PVD (Physical Vapor Deposition) coating is a highly advanced and durable surface finishing technique that significantly enhances the hardness, wear resistance, and lifespan of materials. It is particularly known for its ability to create thin, hard coatings ranging from 0.5 to 5 microns in thickness, which are applied to metals like stainless steel. PVD coatings are four times harder than chrome, making them exceptionally resistant to scratches, corrosion, and oxidation. This makes them ideal for applications in harsh environments, such as automotive parts, industrial tools, and coastal projects. Additionally, PVD coatings are environmentally friendly, operate at lower temperatures, and are suitable for precision tools and complex components, offering both practical and ethical advantages over traditional coating methods like chrome plating.
Key Points Explained:
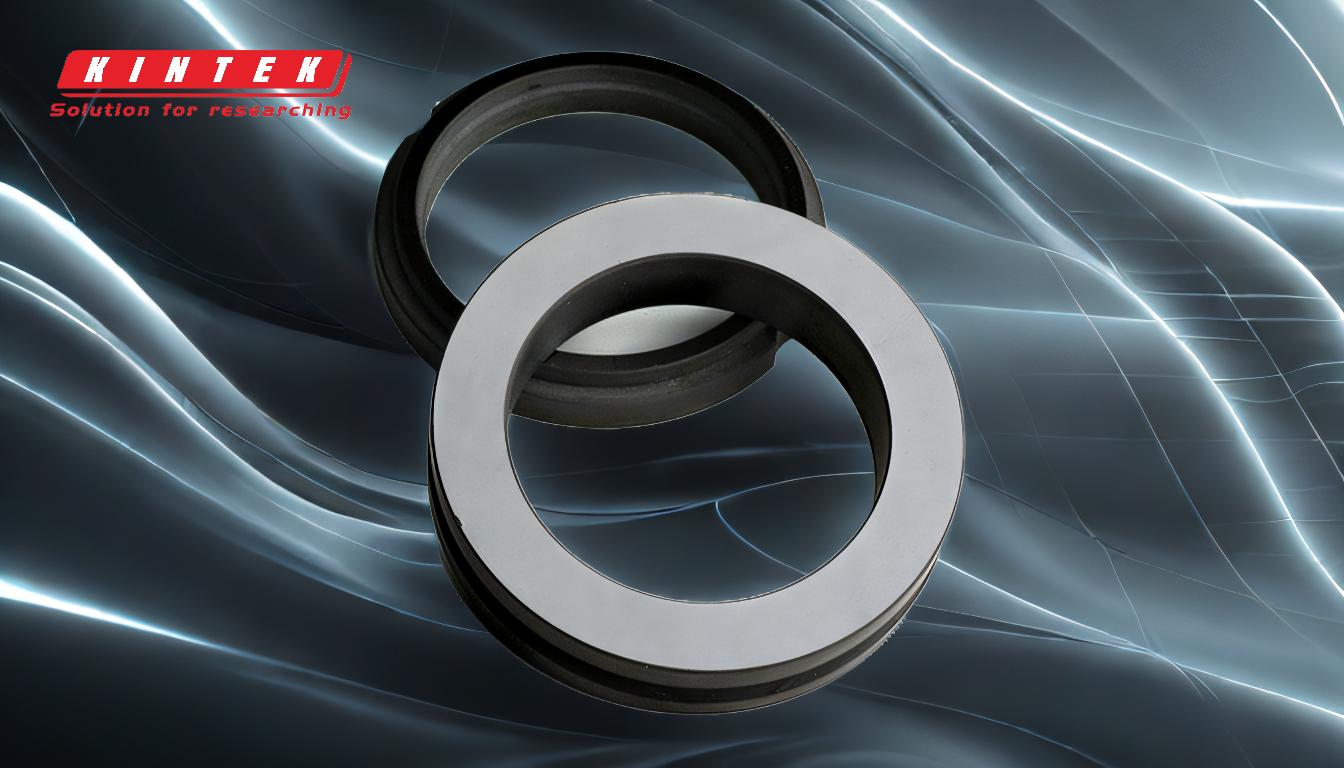
-
Hardness of PVD Coatings:
- PVD coatings are four times harder than chrome, making them highly resistant to scratches and wear. This hardness is achieved through the molecular-level alteration of the metal surface during the coating process.
- The hardness of PVD coatings makes them ideal for applications requiring durability, such as cutting tools, automotive components, and industrial machinery.
-
Thickness and Durability:
- PVD coatings are extremely thin, typically ranging from 0.5 to 5 microns. Despite their thinness, they provide exceptional durability and longevity.
- The thinness of the coating preserves the sharpness of tools, such as blades, and reduces cutting force and heat during use.
-
Resistance to Corrosion and Oxidation:
- PVD coatings are highly resistant to corrosion and oxidation, making them suitable for use in harsh environments, such as coastal areas or industrial settings.
- This resistance extends the lifespan of coated products, reducing the need for frequent replacements or maintenance.
-
Environmental and Practical Benefits:
- PVD coating is an environmentally friendly alternative to traditional processes like chrome plating, which produces toxic byproducts.
- The process operates at lower temperatures (around 500 °C), reducing the risk of thermal damage to the substrate and minimizing material distortion.
-
Versatility in Applications:
- PVD coatings are suitable for a wide range of applications, including high-speed steel (HSS) and carbide cutting tools, plastic injection molding components, fine blanking tools, and optical coatings.
- The process is compatible with both high-volume manufacturing and small batch production, making it versatile for various industries.
-
Advantages Over Traditional Coatings:
- PVD coatings offer superior hardness, wear resistance, and durability compared to traditional coatings like chrome plating.
- The compressive stress formed during cooling prevents crack formation and expansion, making PVD coatings ideal for interrupted cutting processes like milling.
-
Operational Efficiency:
- PVD coating machines are computer-controlled, allowing for precise and consistent application of coatings. This reduces production costs and turnaround time.
- The fast deposition speed and low deposition temperature of PVD machines make them efficient and suitable for coating complex and precision tools.
In summary, PVD coating is a highly effective and versatile surface finishing technique that offers superior hardness, durability, and resistance to corrosion and oxidation. Its environmental benefits, combined with its ability to enhance the lifespan and performance of products, make it a preferred choice for a wide range of industrial and commercial applications.
Summary Table:
Aspect | Details |
---|---|
Hardness | 4x harder than chrome, ideal for durable applications. |
Thickness | 0.5 to 5 microns, thin yet highly durable. |
Corrosion Resistance | Excellent resistance to corrosion and oxidation, suitable for harsh environments. |
Environmental Impact | Eco-friendly, operates at lower temperatures (≈500 °C). |
Applications | Cutting tools, automotive parts, industrial machinery, and more. |
Enhance your products with PVD coating's superior durability—contact us today to learn more!