An ion beam works by generating and directing a stream of ions (charged particles) toward a target material. The ions, typically monoenergetic and highly collimated, collide with the target, causing atoms or molecules to be ejected (sputtered) from the target surface. These sputtered particles then deposit onto a substrate, forming a thin film or coating. The process occurs in a vacuum chamber to minimize interference from air molecules and often uses inert gases like argon to generate ions. Ion beam systems can include additional features, such as a secondary ion source for ion-assisted deposition, to enhance film quality or modify surface properties. The precision and control of ion beams make them valuable in applications like thin-film deposition, surface modification, and material analysis.
Key Points Explained:
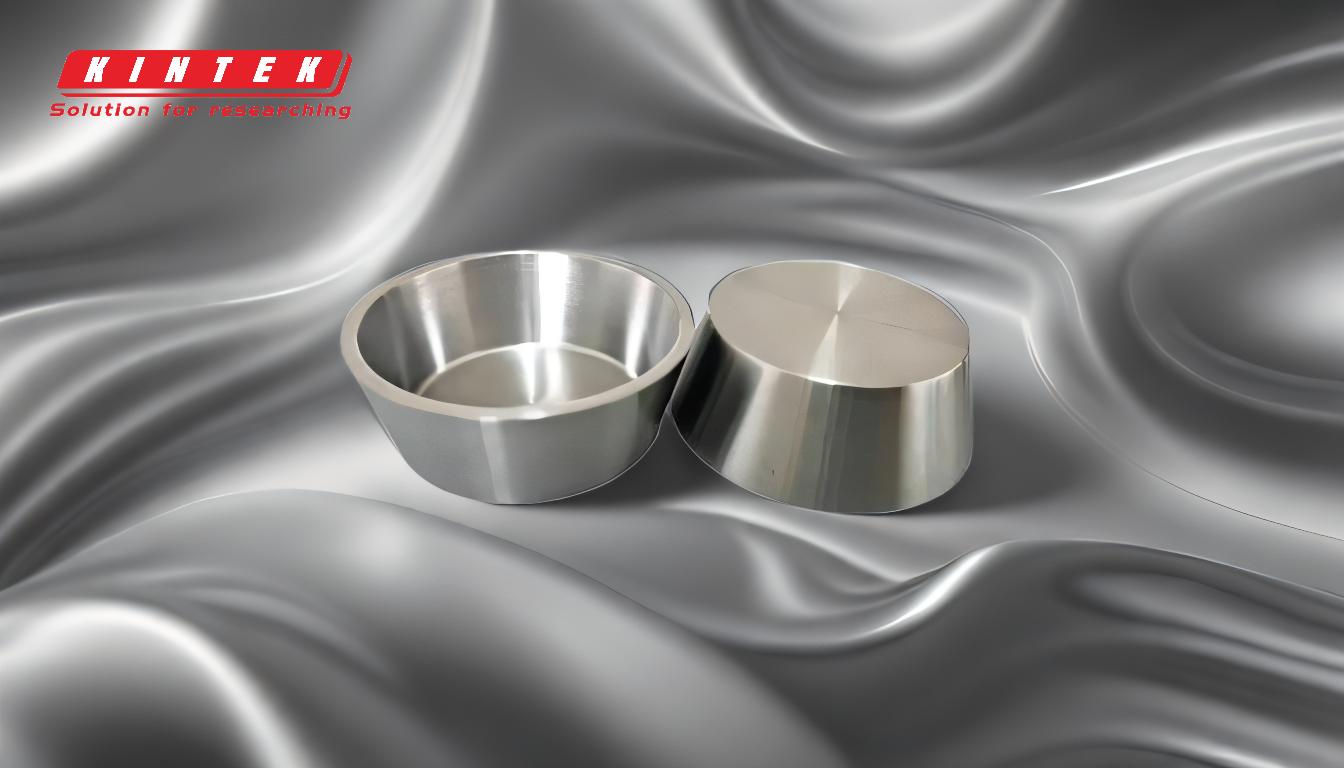
-
Ion Generation and Acceleration:
- An ion source generates ions, typically by ionizing inert gas atoms like argon.
- The ions are accelerated by an electric field, giving them high kinetic energy and making the beam monoenergetic (all ions have the same energy).
- This acceleration ensures the ions are highly collimated, meaning they travel in a focused, parallel beam.
-
Target Sputtering:
- The accelerated ions are directed toward a target material.
- When the ions collide with the target, they transfer their energy to the target atoms, causing them to be ejected (sputtered) from the surface.
- The sputtered material consists of atomic-sized particles, ensuring a fine and uniform deposition.
-
Deposition onto Substrate:
- The sputtered particles travel through the vacuum chamber and deposit onto a substrate.
- The vacuum environment prevents contamination and ensures the sputtered particles reach the substrate without interference from air molecules.
- The result is a thin, uniform film or coating on the substrate.
-
Ion-Assisted Deposition (Optional):
- Some ion beam systems include a secondary ion source directed at the substrate.
- This secondary beam can modify the growing film by enhancing adhesion, density, or other properties.
- Ion-assisted deposition is particularly useful for improving film quality in specialized applications.
-
Advantages of Ion Beam Systems:
- Precision: The monoenergetic and collimated nature of the ion beam allows for precise control over the deposition process.
- Uniformity: The fine, atomic-sized particles ensure a uniform and high-quality film.
- Versatility: Ion beam systems can be used for a wide range of materials and applications, including thin-film deposition, surface modification, and material analysis.
-
Applications of Ion Beam Technology:
- Thin-Film Deposition: Used in industries like semiconductors, optics, and coatings to create precise, high-quality films.
- Surface Modification: Ion beams can alter surface properties, such as hardness, wear resistance, or chemical reactivity.
- Material Analysis: Ion beams are used in techniques like secondary ion mass spectrometry (SIMS) to analyze material composition at the atomic level.
By understanding these key points, one can appreciate the precision and versatility of ion beam technology in various scientific and industrial applications.
Summary Table:
Key Aspect | Details |
---|---|
Ion Generation | Ions are generated by ionizing inert gases like argon. |
Acceleration | Electric fields accelerate ions, making them monoenergetic and collimated. |
Target Sputtering | Ions collide with the target, ejecting atomic particles for deposition. |
Deposition | Sputtered particles deposit onto a substrate in a vacuum environment. |
Ion-Assisted Deposition | Optional secondary ion source enhances film quality and properties. |
Applications | Thin-film deposition, surface modification, and material analysis. |
Unlock the potential of ion beam technology for your projects—contact us today!