Sputter coating is a physical vapor deposition (PVD) technique used to deposit thin films of material onto a substrate. It operates in a vacuum environment where a target material is bombarded by high-energy ions, typically argon, causing atoms to be ejected from the target and deposited onto the substrate. The process involves creating a plasma, accelerating ions toward the target, and managing heat through specialized cooling systems. This method is widely used in industries such as electronics, optics, and materials science due to its ability to produce uniform, high-quality coatings with strong atomic-level bonds.
Key Points Explained:
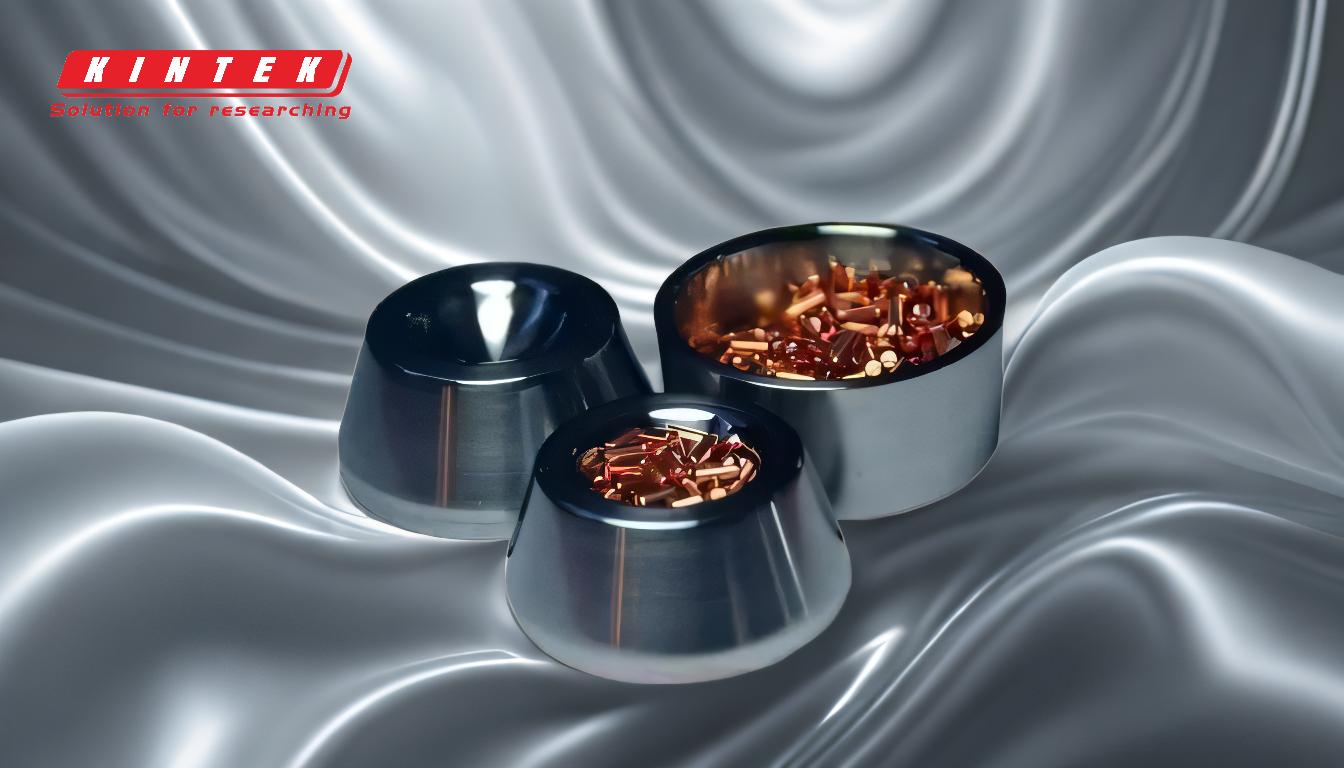
-
Vacuum Environment:
- Sputter coating takes place in a vacuum chamber to eliminate contaminants and ensure a controlled environment.
- The vacuum reduces the presence of other gases, allowing the inert gas (typically argon) to dominate the process.
-
Creation of Plasma:
- A high voltage is applied to the target material, which acts as the cathode.
- This voltage ionizes the inert gas (argon) in the chamber, creating a plasma consisting of free electrons, positively charged ions, and neutral gas atoms.
- The plasma is essential for generating the energetic ions needed to sputter the target material.
-
Ion Bombardment:
- The positively charged argon ions are accelerated toward the negatively charged target (cathode) due to the electric field.
- When these high-energy ions strike the target, they transfer their momentum to the target atoms, causing them to be ejected from the surface in a process called sputtering.
-
Deposition of Thin Film:
- The ejected target atoms travel through the vacuum and deposit onto the substrate, forming a thin film.
- The deposition process is highly controlled, allowing for uniform and precise coating thicknesses.
-
Magnetic Fields and Uniform Erosion:
- Magnets are often used to confine and concentrate the plasma, enhancing the efficiency of the sputtering process.
- These magnetic fields ensure stable and uniform erosion of the target material, which is critical for consistent film quality.
-
Heat Management:
- The sputtering process generates significant heat due to the high-energy collisions.
- Specialized cooling systems are employed to manage this heat and prevent damage to the target, substrate, and equipment.
-
Applications and Advantages:
- Sputter coating is used in various industries, including semiconductor manufacturing, optical coatings, and decorative finishes.
- It offers advantages such as excellent adhesion, high purity, and the ability to deposit a wide range of materials, including metals, alloys, and ceramics.
By understanding these key points, one can appreciate the complexity and precision of the sputter coating process, making it a valuable technique for creating high-performance thin films in advanced manufacturing and research applications.
Summary Table:
Key Aspect | Description |
---|---|
Vacuum Environment | Ensures a contaminant-free, controlled environment for precise coating. |
Creation of Plasma | High voltage ionizes argon gas, creating a plasma for ion generation. |
Ion Bombardment | Argon ions strike the target, ejecting atoms for deposition. |
Deposition of Thin Film | Ejected atoms form a uniform, high-quality coating on the substrate. |
Magnetic Fields | Enhances plasma efficiency and ensures uniform target erosion. |
Heat Management | Cooling systems manage heat to protect equipment and maintain process stability. |
Applications | Used in semiconductors, optics, and decorative finishes for durable coatings. |
Discover how sputter coating can elevate your manufacturing process—contact our experts today!