Plasma-Enhanced Chemical Vapor Deposition (PECVD) is a thin-film deposition technique that combines chemical vapor deposition (CVD) with plasma to enable deposition at lower temperatures. The process involves placing a substrate in a reaction chamber, introducing reactant gases, and using plasma to decompose the gases into reactive species. These species then diffuse to the substrate surface, where they undergo chemical reactions to form a thin film. PECVD is widely used in industries such as semiconductors, photovoltaics, and optics due to its ability to deposit high-quality films at relatively low temperatures compared to traditional CVD.
Key Points Explained:
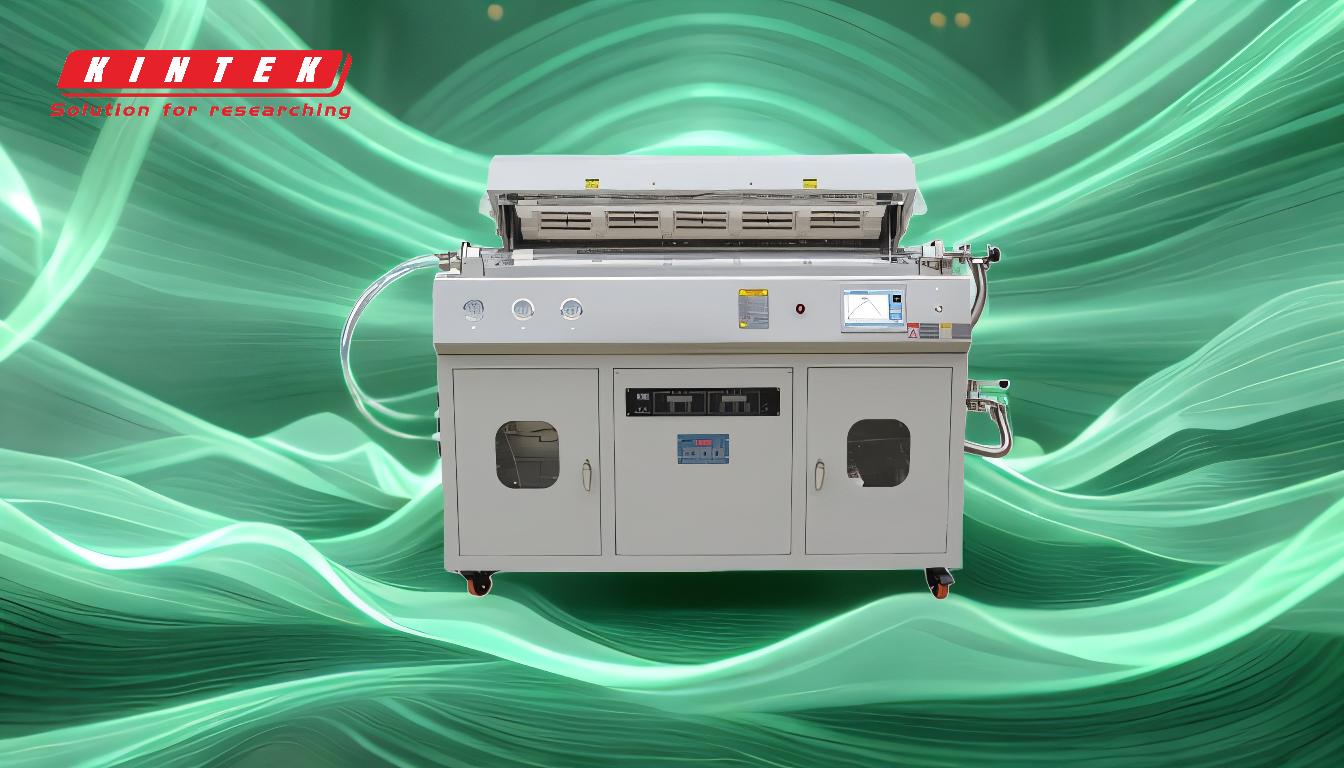
-
Plasma Generation and Reactant Decomposition:
- In PECVD, plasma is generated using a radio frequency (RF) power source, typically operating at 13.56 MHz. This plasma excites the reactant gases, such as SiH4 and NH3, breaking them down into reactive species like ions, radicals, and other active groups.
- The plasma operates at reduced gas pressures (50 mtorr to 5 torr), creating an environment where electron and ion densities are high, and electron energies range from 1 to 10 eV. This energetic environment is crucial for decomposing gas molecules at lower temperatures than traditional CVD.
-
Diffusion and Adsorption of Reactive Species:
- Once the reactant gases are decomposed, the reactive species diffuse through the plasma and reach the substrate surface. Some species may interact with other gas molecules or reactive groups to form the chemical groups required for deposition.
- These chemical groups then adsorb onto the substrate surface, where they undergo further reactions to form the desired thin film.
-
Surface Reactions and Film Formation:
- On the substrate surface, the adsorbed reactive species participate in chemical reactions that lead to the formation of a continuous thin film. For example, in the deposition of silicon nitride (SiNx), SiH4 and NH3 react to form SiNx and release by-products such as hydrogen gas.
- The film grows as more reactive species are deposited and react on the surface, forming a uniform and adherent coating.
-
Advantages of PECVD:
- Low Substrate Temperature: PECVD operates at temperatures between 350-600 ℃, significantly lower than traditional CVD, making it suitable for temperature-sensitive substrates.
- Low Film Stress: The films deposited by PECVD typically have low intrinsic stress, which is beneficial for applications requiring mechanical stability.
- Large-Area Deposition: PECVD can deposit films onto large-area substrates, making it ideal for applications like photovoltaic cells and flat-panel displays.
- Thick Coatings: Unlike conventional CVD, PECVD can deposit thick coatings (>10 μm) without compromising film quality.
-
Comparison with PVD:
- While PECVD relies on chemical reactions in the gas phase, Physical Vapor Deposition (PVD) involves the physical excitation of a target material to form a vapor, which then reacts with a gas to form a compound deposited on the substrate.
- PECVD is generally preferred for applications requiring precise control over film composition and properties, whereas PVD is often used for metallic or alloy coatings.
-
Applications in Photovoltaics:
- In photovoltaic cells, PECVD is used to deposit anti-reflective coatings like silicon nitride (SiNx) on silicon wafers. This improves light absorption and enhances the efficiency of solar cells.
- The process involves placing the silicon wafer on a lower electrode, injecting reactant gases, and using plasma to form a uniform SiNx layer.
By leveraging plasma to enable low-temperature deposition, PECVD offers a versatile and efficient method for producing high-quality thin films across various industries. Its ability to deposit films with precise control over composition and properties makes it a cornerstone of modern manufacturing processes.
Summary Table:
Key Aspect | Details |
---|---|
Plasma Generation | RF power source (13.56 MHz) excites gases, creating reactive species. |
Reactive Species Formation | Gases like SiH4 and NH3 decompose into ions, radicals, and active groups. |
Film Formation | Reactive species diffuse to the substrate, adsorb, and form a thin film. |
Temperature Range | Operates at 350-600 ℃, lower than traditional CVD. |
Applications | Semiconductors, photovoltaics, optics, and large-area coatings. |
Advantages | Low substrate temperature, low film stress, large-area deposition. |
Discover how PECVD can enhance your manufacturing process—contact our experts today!