Test sieve calibration is a critical process to ensure the accuracy and reliability of sieves used in particle size analysis. It involves a combination of visual inspection, cleaning, and statistical verification to confirm that the sieve meets the required standards. Calibration ensures that the sieve's mesh openings are uniform and comply with applicable standards like ASTM E11 and ISO 3310-1. The process includes steps such as visual examination for defects, cleaning to remove particles, and statistical analysis to predict overall conformance. Regular re-verification is also essential to maintain the sieve's performance over time.
Key Points Explained:
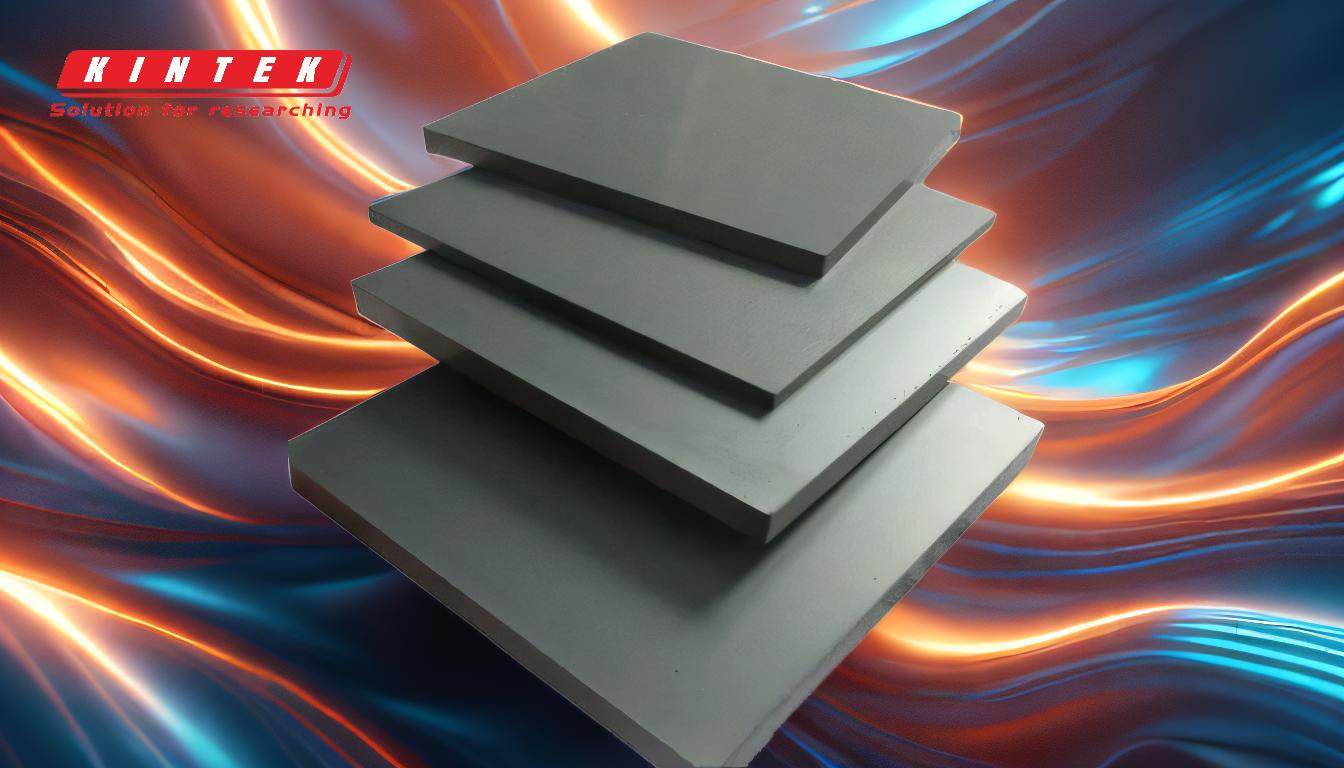
-
Visual Inspection
- The first step in calibrating a test sieve is a thorough visual examination.
- Inspect the sieve for physical defects such as tears in the mesh, wavy mesh patterns, or cracks in the epoxy that secures the mesh to the frame.
- Any defects can compromise the sieve's accuracy and must be addressed before proceeding with further calibration steps.
-
Cleaning the Sieve
- Proper cleaning is essential to ensure that no particles from previous uses interfere with calibration.
- Steps for cleaning include:
- Turning the sieve over a receiving pan to collect dislodged particles.
- Gently brushing the underside of the mesh in a circular motion to remove trapped particles.
- Tapping the sieve frame with the brush handle to dislodge clinging particles.
- Washing the sieve in warm water with mild detergent to remove residual debris.
- Allowing the sieve to dry completely before use to prevent moisture-related errors.
-
Statistical Verification of Aperture Uniformity
- The accuracy of a test sieve depends on the uniformity of its mesh openings.
- Both the wire cloth weaver and the sieve manufacturer must maintain rigorous quality control programs to ensure compliance with standards.
- During calibration, a certain number of apertures are measured, and statistical forecasting is used to predict overall conformance.
- Standards like ASTM E11 and ISO 3310-1 classify sieves into three levels of accuracy based on this statistical analysis.
-
Re-verification for Used Sieves
- Re-verification is a process similar to the initial calibration but is performed on used sieves to check their ongoing performance.
- This step is crucial for maintaining accuracy over time and can be part of an internal quality control or quality assurance program.
- The process involves the same steps as initial calibration, including visual inspection, cleaning, and statistical analysis.
-
Compliance with Standards
- Test sieves must comply with recognized standards such as ASTM E11 and ISO 3310-1.
- These standards specify the requirements for sieve construction, including the permissible variations in aperture size and the methods for verifying compliance.
- Adhering to these standards ensures that sieves provide consistent and reliable results across different applications and laboratories.
By following these steps, test sieve calibration ensures that the sieve performs accurately and reliably, providing consistent results for particle size analysis. Regular calibration and re-verification are essential to maintain the sieve's performance and compliance with industry standards.
Summary Table:
Step | Description |
---|---|
Visual Inspection | Examine the sieve for defects like tears, wavy mesh, or cracks in the epoxy. |
Cleaning the Sieve | Remove particles by brushing, tapping, washing, and drying the sieve thoroughly. |
Statistical Verification | Measure aperture uniformity and predict conformance using statistical methods. |
Re-verification | Perform regular checks on used sieves to maintain accuracy over time. |
Compliance with Standards | Ensure adherence to ASTM E11 and ISO 3310-1 for consistent results. |
Ensure your test sieves meet industry standards—contact us today for expert calibration services!