Catalysts play a crucial role in pyrolysis by enhancing the efficiency and quality of the chemical reactions that break down plastic into oil and other valuable products. They promote specific reactions that lead to higher yields of desirable biofuels and chemicals, such as drop-in fuels, which are compatible with existing hydrocarbon fuels. Catalysts like biochar-based ones are particularly effective in improving the product quality and making the process more economically viable. By lowering the activation energy required for reactions, catalysts enable the pyrolysis process to occur at lower temperatures and with greater precision, resulting in a more controlled and efficient conversion of waste materials into useful resources.
Key Points Explained:
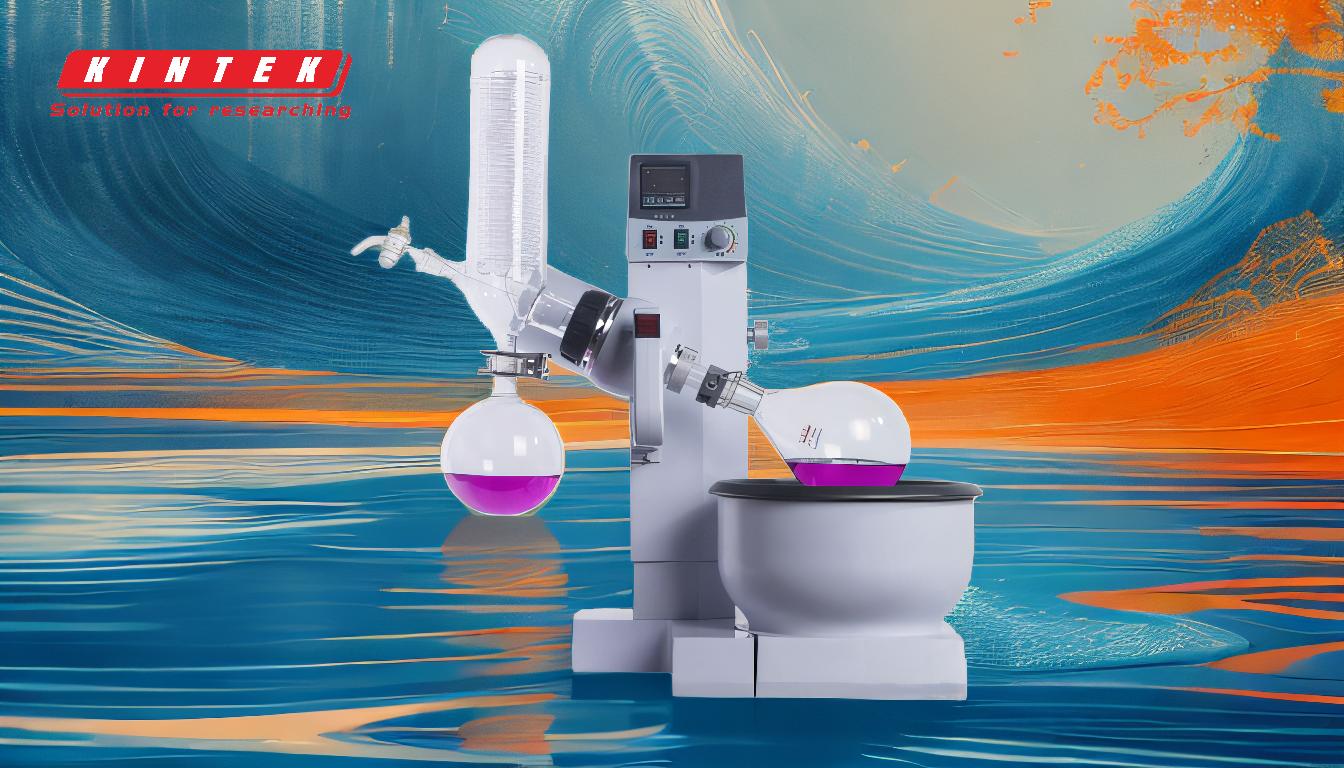
-
Role of Catalysts in Pyrolysis:
- Catalysts are substances that accelerate chemical reactions without being consumed in the process.
- In pyrolysis, catalysts promote the breakdown of plastic polymers into smaller hydrocarbon molecules, which can be converted into oil, biofuels, and other chemicals.
- They enable the process to occur at lower temperatures and with higher efficiency, reducing energy requirements.
-
Improving Product Quality:
- Catalysts enhance the quality of the pyrolysis products by promoting specific reactions that yield more valuable compounds.
- For example, they help produce drop-in fuels, which are chemically identical to conventional fuels and can be used directly in existing engines and infrastructure.
- This makes the pyrolysis process more economically viable and environmentally friendly.
-
Types of Catalysts:
- Biochar-Based Catalysts: These are derived from biomass and are known for their effectiveness in promoting desirable reactions during pyrolysis.
- Other catalysts may include zeolites, metal oxides, or acidic/basic catalysts, depending on the desired output and feedstock.
-
Mechanism of Action:
- Catalysts work by lowering the activation energy required for chemical reactions, making it easier for the plastic to break down into smaller molecules.
- They also help control the reaction pathways, ensuring that the products are more uniform and of higher quality.
-
Economic and Environmental Benefits:
- By improving the yield and quality of pyrolysis products, catalysts make the process more cost-effective and scalable.
- The ability to produce drop-in fuels reduces reliance on fossil fuels and contributes to a circular economy by recycling plastic waste.
-
Challenges and Considerations:
- Selecting the right catalyst is critical, as different catalysts may produce varying results depending on the feedstock and process conditions.
- Catalyst deactivation over time due to coking or contamination is a challenge that needs to be addressed for long-term viability.
By understanding how catalysts function in pyrolysis, stakeholders can optimize the process to maximize the production of valuable fuels and chemicals while minimizing environmental impact.
Summary Table:
Aspect | Details |
---|---|
Role of Catalysts | Accelerate reactions, reduce energy needs, and enable lower-temperature pyrolysis. |
Product Quality | Produce drop-in fuels and valuable chemicals, enhancing economic viability. |
Types of Catalysts | Biochar-based, zeolites, metal oxides, acidic/basic catalysts. |
Mechanism of Action | Lower activation energy, control reaction pathways for uniform products. |
Economic Benefits | Improve yield, reduce costs, and enable scalable plastic recycling. |
Environmental Benefits | Reduce fossil fuel reliance, promote circular economy. |
Challenges | Catalyst selection and deactivation due to coking or contamination. |
Optimize your pyrolysis process with the right catalysts—contact our experts today for tailored solutions!