Alumina ceramic is a high-performance material widely used in industries due to its excellent mechanical, thermal, and electrical properties. The manufacturing process involves several precise steps to ensure the final product meets stringent quality standards. The process typically begins with the preparation of a ceramic slurry, followed by shaping, drying, binder removal, sintering, and post-processing. Each step is critical to achieving the desired properties of the final alumina ceramic product. Below, the key steps and their significance are explained in detail.
Key Points Explained:
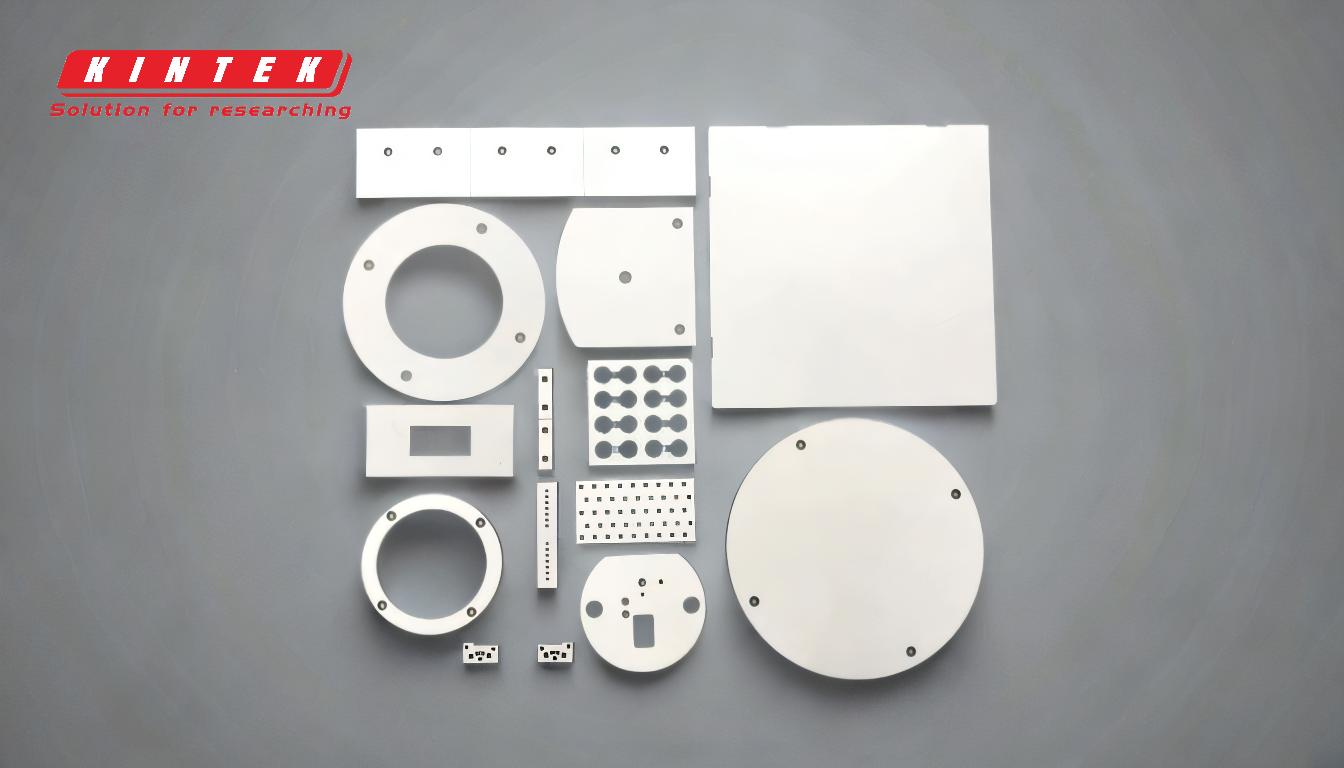
-
Preparation of Ceramic Slurry
- Ingredients: The process starts by mixing alumina powder with water, a binder, and a deflocculant. The binder helps hold the particles together, while the deflocculant ensures the slurry remains stable and homogeneous.
- Purpose: This step ensures the ceramic particles are evenly distributed, which is crucial for achieving uniform properties in the final product.
- Outcome: The slurry is a liquid mixture ready for the next stage of processing.
-
Spray Drying
- Process: The slurry is sprayed into a hot chamber, where the water evaporates, leaving behind fine, free-flowing granules of alumina powder.
- Purpose: Spray drying converts the slurry into a powder form that is easier to handle and press into molds.
- Outcome: The resulting powder has consistent particle size and flowability, which is essential for uniform compaction.
-
Pressing
- Process: The spray-dried powder is compacted into a mold under high pressure to form a "green body," which is the initial shape of the ceramic part.
- Purpose: Pressing ensures the powder particles are densely packed, reducing porosity and improving mechanical strength.
- Outcome: The green body is a coherent but fragile structure that retains the desired shape.
-
Binder Removal (Debinding)
- Process: The green body is heated at a low temperature to burn off the binder used in the slurry.
- Purpose: Removing the binder prevents defects during sintering and ensures the ceramic particles can bond effectively.
- Outcome: The debound part is now ready for high-temperature sintering.
-
Sintering
- Process: The debound part is heated to a high temperature (typically above 1600°C) in a controlled atmosphere. During sintering, the ceramic particles fuse together, reducing porosity and increasing density.
- Purpose: Sintering transforms the fragile green body into a strong, dense ceramic material with the desired mechanical and thermal properties.
- Outcome: The sintered part is now a solid, durable alumina ceramic component.
-
Post-Processing (Machining and Assembly)
- Machining: After sintering, the ceramic part may require precision machining using diamond tools or ultrasonic methods to achieve tight tolerances and smooth surfaces.
- Assembly: For complex applications, ceramic parts may be metallized and brazed to other components.
- Purpose: Post-processing ensures the final product meets the exact specifications required for its intended use.
- Outcome: The finished alumina ceramic part is ready for deployment in demanding applications.
By following these steps meticulously, manufacturers can produce high-quality alumina ceramics with consistent properties, making them suitable for a wide range of industrial applications, from electronics to aerospace.
Summary Table:
Step | Process | Purpose | Outcome |
---|---|---|---|
Preparation of Slurry | Mixing alumina powder, water, binder, and deflocculant | Ensures even particle distribution for uniform properties | Liquid slurry ready for processing |
Spray Drying | Slurry sprayed into a hot chamber to evaporate water | Converts slurry into free-flowing powder for easy handling | Fine, consistent powder for compaction |
Pressing | Compacting powder into a mold under high pressure | Reduces porosity and improves mechanical strength | Green body with the desired shape |
Binder Removal | Heating green body to burn off binder | Prevents defects and ensures effective particle bonding | Debound part ready for sintering |
Sintering | Heating to high temperature (above 1600°C) in a controlled atmosphere | Fuses particles, reduces porosity, and increases density | Durable, dense alumina ceramic component |
Post-Processing | Machining and assembly (e.g., metallization, brazing) | Ensures final product meets exact specifications | Finished alumina ceramic part for demanding applications |
Learn more about how alumina ceramics can meet your industrial needs—contact our experts today!