A rotary kiln is a cylindrical, inclined, and rotating furnace used to process materials at high temperatures, causing physical or chemical changes. It operates by feeding raw materials into the upper end, which then move downward due to gravity and rotation. Heat is generated through fuel combustion, either internally or externally, and transferred to the material. The kiln's design ensures uniform heating, mixing, and controlled retention time, enabling precise temperature profiles for specific reactions. Rotary kilns are widely used in industries like cement production, metallurgy, and chemical processing.
Key Points Explained:
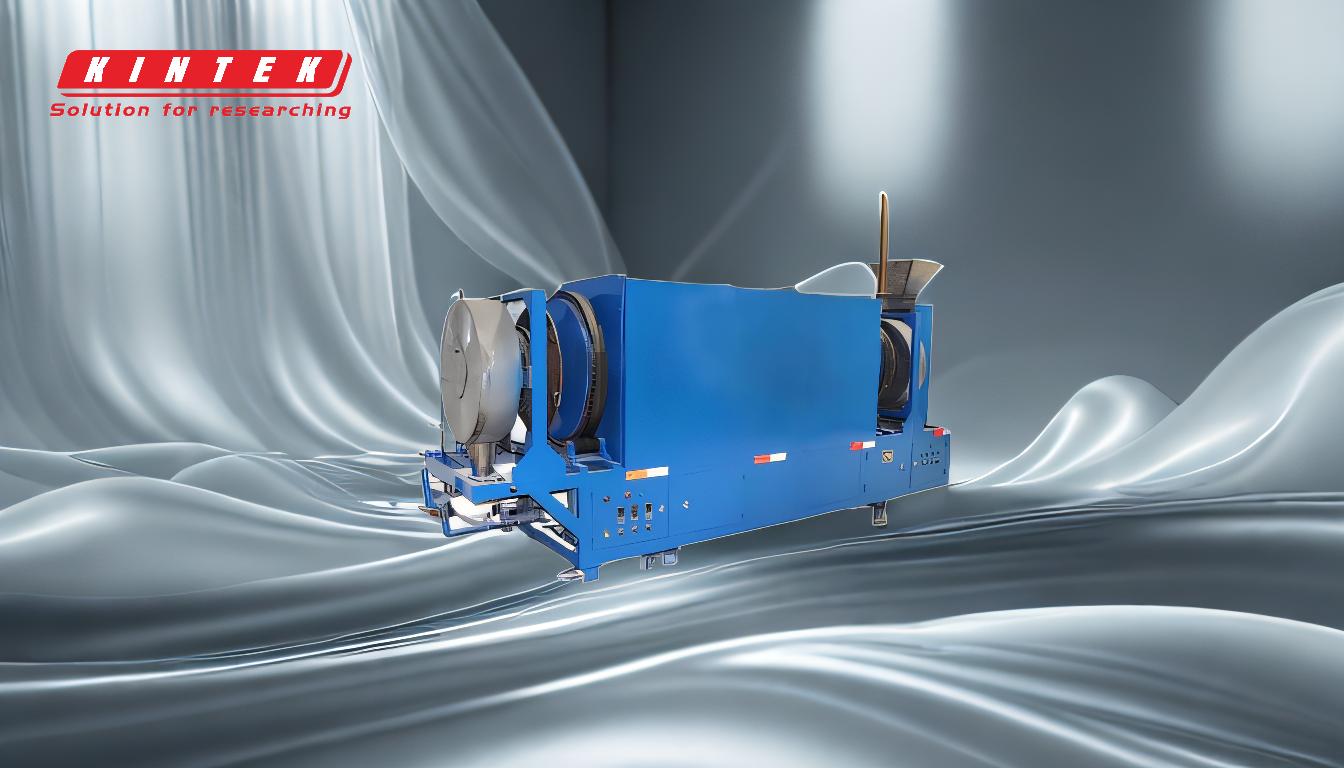
-
Structure and Design of a Rotary Kiln:
- A rotary kiln is a cylindrical vessel, slightly inclined from the horizontal, allowing materials to move downward by gravity.
- The cylinder rotates slowly about its longitudinal axis, ensuring continuous mixing and stirring of the material.
- The kiln is sealed at both ends with stationary breeching to control the internal atmosphere and temperature.
-
Material Movement and Processing:
- Raw materials are fed into the upper end of the kiln using a feeding device, such as a screw feeder.
- As the kiln rotates, the material moves toward the lower end, undergoing physical and chemical changes due to heat and mixing.
- The retention time and temperature are carefully controlled based on the desired reaction or transformation.
-
Heat Generation and Transfer:
- Heat is generated through fuel combustion, which can occur internally (via a burner-pipe) or externally (in a separate furnace).
- Common fuels include gas, oil, pulverized petroleum coke, or pulverized coal.
- Hot gases flow through the kiln, either in the same direction as the material (co-current) or in the opposite direction (counter-current), ensuring efficient heat transfer.
-
Temperature Control and Profiles:
- The kiln maintains precise temperature profiles, determined through chemical and thermal analyses, to achieve specific reactions or physical changes.
- The material is held at specialized temperatures for a predetermined amount of time, ensuring uniformity and consistency in the final product.
-
Industrial Applications:
- Rotary kilns are widely used in industries such as cement production, where they calcine limestone to produce clinker.
- They are also used in metallurgy for roasting ores, in chemical processing for thermal decomposition, and in waste treatment for incineration.
-
Advantages of Rotary Kilns:
- Continuous processing allows for high throughput and efficiency.
- Uniform heating and mixing ensure consistent product quality.
- The ability to handle a wide range of materials and temperatures makes rotary kilns versatile for various industrial applications.
-
Challenges and Considerations:
- Maintaining proper sealing and temperature control is critical to prevent energy loss and ensure safety.
- The design and operation of rotary kilns require careful consideration of material properties, reaction kinetics, and thermal dynamics.
- Regular maintenance is necessary to address wear and tear from high temperatures and rotational stresses.
In summary, a rotary kiln is a highly efficient and versatile thermal processing device that plays a crucial role in various industrial processes. Its design ensures uniform heating, mixing, and controlled retention time, enabling precise temperature profiles for specific reactions. Understanding its structure, operation, and applications is essential for optimizing performance and achieving desired outcomes in industrial settings.
Summary Table:
Aspect | Details |
---|---|
Structure | Cylindrical, inclined vessel with rotating design for material movement. |
Material Movement | Raw materials move downward by gravity and rotation, undergoing processing. |
Heat Generation | Fuel combustion (gas, oil, coal) for internal or external heat transfer. |
Temperature Control | Precise profiles for uniform heating and specific reactions. |
Applications | Cement production, metallurgy, chemical processing, waste treatment. |
Advantages | High throughput, uniform heating, versatility for various materials. |
Challenges | Sealing, temperature control, and regular maintenance required. |
Discover how a rotary kiln can optimize your industrial processes—contact us today!