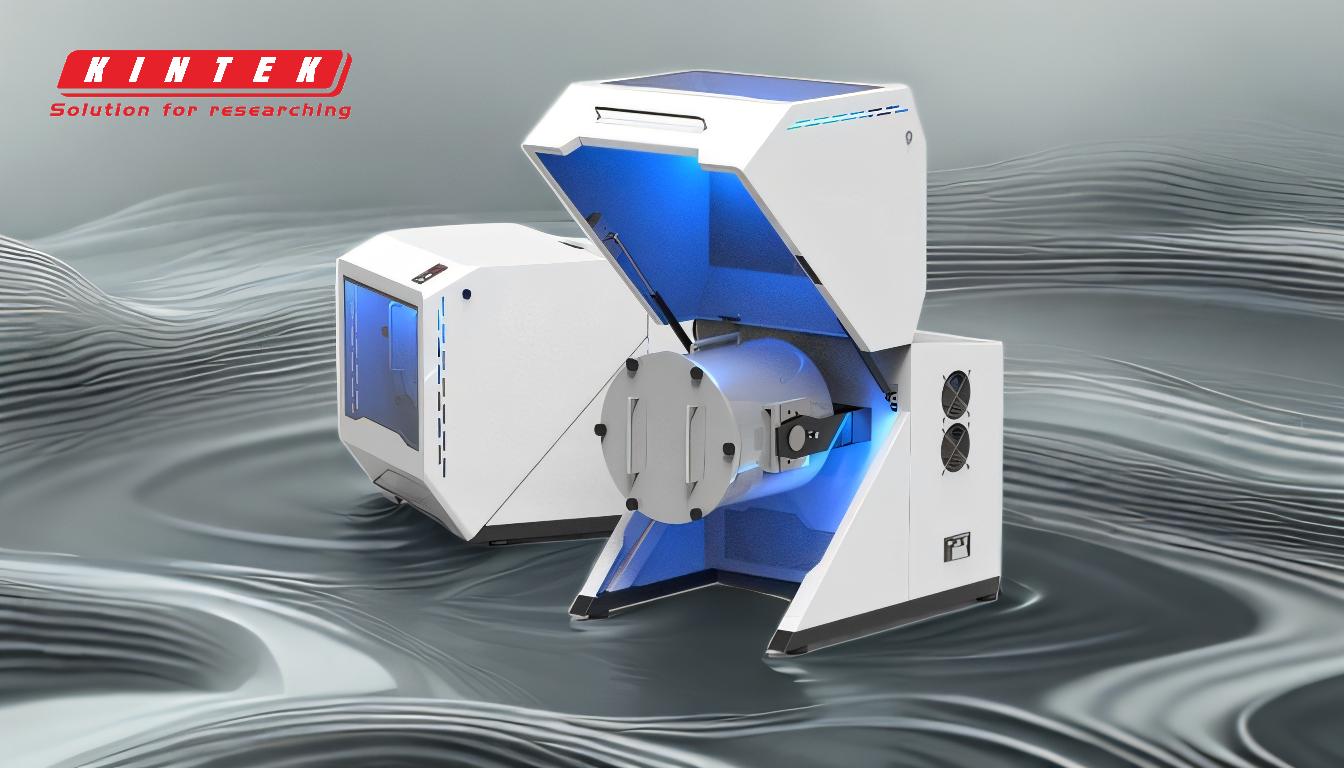
-
Material Feeding:
- The process begins with the introduction of raw material into the hammer mill's feed hopper. The material can be fed manually or automatically, depending on the design of the mill.
- The feed hopper directs the material into the grinding chamber, where it comes into contact with the rotating hammers.
-
Impact Grinding:
- Inside the grinding chamber, the material is subjected to repeated blows from the hammers, which are attached to a rotor that spins at high speed.
- The hammers strike the material with sufficient force to break it down into smaller particles. The impact force is generated by the kinetic energy of the rotating hammers.
-
Particle Size Reduction:
- As the material is struck by the hammers, it is repeatedly crushed and ground until it reaches the desired particle size.
- The size of the particles is controlled by the size of the openings in the screen or grate located at the bottom of the grinding chamber. Only particles smaller than the screen openings can pass through, while larger particles are retained for further grinding.
-
Discharge of Ground Material:
- Once the material has been reduced to the desired size, it passes through the screen or grate and is discharged from the hammer mill.
- The ground material is collected in a container or conveyed to the next stage of processing, depending on the application.
-
Hammers and Rotor:
- The hammers are the primary components responsible for the grinding action. They are typically made of hardened steel and are designed to withstand the high impact forces generated during operation.
- The rotor, which holds the hammers, rotates at high speed, typically between 1,800 and 3,600 revolutions per minute (RPM), depending on the size and design of the hammer mill.
-
Screen or Grate:
- The screen or grate is a critical component that determines the final particle size of the ground material. It is located at the bottom of the grinding chamber and has openings of a specific size.
- The size of the screen openings can be adjusted to produce particles of different sizes, making the hammer mill suitable for a wide range of applications.
-
Air Flow and Dust Collection:
- In some hammer mills, air flow is used to assist in the grinding process and to remove fine particles from the grinding chamber.
- Dust collection systems may be integrated into the hammer mill to capture and contain fine particles, ensuring a clean and safe working environment.
-
Applications of Hammer Mills:
- Hammer mills are used in various industries, including agriculture (for grinding grains and feed), food processing (for milling spices and other food products), and recycling (for shredding paper, plastics, and other materials).
- The versatility of hammer mills makes them suitable for processing a wide range of materials, from soft and fibrous to hard and brittle.
-
Maintenance and Safety:
- Regular maintenance of the hammer mill is essential to ensure optimal performance and longevity. This includes inspecting and replacing worn hammers, checking the screen for damage, and lubricating moving parts.
- Safety precautions should be taken when operating a hammer mill, including wearing protective gear and ensuring that the machine is properly guarded to prevent accidents.
-
Advantages of Hammer Mills:
- Hammer mills are known for their simplicity, reliability, and efficiency in reducing the size of various materials.
- They are capable of producing a uniform particle size distribution, making them ideal for applications where consistency is important.
- Hammer mills are also relatively easy to operate and maintain, making them a popular choice for many industries.
In summary, a hammer mill works by feeding material into a grinding chamber where it is struck by rapidly rotating hammers. The material is repeatedly crushed and ground until it reaches the desired particle size, at which point it is discharged through a screen or grate. The size of the final product is determined by the size of the screen openings, and the process can be adjusted to produce particles of different sizes. Hammer mills are widely used in various industries due to their versatility, efficiency, and ease of maintenance.
Summary Table:
Step | Description |
---|---|
Material Feeding | Raw material is introduced into the feed hopper, which directs it into the grinding chamber. |
Impact Grinding | Rotating hammers strike the material, breaking it down into smaller particles. |
Particle Size Reduction | Material is crushed and ground until it reaches the desired size, controlled by the screen/grate. |
Discharge | Ground material passes through the screen/grate and is collected or conveyed for further processing. |
Hammers and Rotor | High-speed rotor with hardened steel hammers generates impact force for grinding. |
Screen/Grate | Determines final particle size; adjustable for different applications. |
Air Flow & Dust Collection | Assists grinding and removes fine particles for a clean working environment. |
Applications | Used in agriculture, food processing, and recycling for versatile material grinding. |
Maintenance & Safety | Regular upkeep and safety measures ensure optimal performance and safe operation. |
Advantages | Simple, reliable, efficient, and capable of producing uniform particle sizes. |
Need a hammer mill for your industry? Contact us today to find the perfect solution!