The PVD sputtering process is a widely used technique for depositing thin films of material onto a substrate. It involves bombarding a target material with high-energy ions, typically argon gas ions, to eject atoms from the target. These ejected atoms then travel through a vacuum chamber and condense onto a substrate, forming a thin film. This process is highly controllable and is used in various industries, including semiconductors, optics, and coatings, to create precise and high-quality thin films.
Key Points Explained:
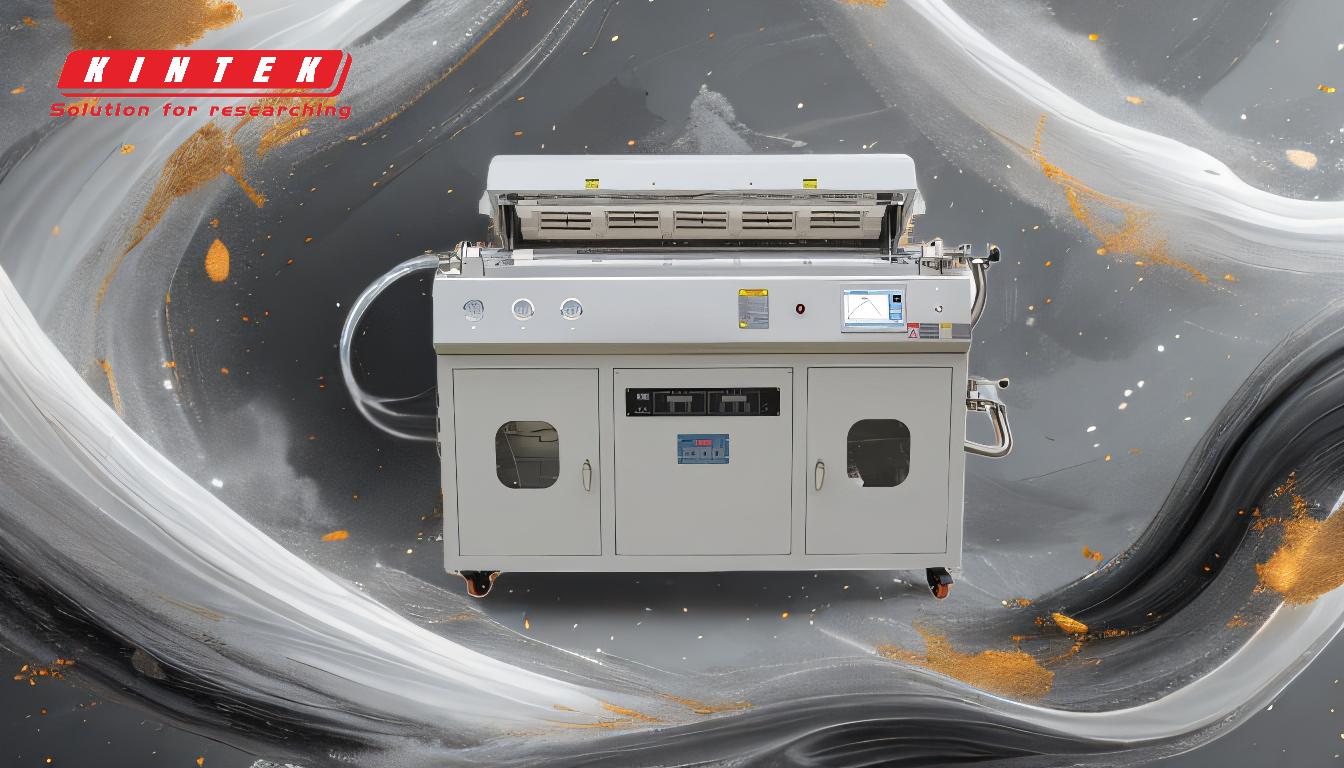
-
Overview of PVD Sputtering:
- PVD sputtering is a type of physical vapor deposition (PVD) where a target material is bombarded with high-energy ions, causing atoms to be ejected from the target.
