Temperature is a critical factor in pyrolysis, as it directly influences the type and quality of the products generated. Pyrolysis is a thermal decomposition process that occurs in the absence of oxygen, and its outcomes vary significantly depending on the temperature range and heating rate. At low temperatures (below 450°C), pyrolysis primarily produces biochar, a solid residue. At intermediate temperatures, bio-oil is the dominant product, while high temperatures (above 800°C) favor the production of gases. The heating rate and residence time also play crucial roles in determining the final product distribution. Understanding these temperature-dependent effects is essential for optimizing pyrolysis processes for specific applications, such as energy production or waste management.
Key Points Explained:
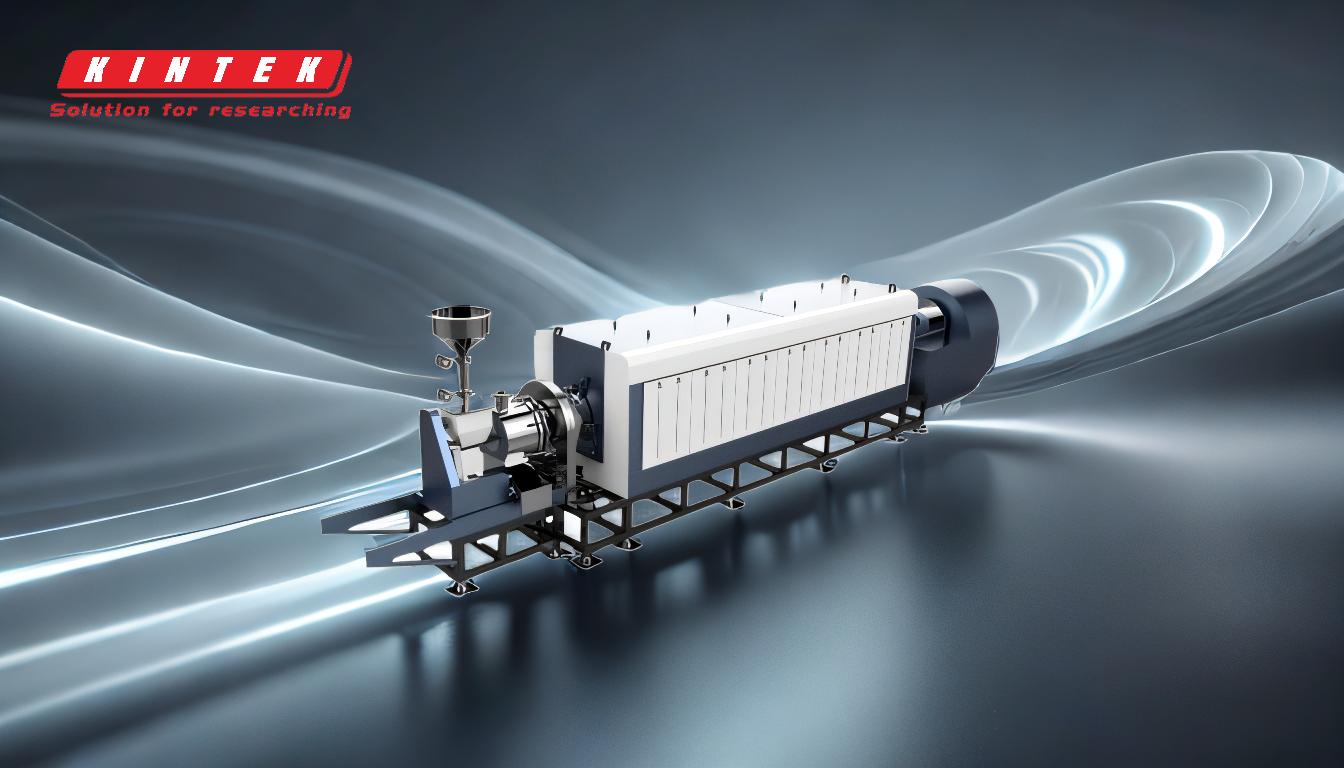
-
Temperature Ranges and Product Distribution:
-
Low Temperatures (Below 450°C):
- At low temperatures, pyrolysis primarily yields biochar, a solid carbon-rich residue.
