Heating elements can fail due to a variety of reasons, primarily related to thermal stress, oxidation, contamination, and mechanical wear. The key causes include the formation of hot spots, oxidation due to intermittent operation, embrittlement from grain growth, and contamination or corrosion from the furnace environment. Additionally, faulty wiring and rapid heating/cooling cycles can exacerbate these issues, leading to premature failure. Understanding these mechanisms is crucial for selecting the right materials, operating conditions, and maintenance practices to extend the lifespan of heating elements.
Key Points Explained:
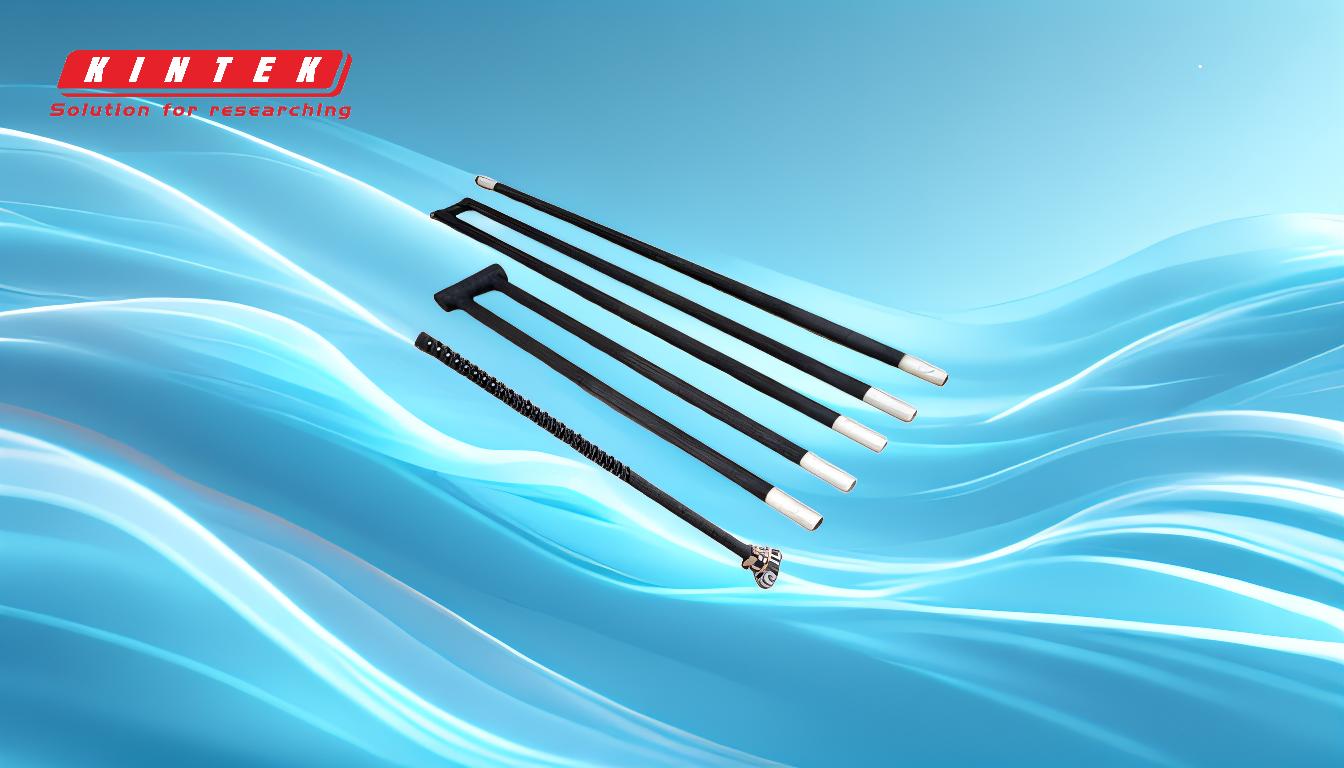
-
Formation of Hot Spots
- Cause: Hot spots occur when certain areas of the heating element reach higher temperatures than the rest, often due to localized oxidation or shielding by supports.
- Impact: These high-temperature areas can degrade faster, leading to uneven wear and eventual failure.
- Prevention: Ensure uniform heating and avoid physical obstructions that can cause shielding.
-
Oxidation and Intermittency of Operation
- Cause: Frequent heating and cooling cycles cause the oxide layer on the heating element to crack and flake off, exposing fresh metal to further oxidation.
- Impact: This continuous oxidation weakens the element over time, making it brittle and prone to failure.
- Prevention: Minimize rapid temperature changes and use materials with better oxidation resistance.
-
Embrittlement Due to Grain Growth
- Cause: At high temperatures, heating alloys containing iron can form large, brittle grains, reducing the element's mechanical strength.
- Impact: The element becomes more susceptible to cracking and breaking under stress.
- Prevention: Use alloys designed to resist grain growth or operate at lower temperatures if possible.
-
Contamination and Corrosion
- Cause: Exposure to gases, fumes, or other contaminants in the furnace environment can lead to dry corrosion.
- Impact: Contamination accelerates degradation, leading to cracks and eventual burnout.
- Prevention: Use corrosion-resistant materials and maintain a clean furnace environment.
-
Faulty Wiring
- Cause: Inadequate electrical power due to faulty wiring can cause uneven heating and burnout.
- Impact: The element may not receive consistent power, leading to localized overheating and failure.
- Prevention: Regularly inspect and maintain electrical connections to ensure proper power delivery.
-
Rapid Heating and Cooling Cycles
- Cause: Frequent and rapid temperature changes can cause thermal stress, leading to material fatigue.
- Impact: This stress can cause deformation, cracking, or even volatilization of the heating element.
- Prevention: Implement controlled heating and cooling rates to minimize thermal stress.
By understanding these key points, equipment purchasers can make informed decisions about material selection, operating conditions, and maintenance practices to maximize the lifespan and efficiency of heating elements.
Summary Table:
Cause of Failure | Impact | Prevention |
---|---|---|
Formation of Hot Spots | Uneven wear and eventual failure | Ensure uniform heating and avoid physical obstructions |
Oxidation and Intermittency | Weakening and brittleness over time | Minimize rapid temperature changes and use oxidation-resistant materials |
Embrittlement from Grain Growth | Susceptibility to cracking and breaking | Use alloys resistant to grain growth or operate at lower temperatures |
Contamination and Corrosion | Accelerated degradation, cracks, and burnout | Use corrosion-resistant materials and maintain a clean furnace environment |
Faulty Wiring | Localized overheating and failure | Regularly inspect and maintain electrical connections |
Rapid Heating/Cooling Cycles | Deformation, cracking, or volatilization of the element | Implement controlled heating and cooling rates to minimize thermal stress |
Need help selecting or maintaining heating elements? Contact our experts today for tailored solutions!