- These ejected atoms travel through a vacuum environment and deposit onto a substrate, forming a thin film.
- The process is widely used in industries requiring precise and high-quality thin films, such as semiconductors, optics, and decorative coatings.
-
Key Components of the PVD Sputtering Process:
- Target Material: The material to be deposited as a thin film. It is typically a solid material, such as metals, alloys, or ceramics.
- Substrate: The surface onto which the thin film is deposited. It can be made of various materials, including silicon wafers, glass, or polymers.
- Vacuum Chamber: The environment where the sputtering process takes place. A vacuum is necessary to minimize contamination and ensure the efficient transport of ejected atoms.
- Ion Source: Typically, argon gas is ionized to create high-energy ions that bombard the target material. Other gases, such as nitrogen or oxygen, can be used for reactive sputtering to form compound films.
-
Step-by-Step Process of PVD Sputtering:
-
Step 1: Ion Generation:
- Argon gas is introduced into the vacuum chamber and ionized using an electrical discharge, creating a plasma of high-energy argon ions.
-
Step 2: Bombardment of the Target:
- The high-energy argon ions are accelerated toward the target material, colliding with its surface and ejecting atoms through a process called sputtering.
-
Step 3: Transport of Ejected Atoms:
- The ejected atoms travel through the vacuum chamber toward the substrate. The vacuum environment ensures minimal collisions with other particles, allowing for a uniform deposition.
-
Step 4: Condensation on the Substrate:
- The ejected atoms condense onto the substrate, forming a thin film. The film's properties, such as thickness and uniformity, can be controlled by adjusting process parameters like ion energy, pressure, and deposition time.
-
Step 1: Ion Generation:
-
Types of Sputtering Techniques:
- DC Sputtering: Uses a direct current (DC) power source to generate ions. It is commonly used for conductive target materials.
- RF Sputtering: Uses a radio frequency (RF) power source, which allows for the deposition of insulating materials.
- Magnetron Sputtering: Incorporates a magnetic field to enhance the ionization of gas and increase the deposition rate. It is widely used for high-quality thin films.
- Reactive Sputtering: Involves the introduction of reactive gases, such as oxygen or nitrogen, to form compound films (e.g., oxides or nitrides) during deposition.
-
Advantages of PVD Sputtering:
- High Precision: Allows for the deposition of thin films with precise control over thickness and composition.
- Versatility: Can deposit a wide range of materials, including metals, alloys, and ceramics.
- High-Quality Films: Produces films with excellent adhesion, uniformity, and density.
- Scalability: Suitable for both small-scale laboratory applications and large-scale industrial production.
-
Applications of PVD Sputtering:
- Semiconductors: Used to deposit thin films for integrated circuits, solar cells, and displays.
- Optics: Applied in the production of anti-reflective coatings, mirrors, and optical filters.
- Decorative Coatings: Used to create durable and aesthetically pleasing coatings on consumer products.
- Hard Coatings: Provides wear-resistant coatings for tools and machinery.
-
Challenges and Considerations:
- Cost: The equipment and materials for PVD sputtering can be expensive.
- Complexity: Requires careful control of process parameters to achieve desired film properties.
- Contamination: Maintaining a clean vacuum environment is critical to avoid impurities in the deposited film.
In summary, PVD sputtering is a versatile and precise technique for depositing thin films, with applications across various industries. By understanding the process, components, and techniques, users can optimize the deposition of high-quality thin films for their specific needs.
Summary Table:
Aspect | Details |
---|---|
Process Overview | Bombarding a target material with high-energy ions to deposit a thin film. |
Key Components | Target material, substrate, vacuum chamber, ion source (e.g., argon gas). |
Types of Sputtering | DC, RF, Magnetron, and Reactive Sputtering. |
Advantages | High precision, versatility, high-quality films, and scalability. |
Applications | Semiconductors, optics, decorative coatings, and hard coatings. |
Challenges | High cost, process complexity, and contamination risks. |
Ready to optimize your thin film deposition process? Contact us today for expert guidance!