- Slow heating rates are typically used in this range, allowing for more complete carbonization of the feedstock.
- Biochar is often used in agriculture as a soil amendment due to its ability to improve soil fertility and sequester carbon.
-
Intermediate Temperatures (450–800°C):
- In this range, pyrolysis produces bio-oil, a liquid product rich in organic compounds.
- Relatively high heating rates are employed to maximize bio-oil yield.
- Bio-oil can be used as a renewable fuel or further refined into chemicals.
-
High Temperatures (Above 800°C):
- High temperatures favor the production of non-condensable gases, such as hydrogen, methane, and carbon monoxide.
- Rapid heating rates are used to enhance gas production.
- These gases can be utilized as a source of energy or as feedstocks for chemical synthesis.
-
Low Temperatures (Below 450°C):
-
Heating Rate and Its Influence:
- The heating rate determines how quickly the feedstock reaches the desired pyrolysis temperature.
- Slow heating rates (common in low-temperature pyrolysis) promote the formation of biochar by allowing more time for carbonization.
- Fast heating rates (common in high-temperature pyrolysis) favor the production of gases by rapidly breaking down the feedstock into smaller molecules.
- Intermediate heating rates are optimal for bio-oil production, as they balance the decomposition of the feedstock and the condensation of vapors.
-
Residence Time and Thermal Conversion:
- Residence time refers to the duration the feedstock remains in the pyrolysis chamber.
- Longer residence times at lower temperatures enhance the production of high-quality biochar.
- Shorter residence times at higher temperatures increase the yield of gases and reduce the formation of solid residues.
- The residence time also affects the composition of the vapors, influencing the quality of bio-oil.
-
Feedstock Composition and Its Role:
- The type of feedstock (e.g., biomass, tires, plastics) significantly impacts the pyrolysis process.
- Different components of the feedstock decompose at varying temperatures, affecting the overall product distribution.
- For example, biomass with high cellulose content tends to produce more bio-oil, while lignin-rich biomass yields more biochar.
-
Practical Implications for Equipment and Consumables Purchasers:
-
For Biochar Production:
- Purchasers should look for pyrolysis systems designed for low-temperature operation with slow heating rates.
- Equipment should have sufficient residence time to ensure complete carbonization.
-
For Bio-Oil Production:
- Systems should be capable of operating at intermediate temperatures with controlled heating rates.
- Condensation units are essential for capturing and collecting the bio-oil vapors.
-
For Gas Production:
- High-temperature pyrolysis systems with rapid heating rates are ideal.
- Gas collection and purification systems should be included to maximize the utility of the produced gases.
-
For Biochar Production:
-
Temperature Control and Optimization:
- Precise temperature control is crucial for achieving the desired product distribution.
- Advanced pyrolysis systems often include temperature sensors and automated controls to maintain optimal conditions.
- Purchasers should prioritize equipment with robust temperature regulation features to ensure consistent results.
-
Environmental and Economic Considerations:
- Lower-temperature pyrolysis is generally more energy-efficient and produces fewer emissions.
- High-temperature pyrolysis, while energy-intensive, can generate valuable gases for energy recovery.
- The choice of pyrolysis temperature should align with the intended application and economic goals.
By understanding how temperature affects pyrolysis, purchasers can select the appropriate equipment and consumables to achieve their desired outcomes, whether for biochar, bio-oil, or gas production.
Summary Table:
Temperature Range | Primary Product | Key Characteristics | Applications |
---|---|---|---|
Below 450°C | Biochar | Solid, carbon-rich | Soil amendment, carbon sequestration |
450–800°C | Bio-Oil | Liquid, organic-rich | Renewable fuel, chemical refining |
Above 800°C | Gases | Non-condensable (H2, CH4, CO) | Energy recovery, chemical synthesis |
Heating Rate | Effect | ||
Slow | Promotes biochar | Longer carbonization | Biochar production |
Intermediate | Maximizes bio-oil | Balanced decomposition | Bio-oil production |
Fast | Enhances gas yield | Rapid breakdown | Gas production |
Residence Time | Effect | ||
Long | High-quality biochar | Complete carbonization | Biochar production |
Short | Increased gas yield | Reduced solid residues | Gas production |
Ready to optimize your pyrolysis process? Contact our experts today for tailored solutions!